HELM Damper Complete 100 Hour Service Instructions (Part 3 of 3)
June 2022 orig.
Table of Contents
Recommendations and Warnings
Cane Creek recommends only trained suspension technicians perform service on all suspension, using all required tools and following all proper procedures. Anyone without access to the proper equipment or with any concerns on the procedures should defer to an authorized Cane Creek service center for service. Improper service can result in loss of performance or suspension failure. All Cane Creek forks have pressurized oil. Follow the service procedures exactly as written to avoid possible injury or harm to the suspension. Always wear eye protection while performing suspension service. Please dispose of all waste products and materials through proper channels to avoid contamination of the environment.
Any damage or issues resulting from improper service will not be covered by warranty. If you have a fork still in its original warranty period and do not wish to void your warranty, please contact an authorized Cane Creek service center.
These service instructions cover the basic service procedures using standard service kits. If your suspension requires parts beyond standard replacement parts – CSU, compression rods, etc. – please consult your authorized Cane Creek service center or contact us at our Cane Creek Support Center.
Service Notes
These instructions cover just the damper leg of a complete 100 hour service. Combine these instructions with the appropriate spring side – air or coil; original or MKII – and 50 hour lower service to get a complete 100 hour fork service.
Additionally, follow these instructions for damper removal and reinstall if sending the damper off for a service with an authorized Cane Creek service center.
Service Kit
BAG0714 – HELM Damper Rebuilt Kit
Required Cane Creek Tools
BAG0405 – Compression Retaining Nut Socket – Thin Walled 11mm socket
AAG0086 – HELM Cartridge Fill Tool
AAG0367 – HELM Oil Seal Head Bullet
AAG0406 – HELM Compression Outer Sleeve Spanner
Additional Tools & Supplies
Allen wrenches – 4mm
Torx wrenches – T10
Sockets – 10mm & chamfer-less 30mm
Crowfoot wrenches – 10 & 18mm
Open Ended Box wrenches – 10 & 18mm
10mm Shaft Clamp
Torque wrenches
Knipex pliers
Pick
Suspension Grease
PolyLube Grease
Motorex 2.5wt Racing Fork Oil
Vacuum Oil Fill Machine
Torque, Loctite, Oil & Nitrogen Specs
Torque & Loctite Chart
Part | Torque Spec | Loctite Spec |
---|---|---|
Rebound Piston Assembly | 3 Nm | 263 (Red) |
Rebound Piston Install | 5 Nm | 243 (Blue) |
Rebound Adjuster | 5 Nm | 243 (Blue) |
Damper Top Cap to Gold Coupling | 9 Nm | None |
Oil Seal Head to Damper Tube | 13 Nm | None |
Damper Install | 36 Nm | 243 (Blue) |
Compression Nut | Hand Tight | 243 (Blue) |
LSC Knob Screw | 1.6 Nm | 243 (Blue) |
Oil Chart
Oil Location | Oil Type | Oil Amount |
---|---|---|
Damper Fill | Motorex 2.5wt Racing Fork Oil | Fill to 2 Bars |
Damper Fill
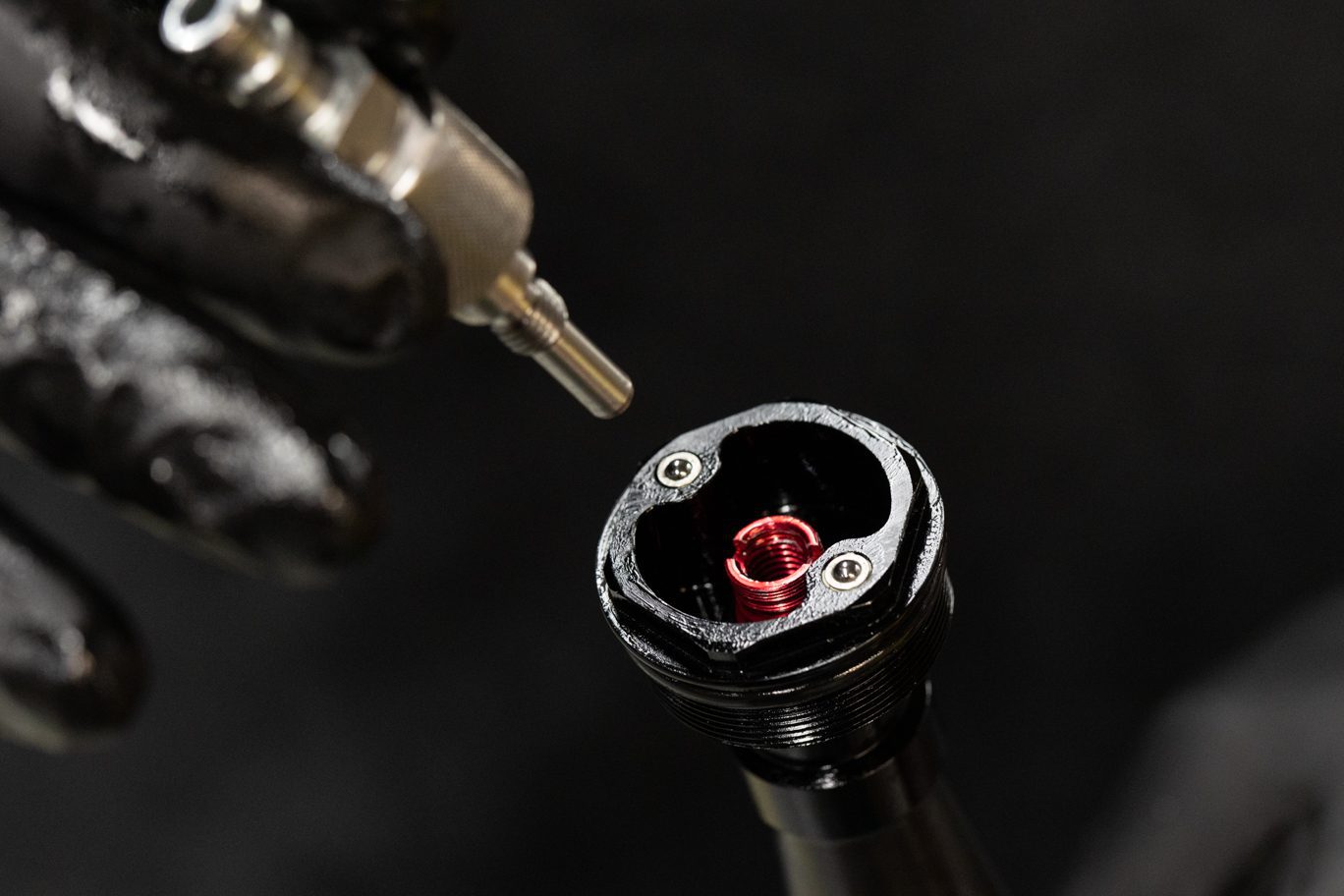
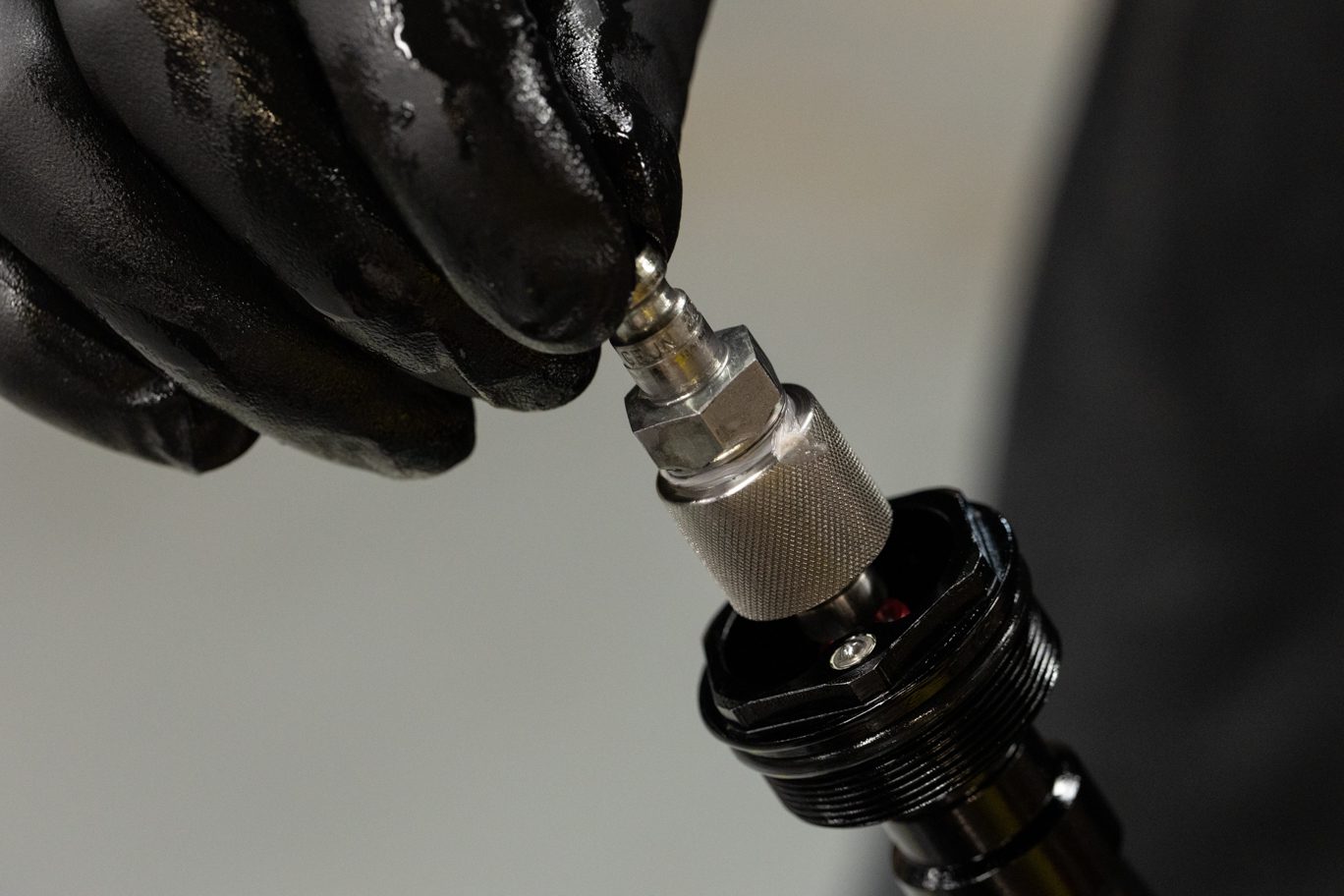
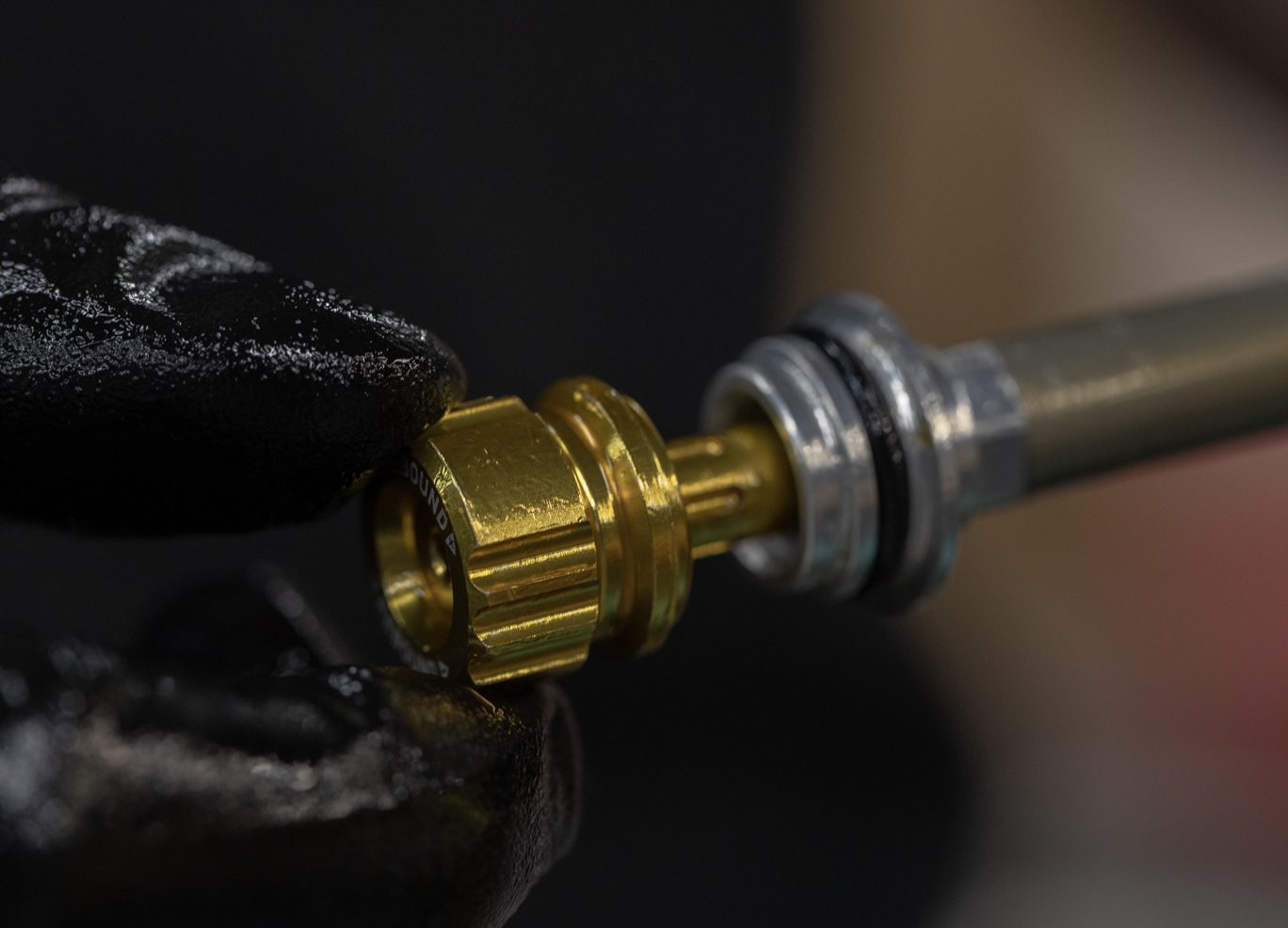
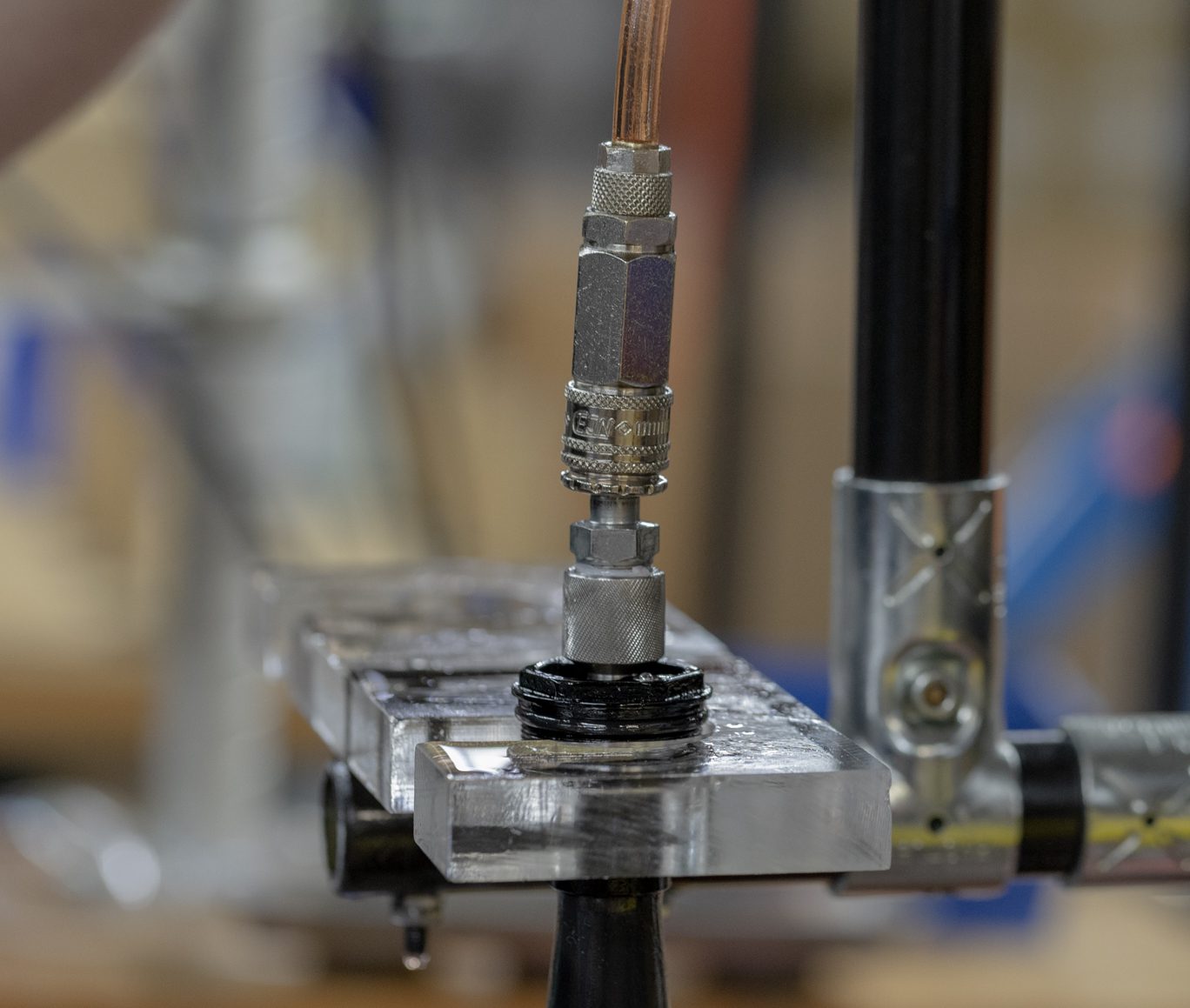
Step 1 – Prepping Damper for Fill
Ensure rebound is open (counterclockwise). Fully compress damper. Attach fill tool to fill machine per your manufacturer’s instructions.
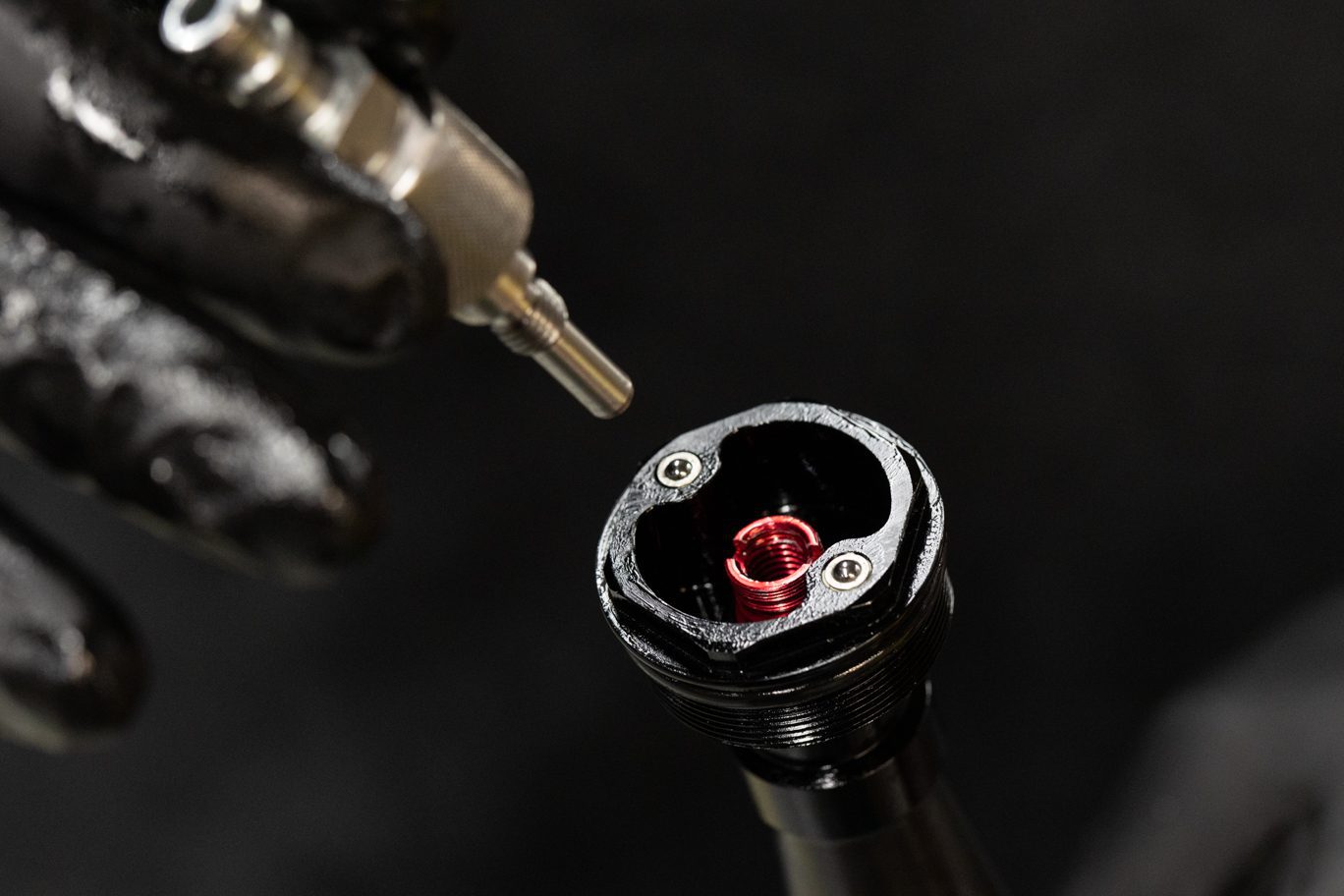
Attaching Fill Tool
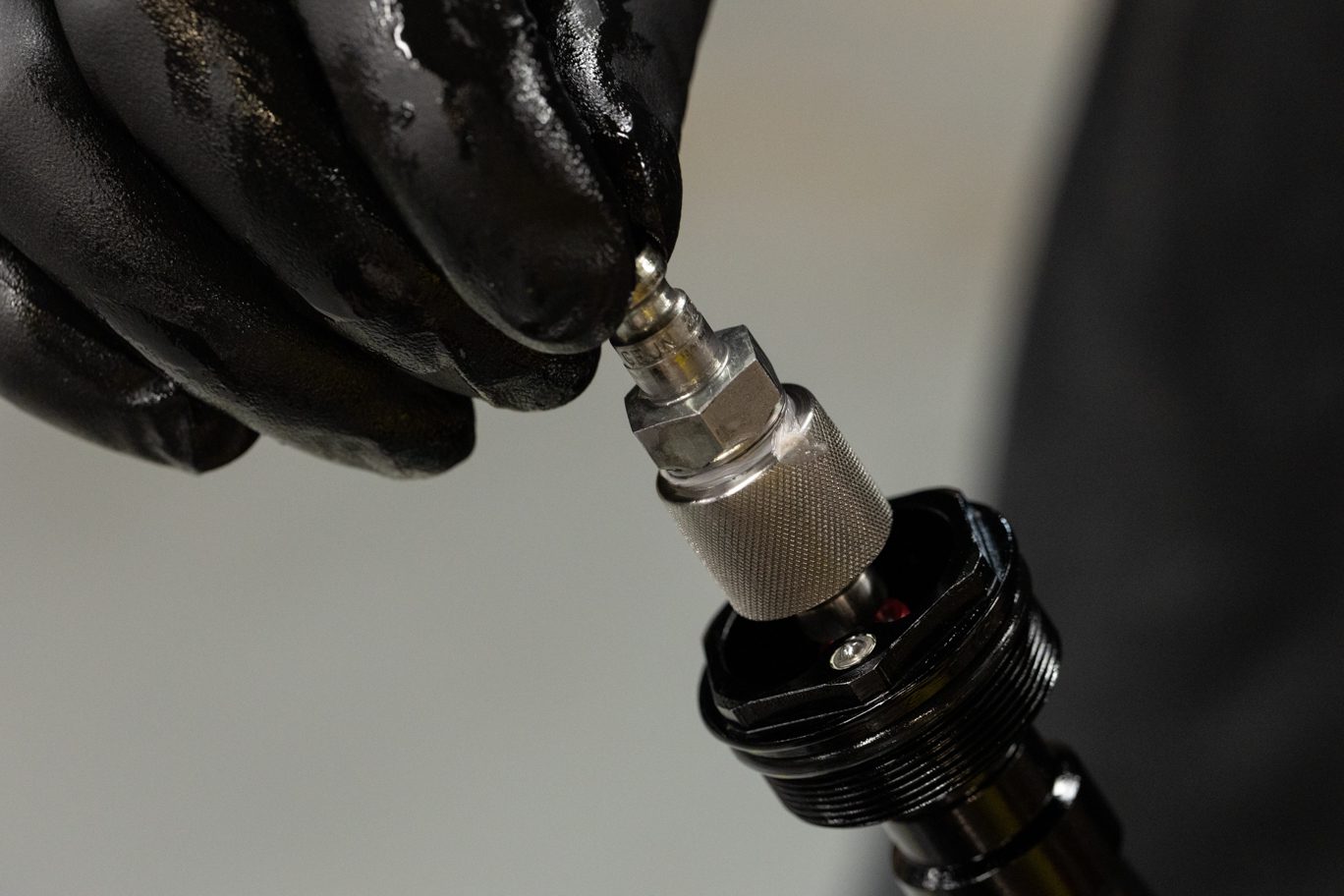
Fill Tool Attached
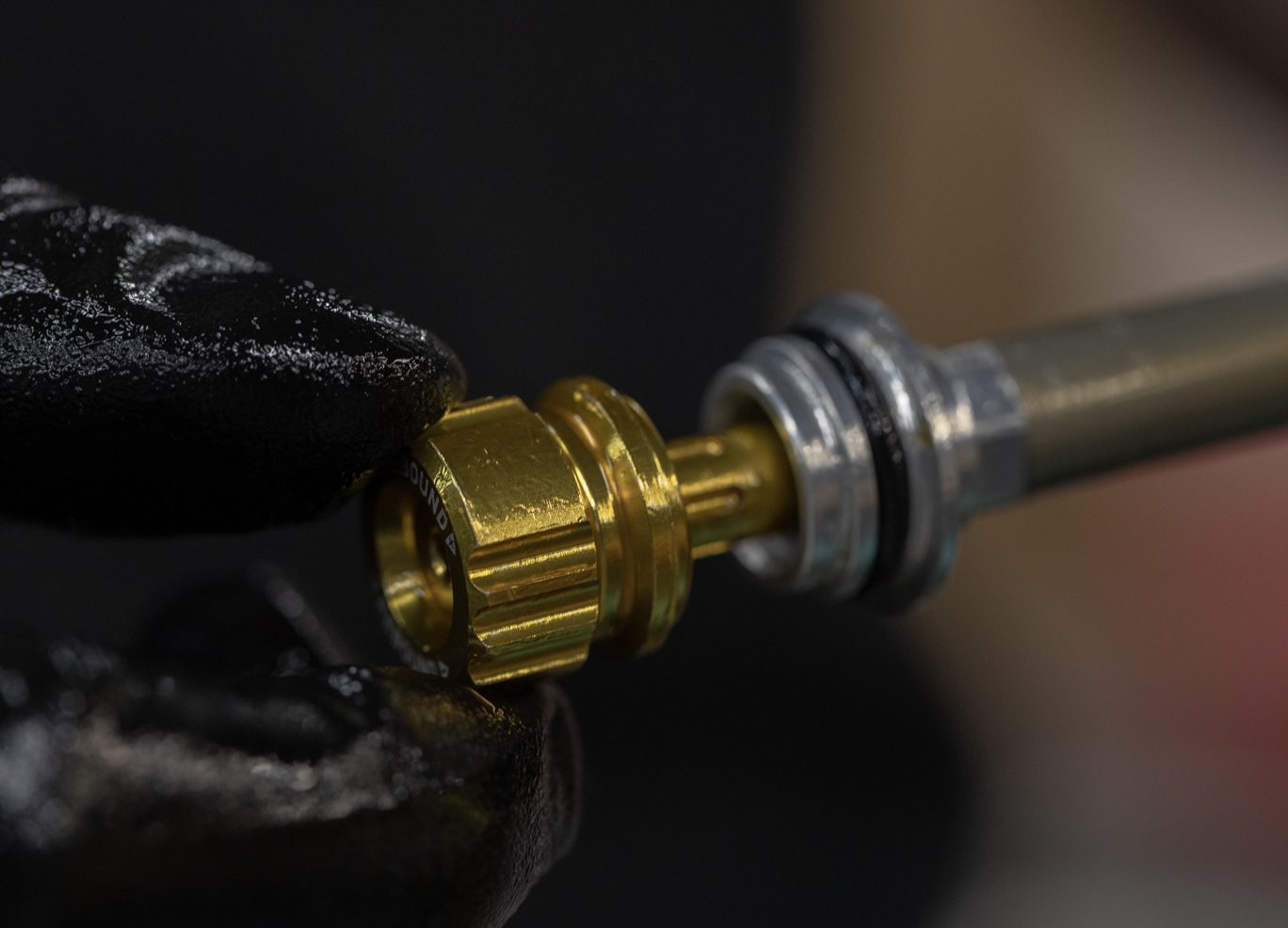
Opening Rebound Completely
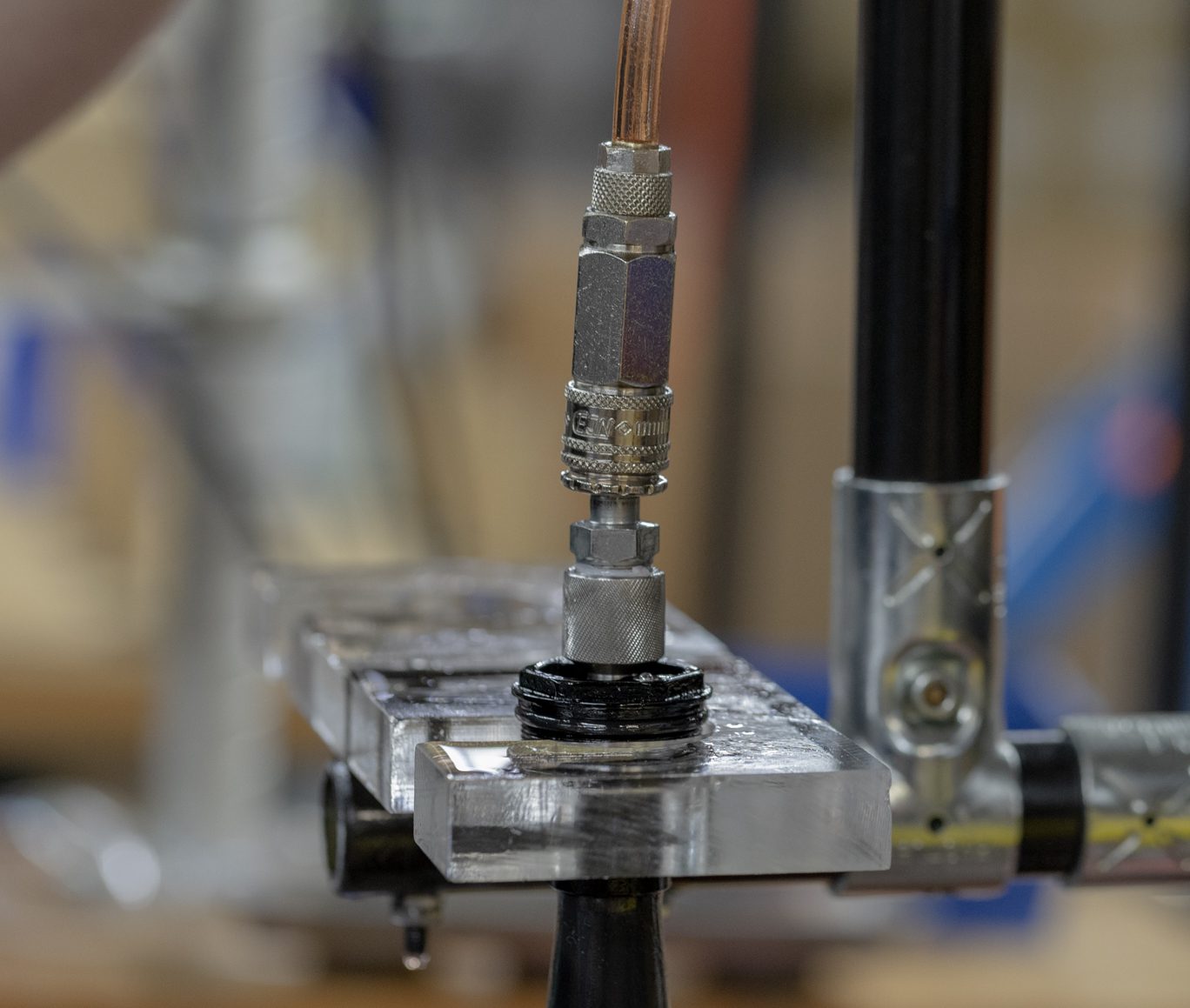
Connected to Fill Machine
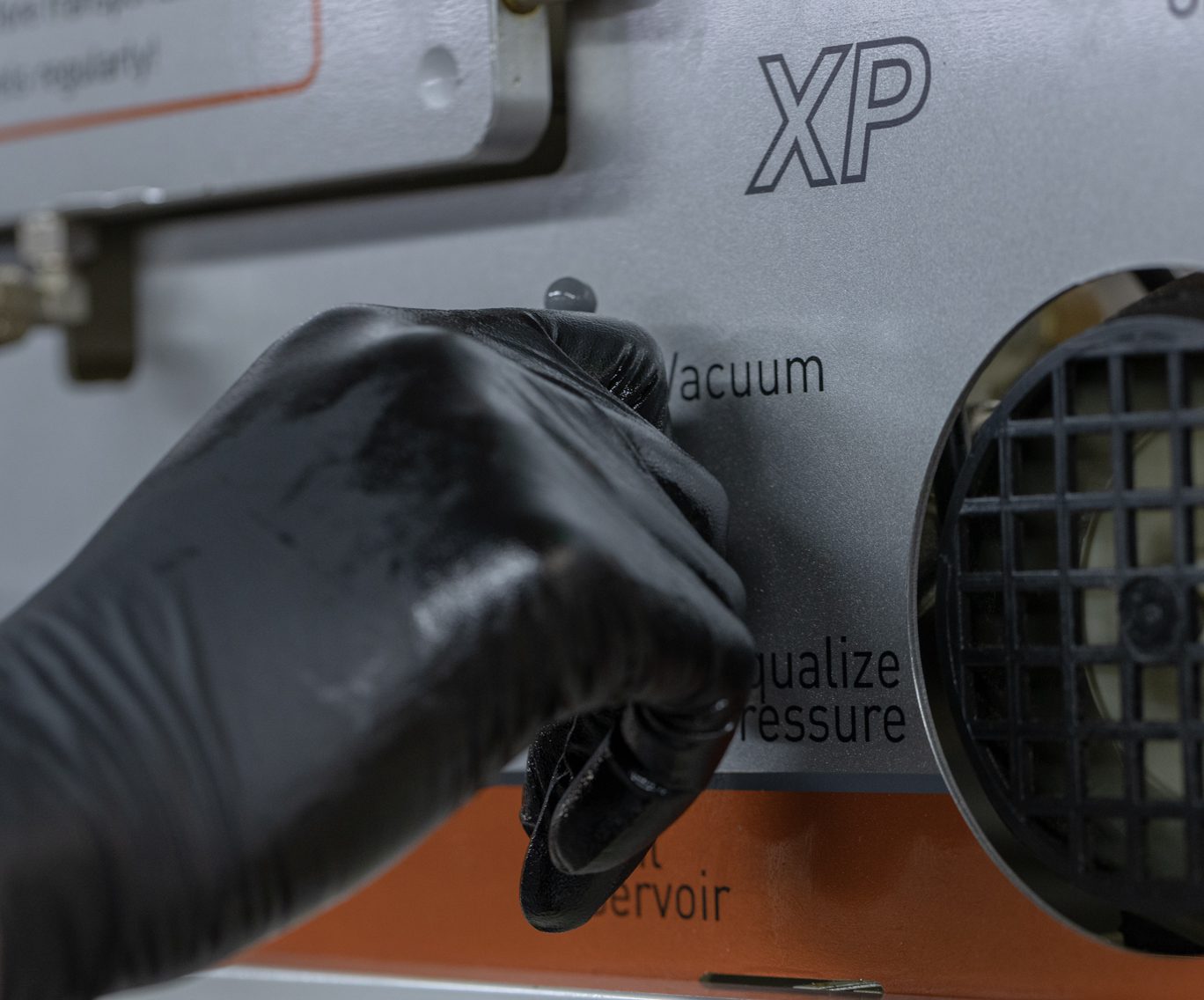
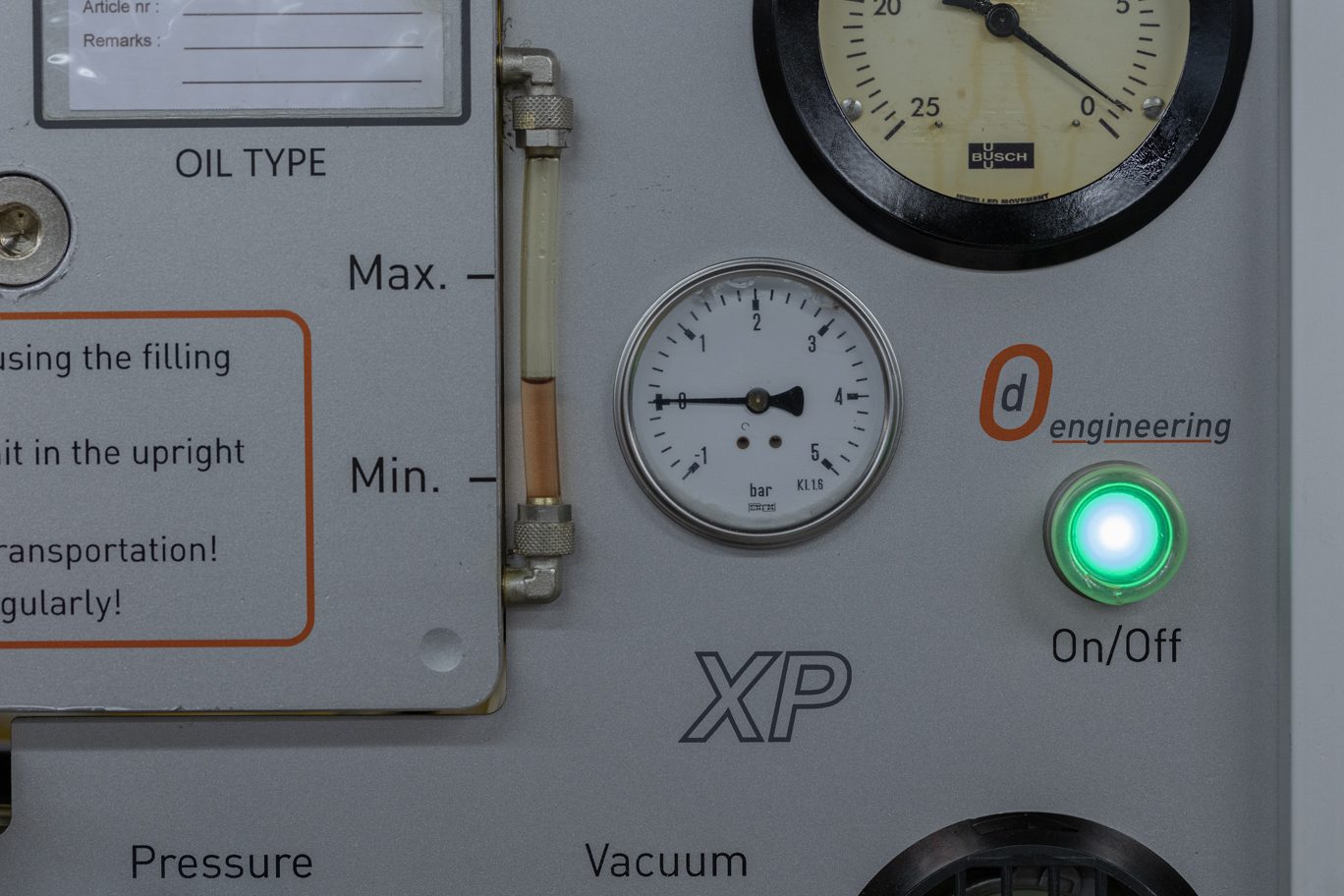
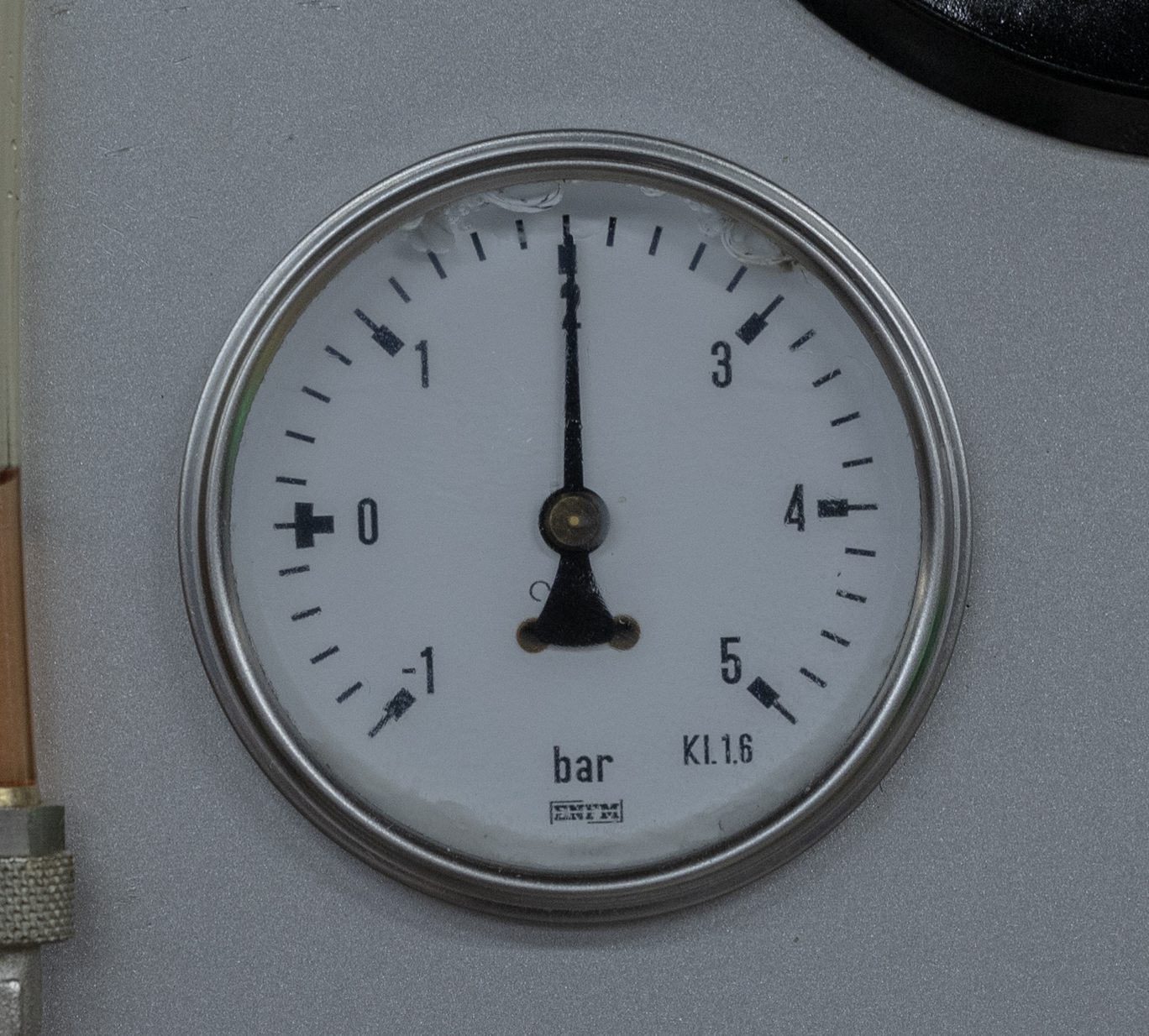
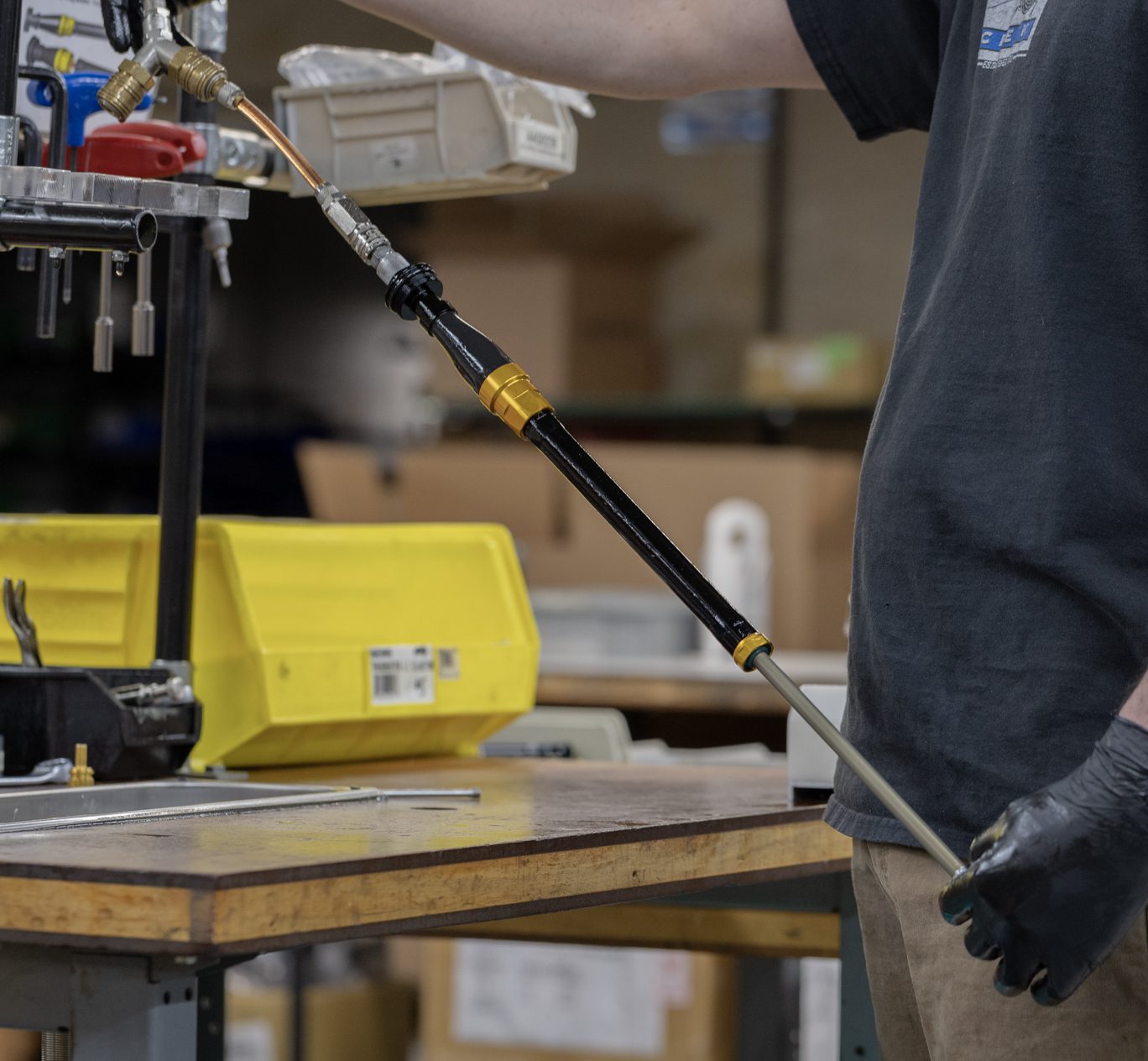
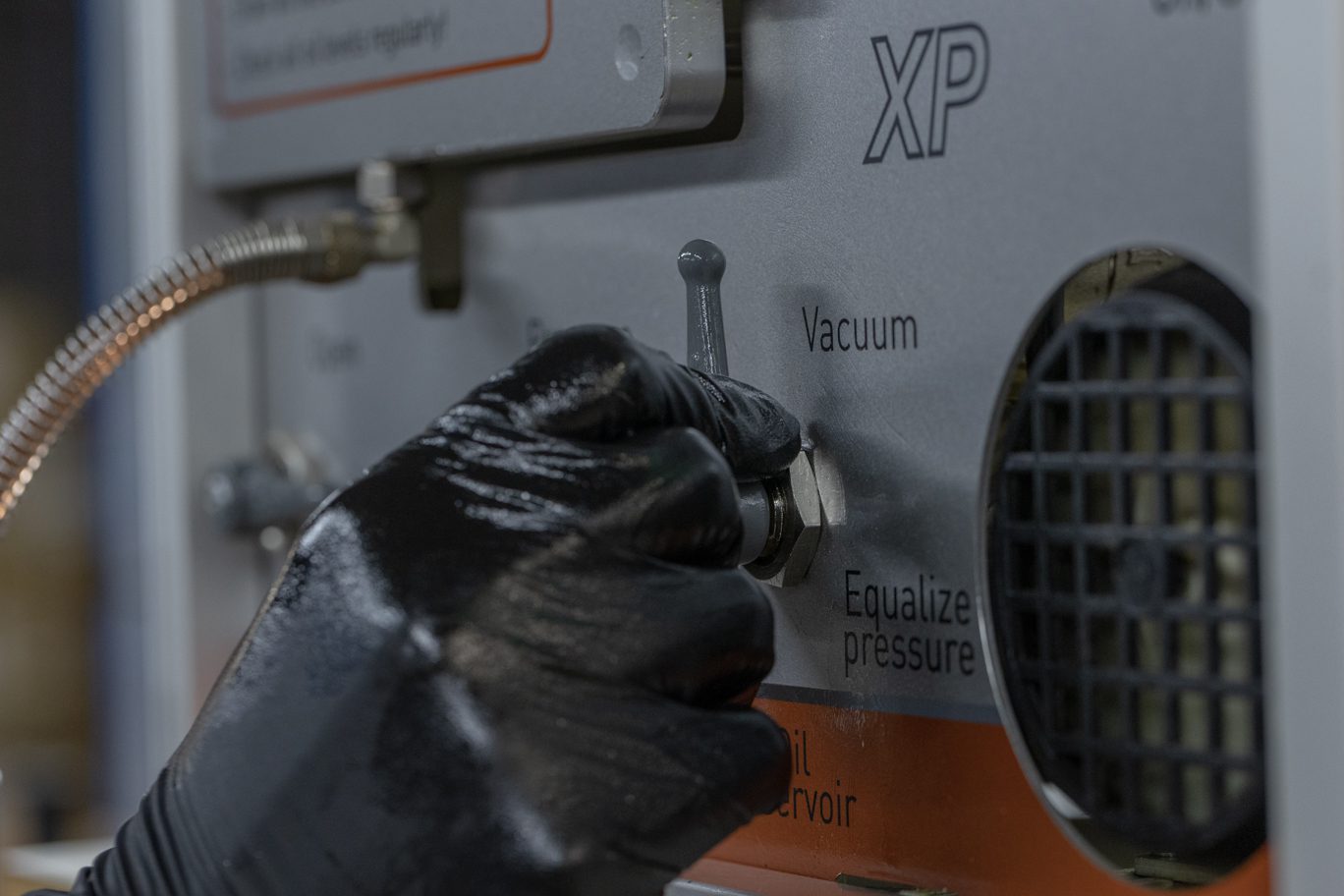
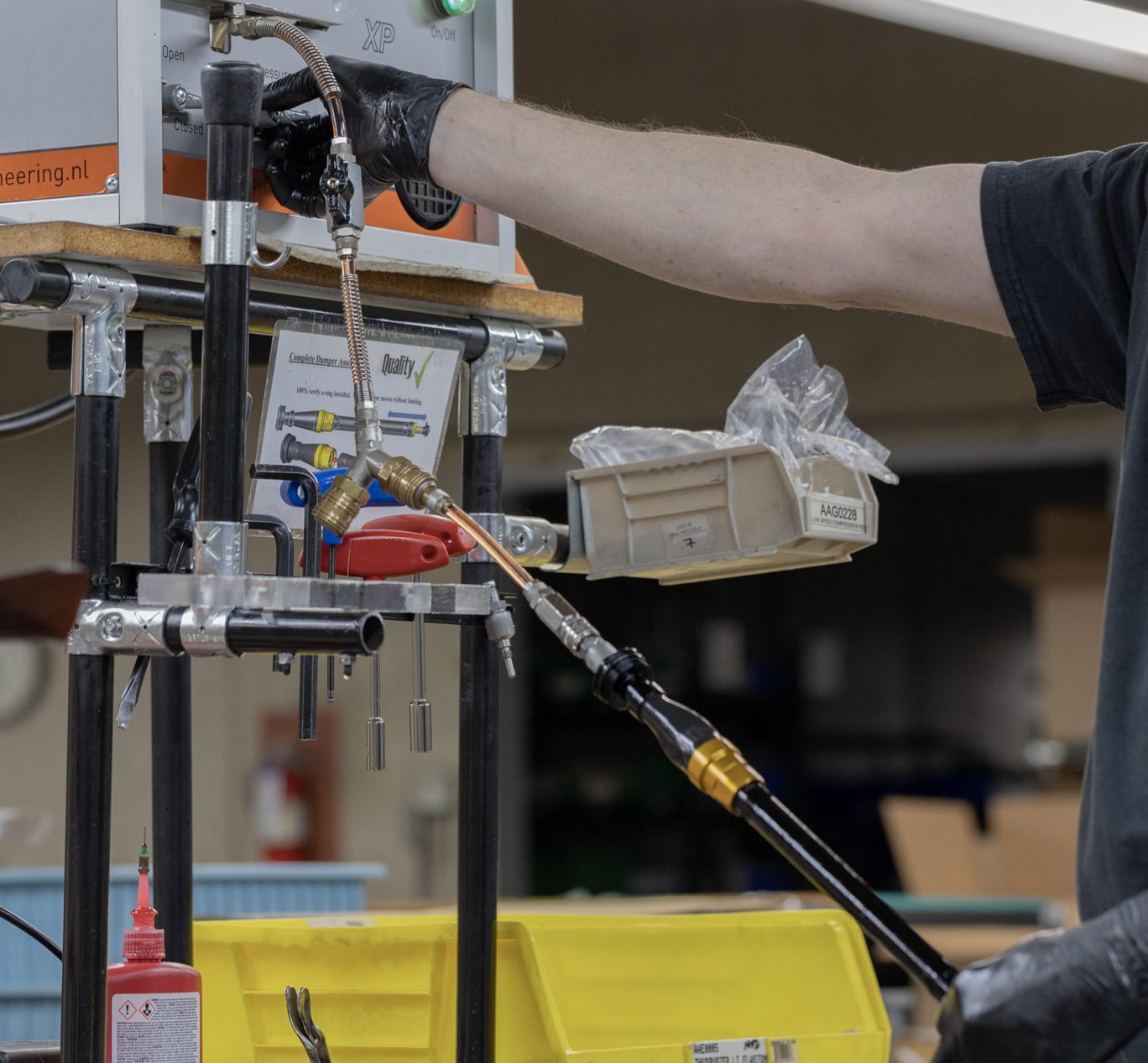
Step 2 – Vacuum and Oil Fill Process
Fill vacuum to (3) mbar. Equalize pressure. Pressurize damper to (2) bars while extending damper shaft.
***Do not overfill. Can cause bladder to rupture.***
Fill vacuum to (3) mbar allowing damper shaft to return to compressed. Equalize pressure. Pressurize damper to (2) bars while extending damper shaft.
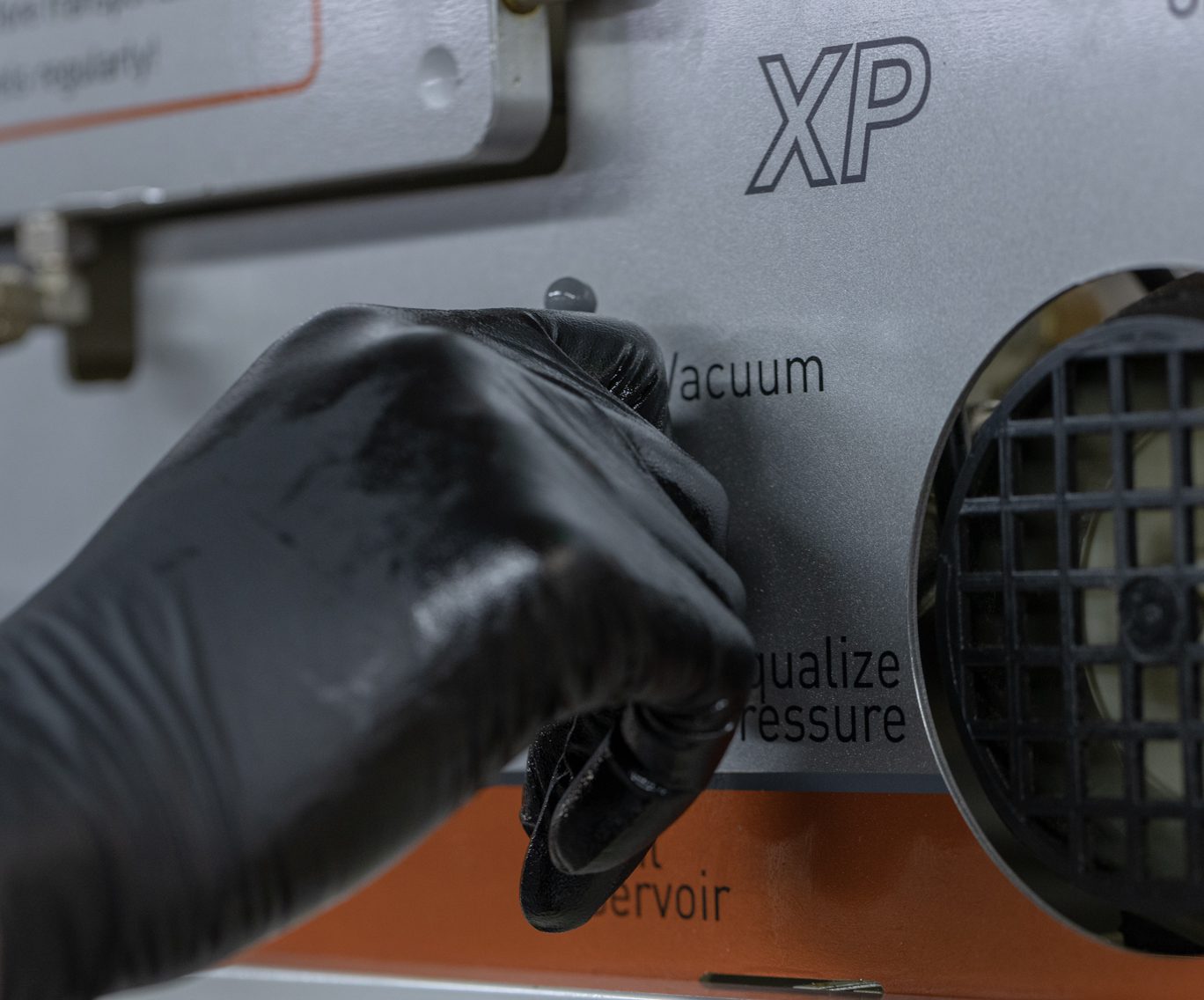
Switching to Equalize
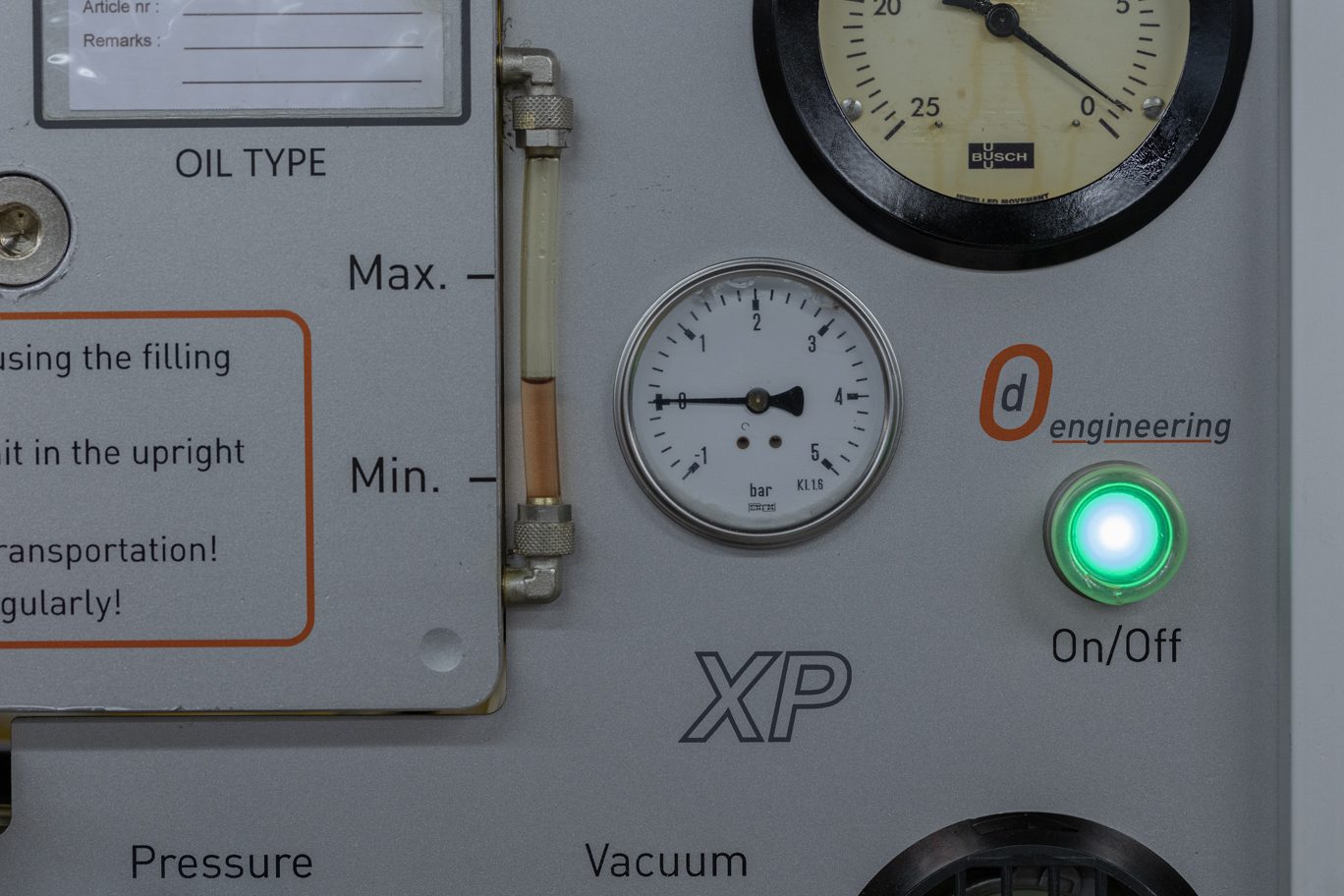
Equalizing Pressure
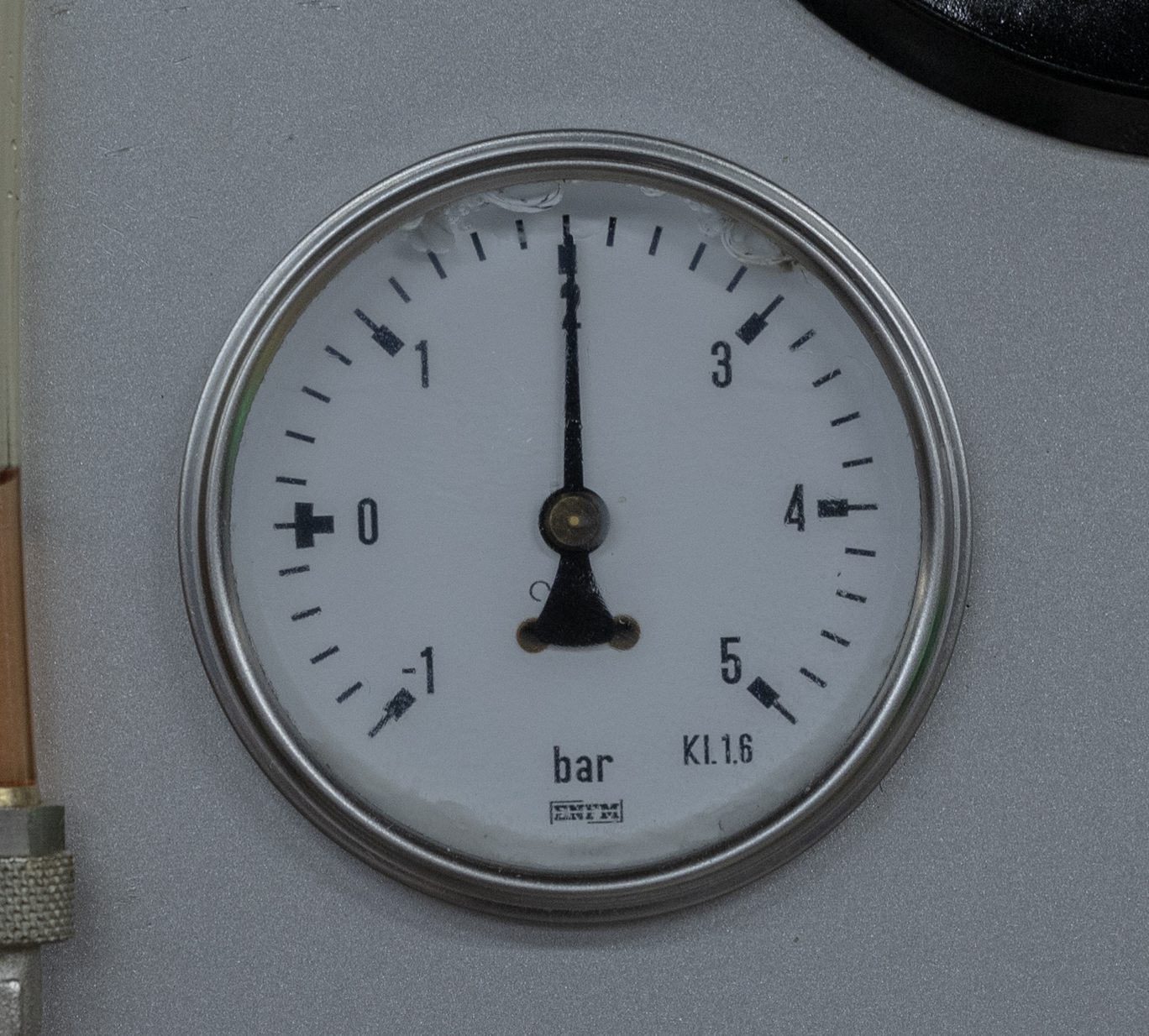
Pressurizing to 2 bars
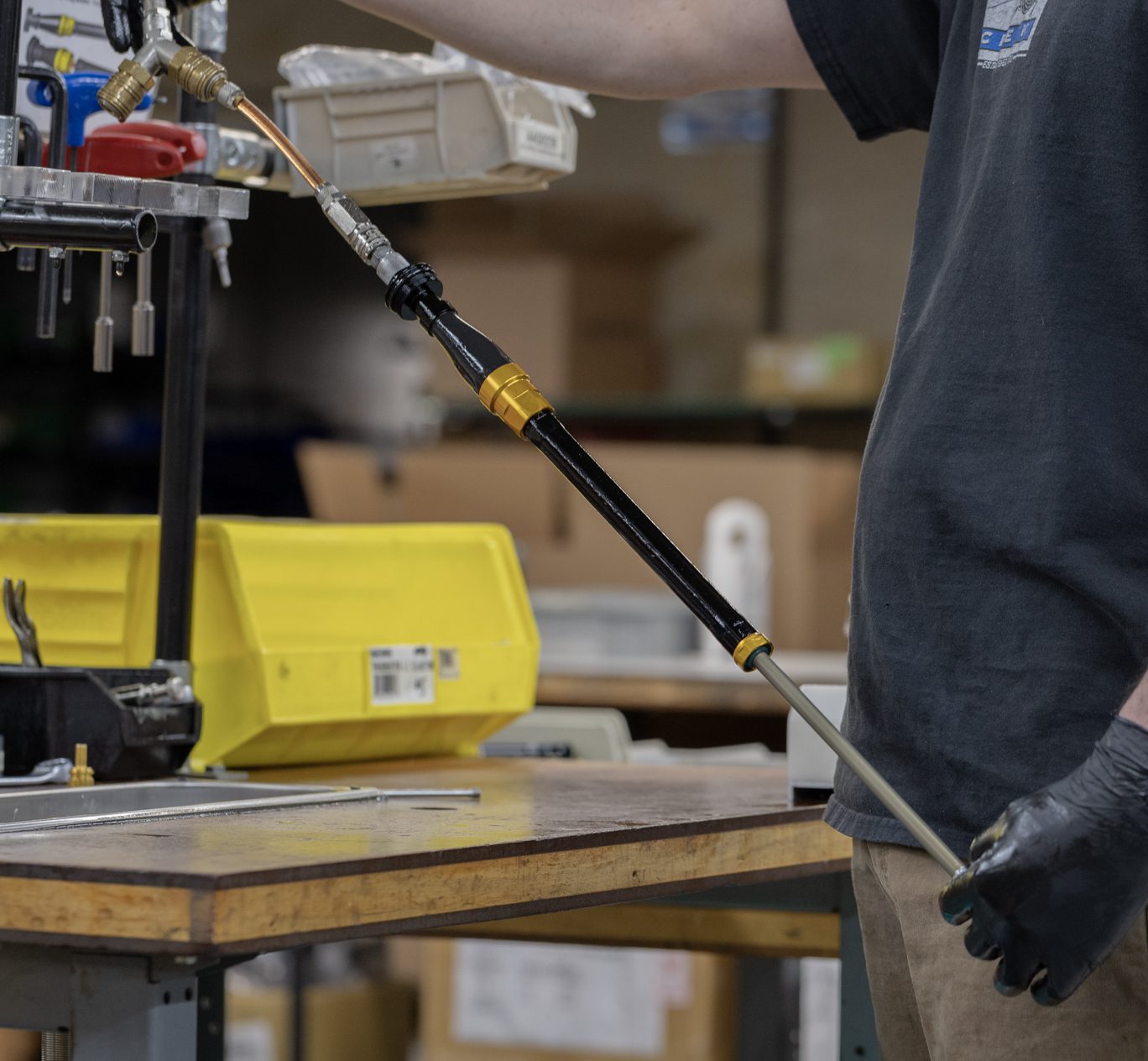
Extending Damper Shaft
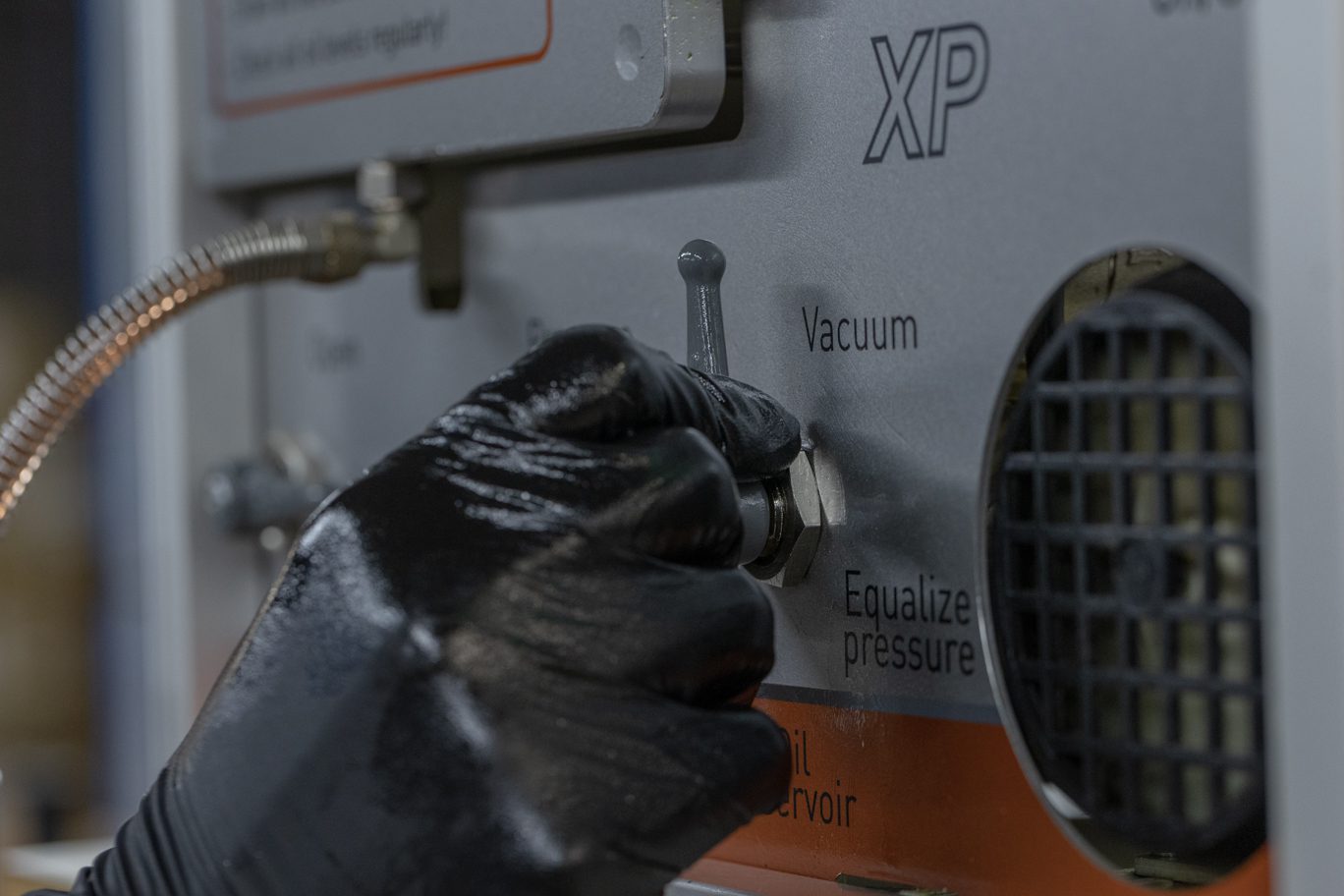
Vacuuming Damper
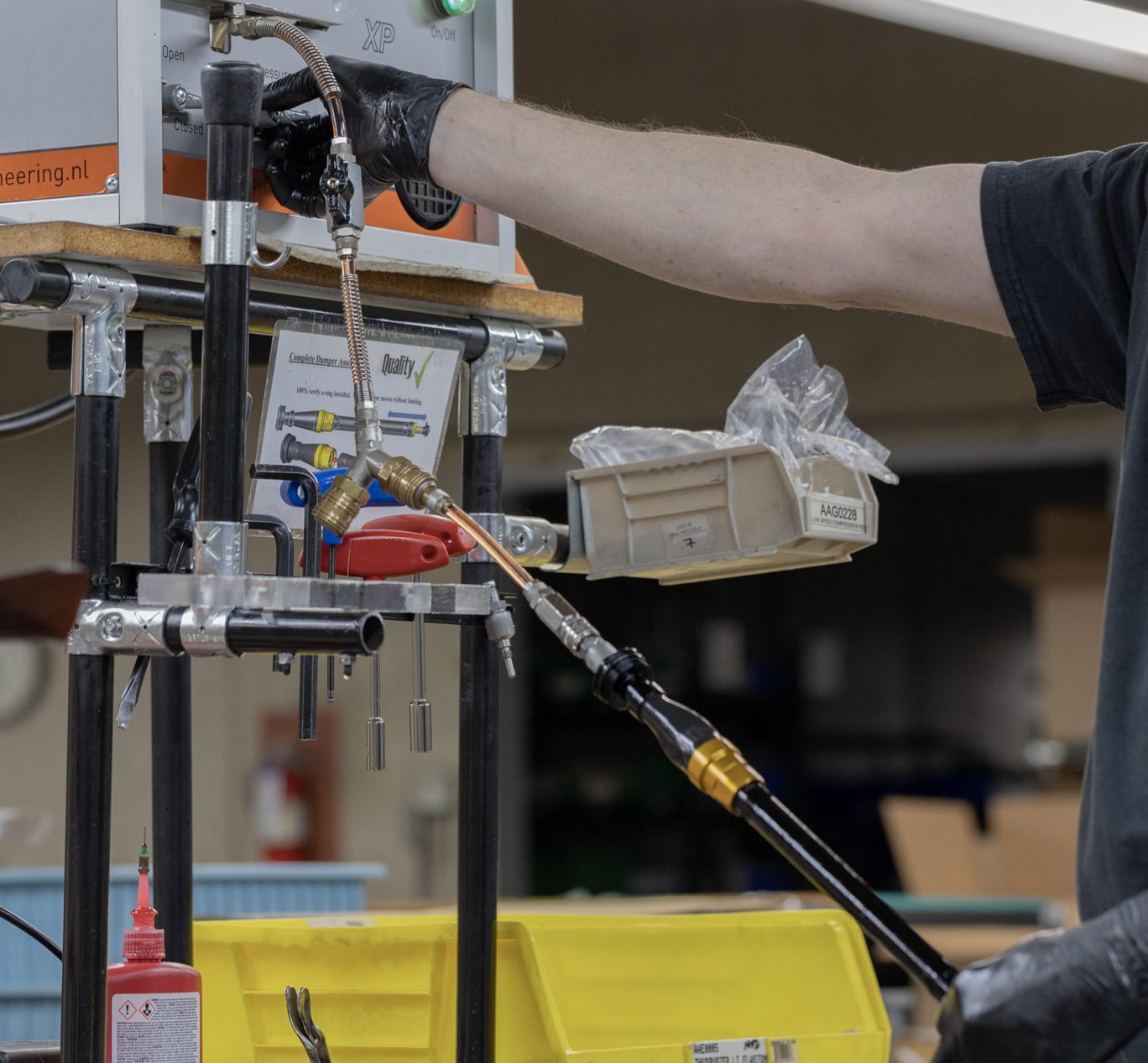
Allowing Damper Shaft to Compress
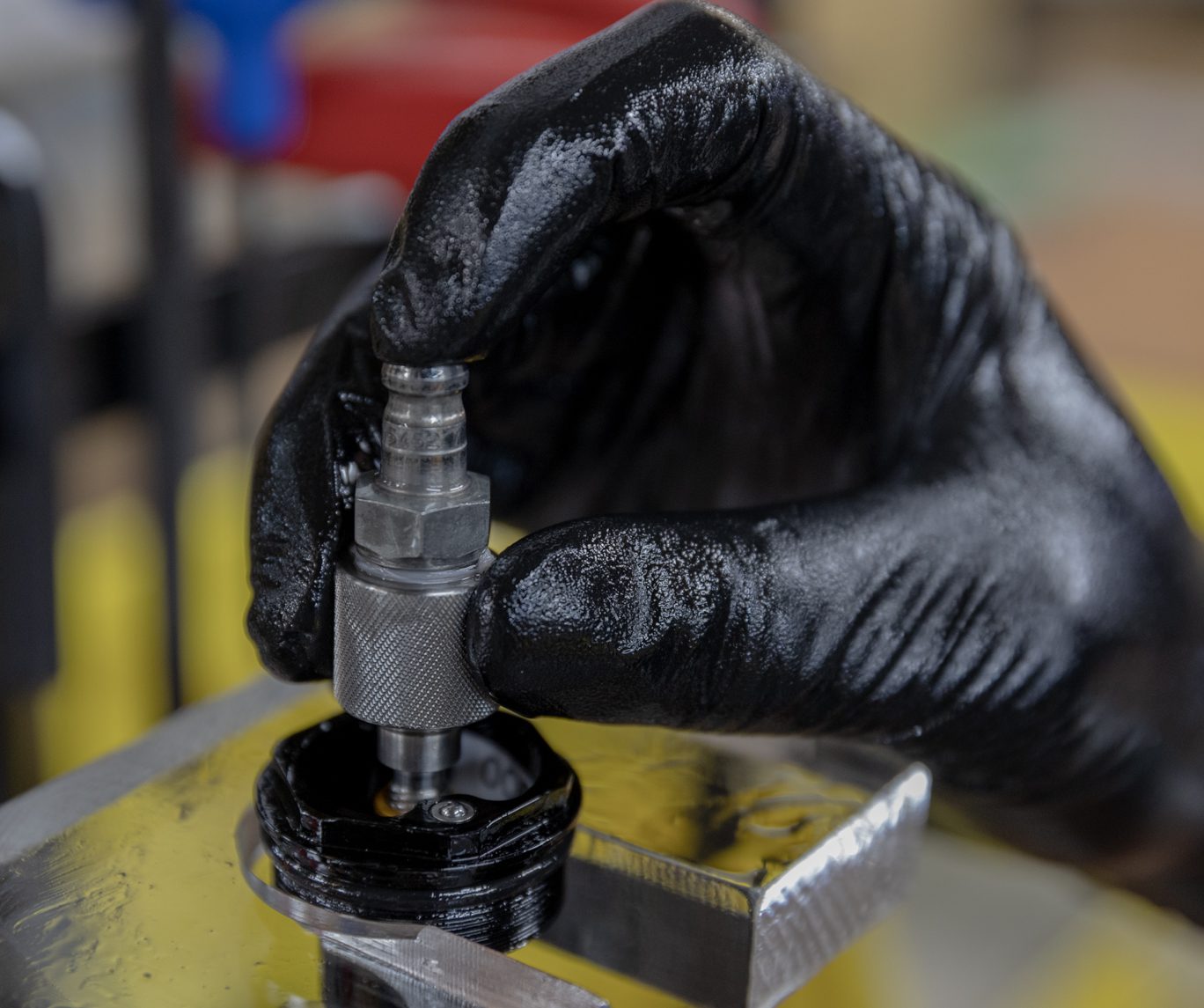
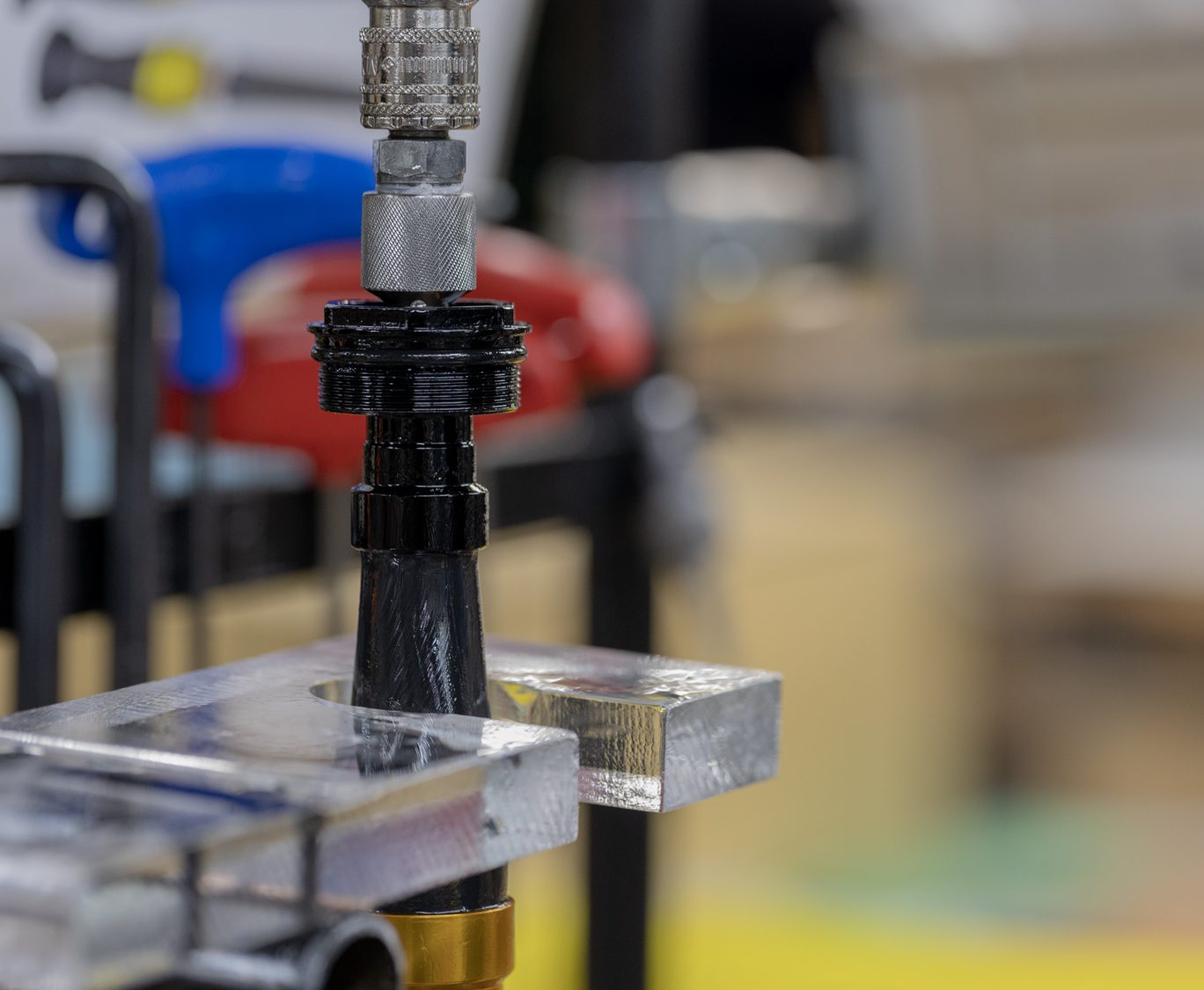
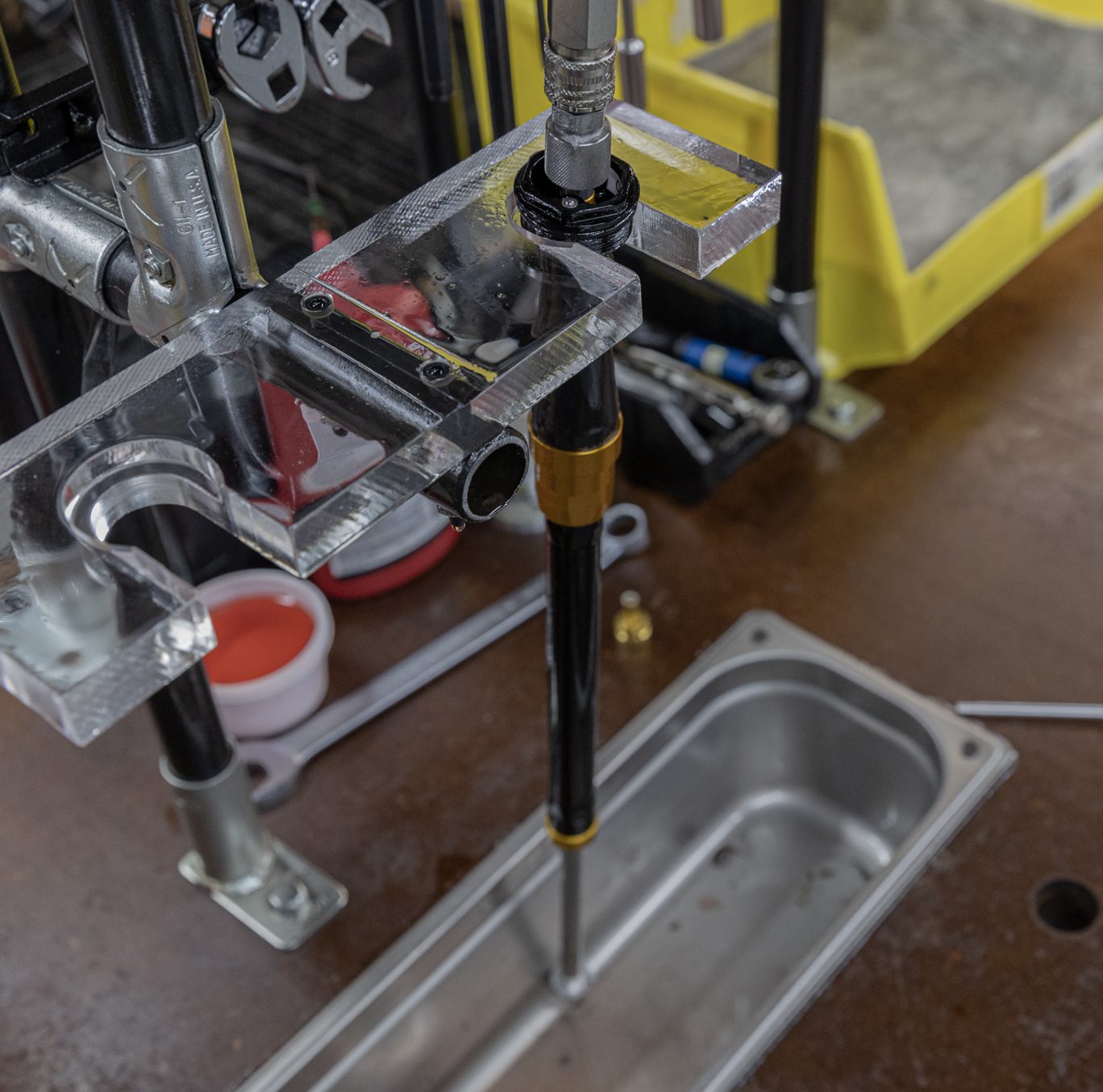
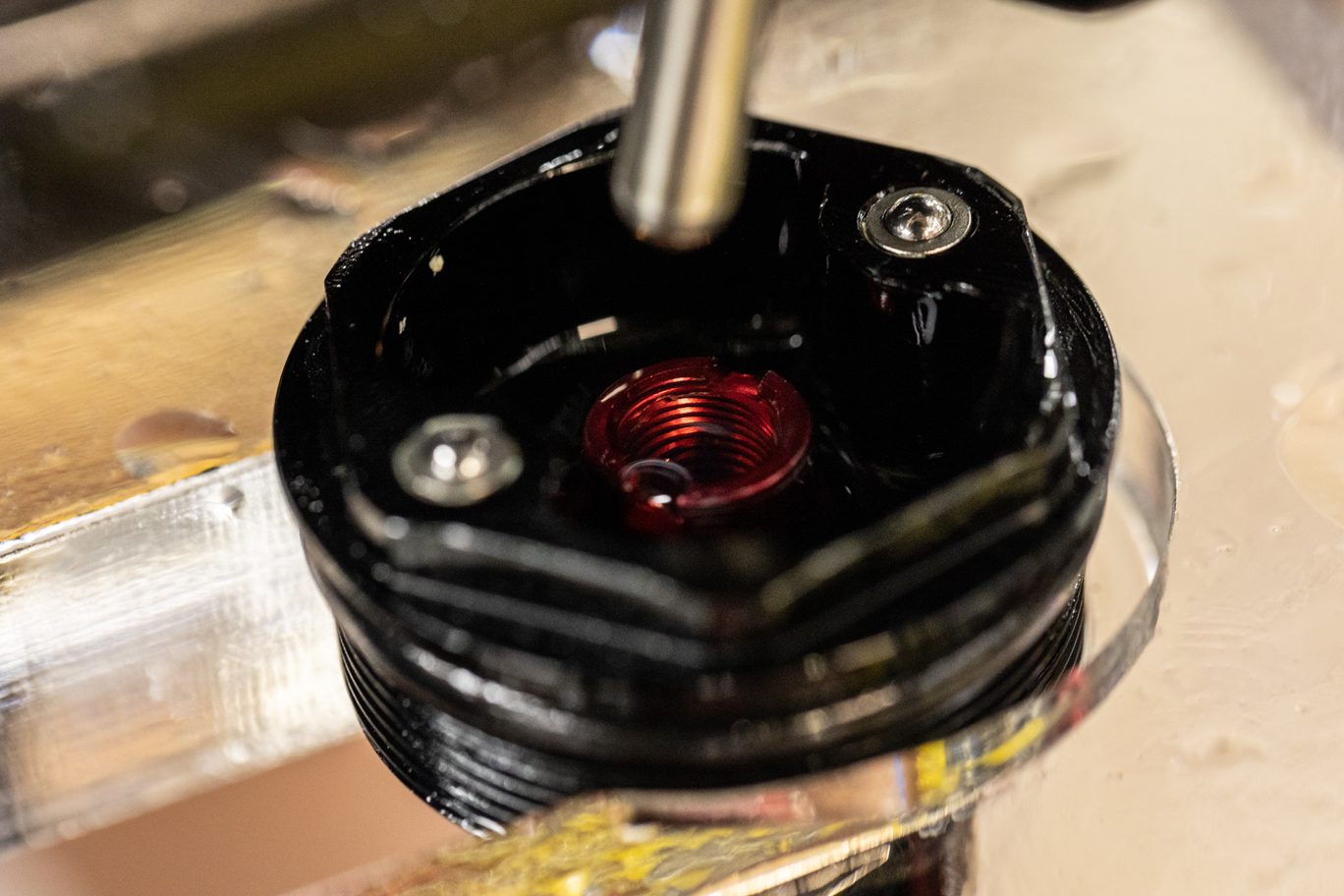
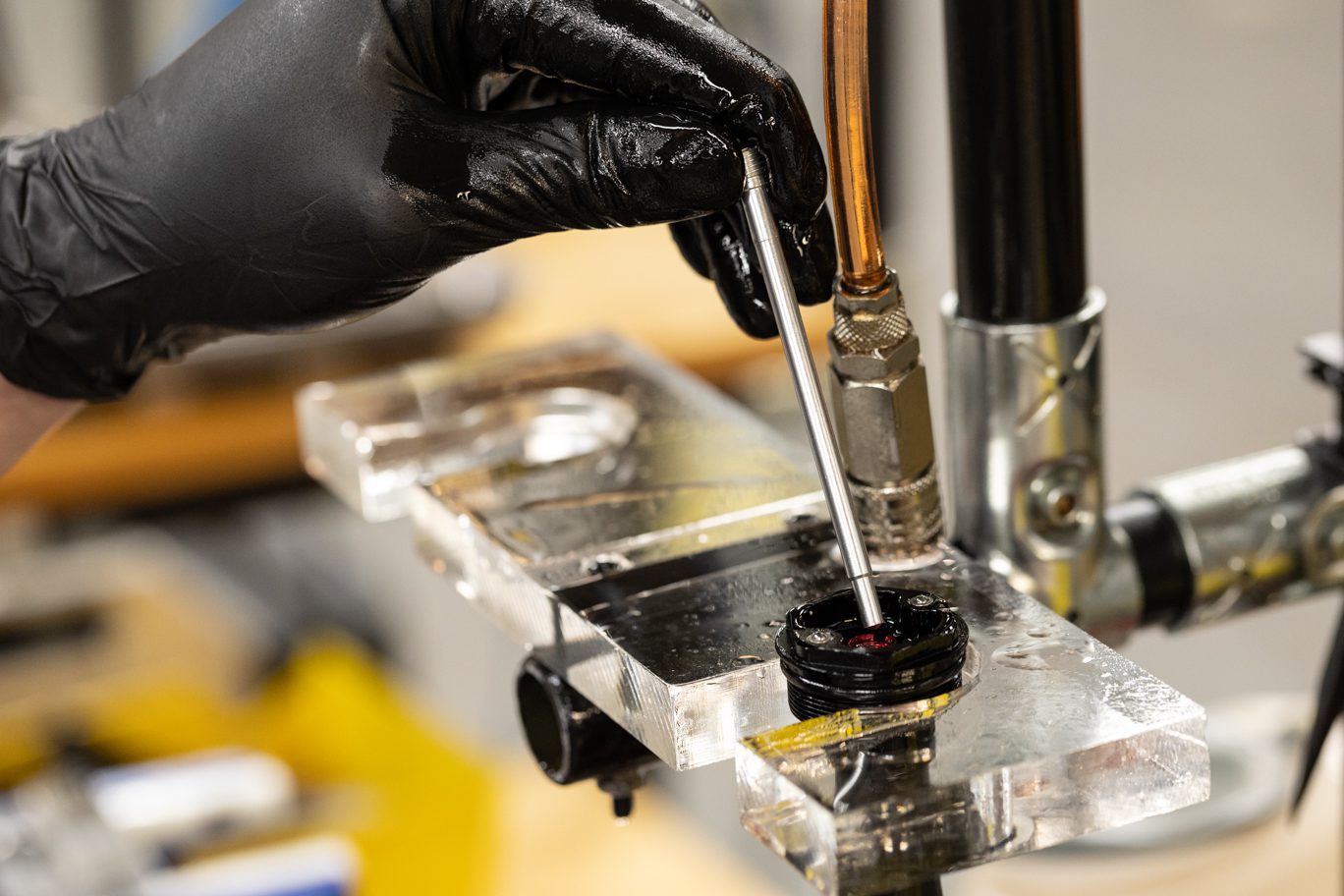
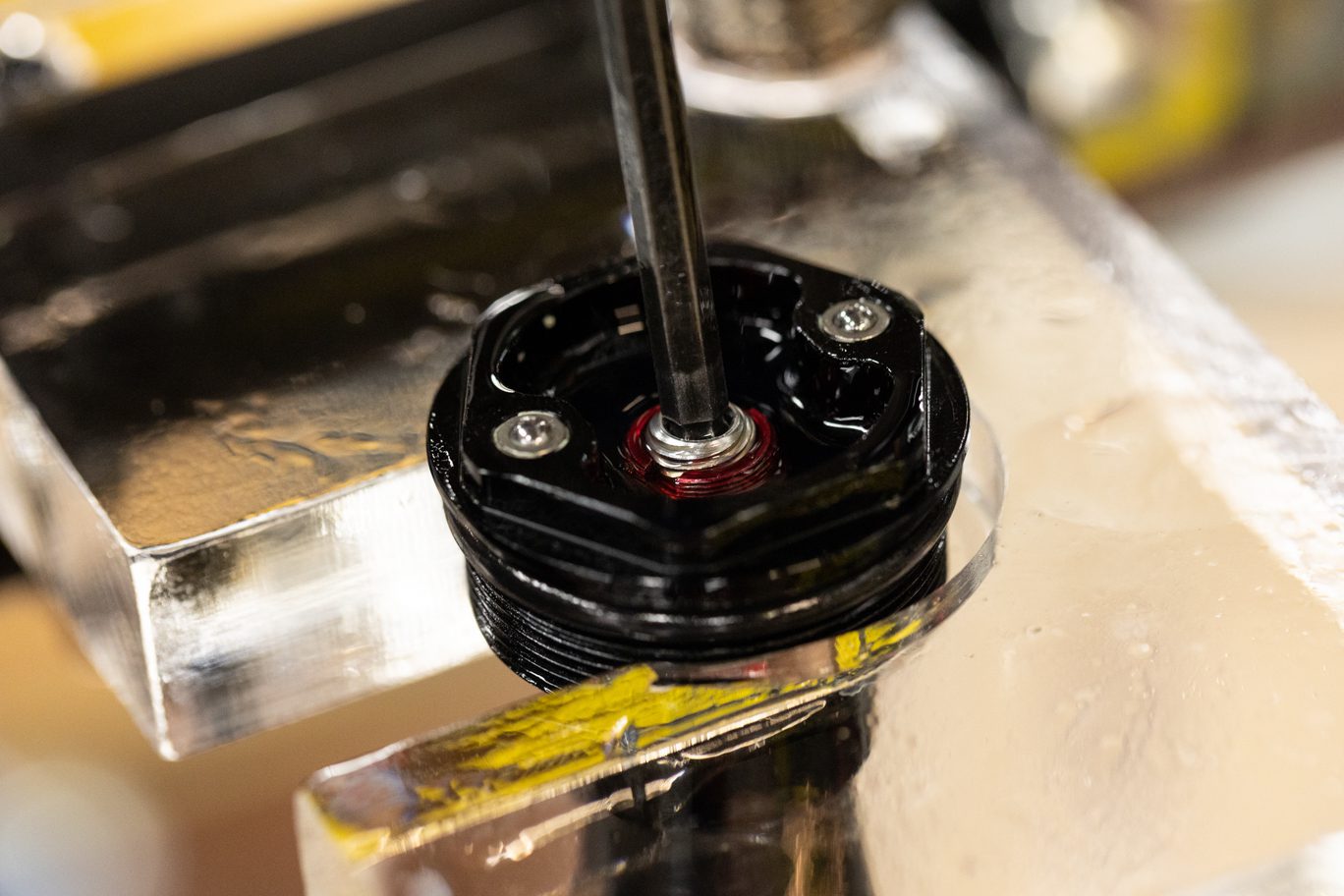
Step 3 – Damper Closure
Disconnect damper from fill machine with fill tool attached. Hold finger over fill adapter to keep oil from leaking. Slowly compress shaft 5cm allowing oil overflow. Insert low speed needle. Thread needle into until flush with helix using 4mm Allen.
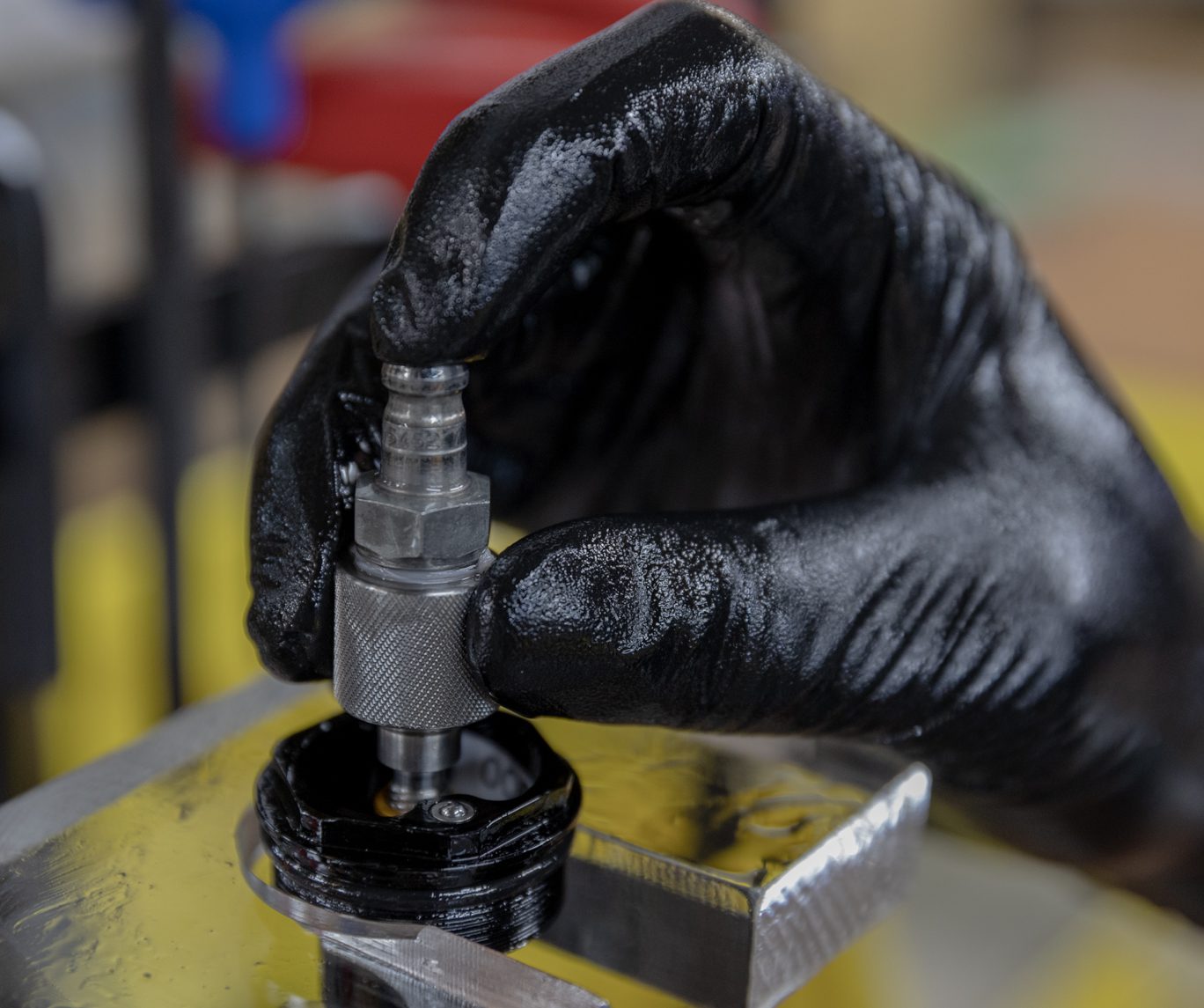
Disconnect from Fill Machine
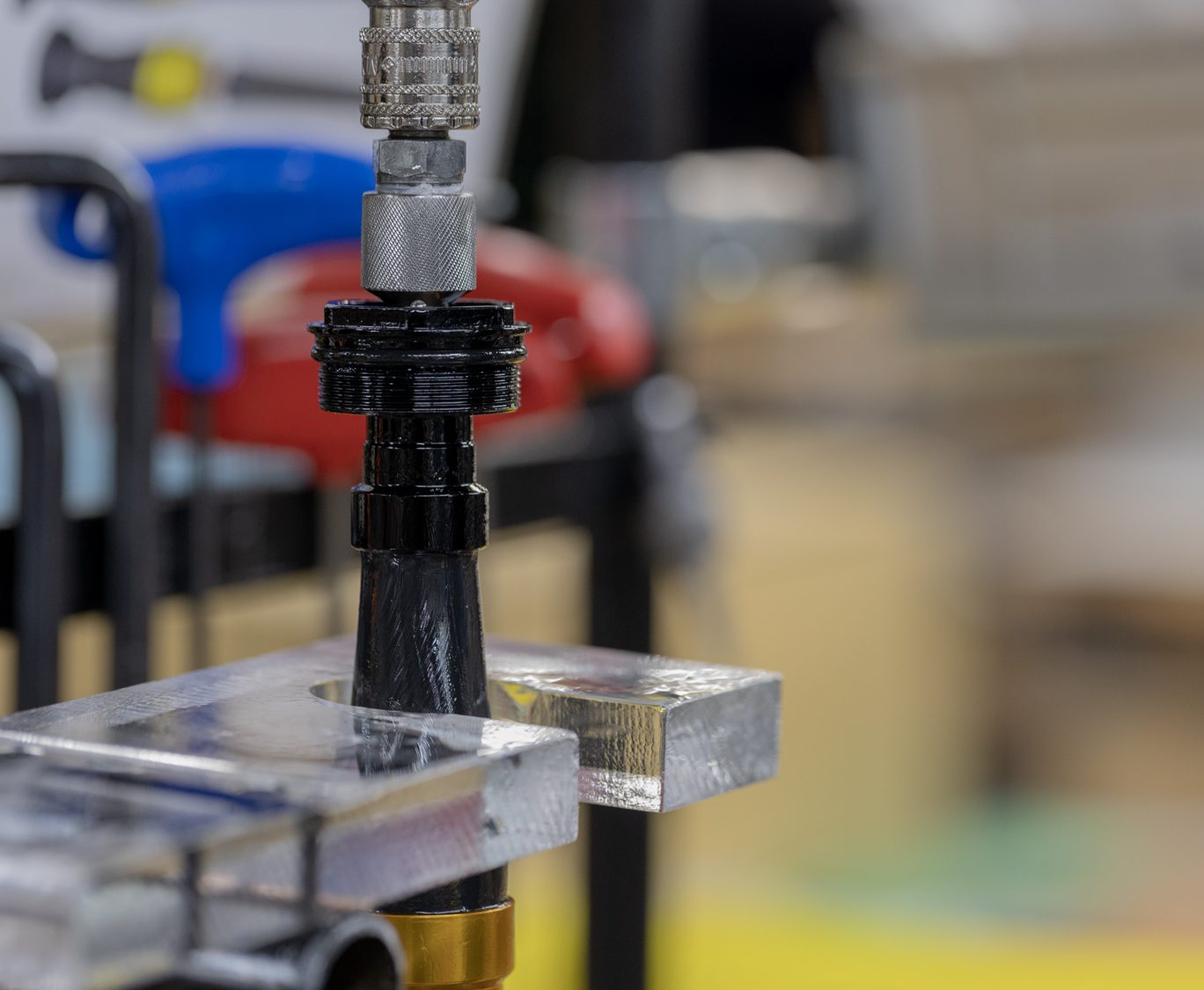
Damper Before Pre-Compression
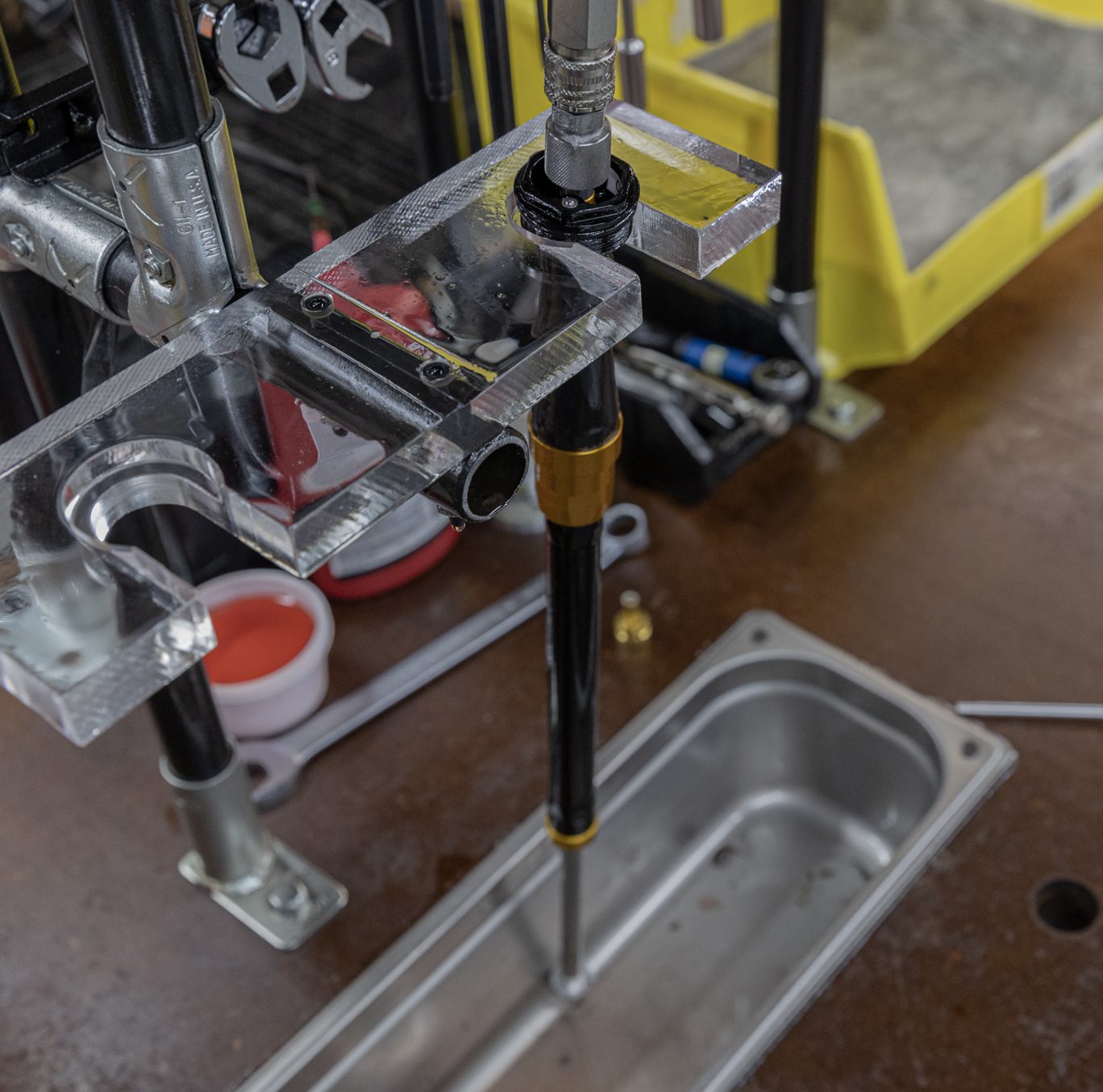
Damper Compressed 5cm
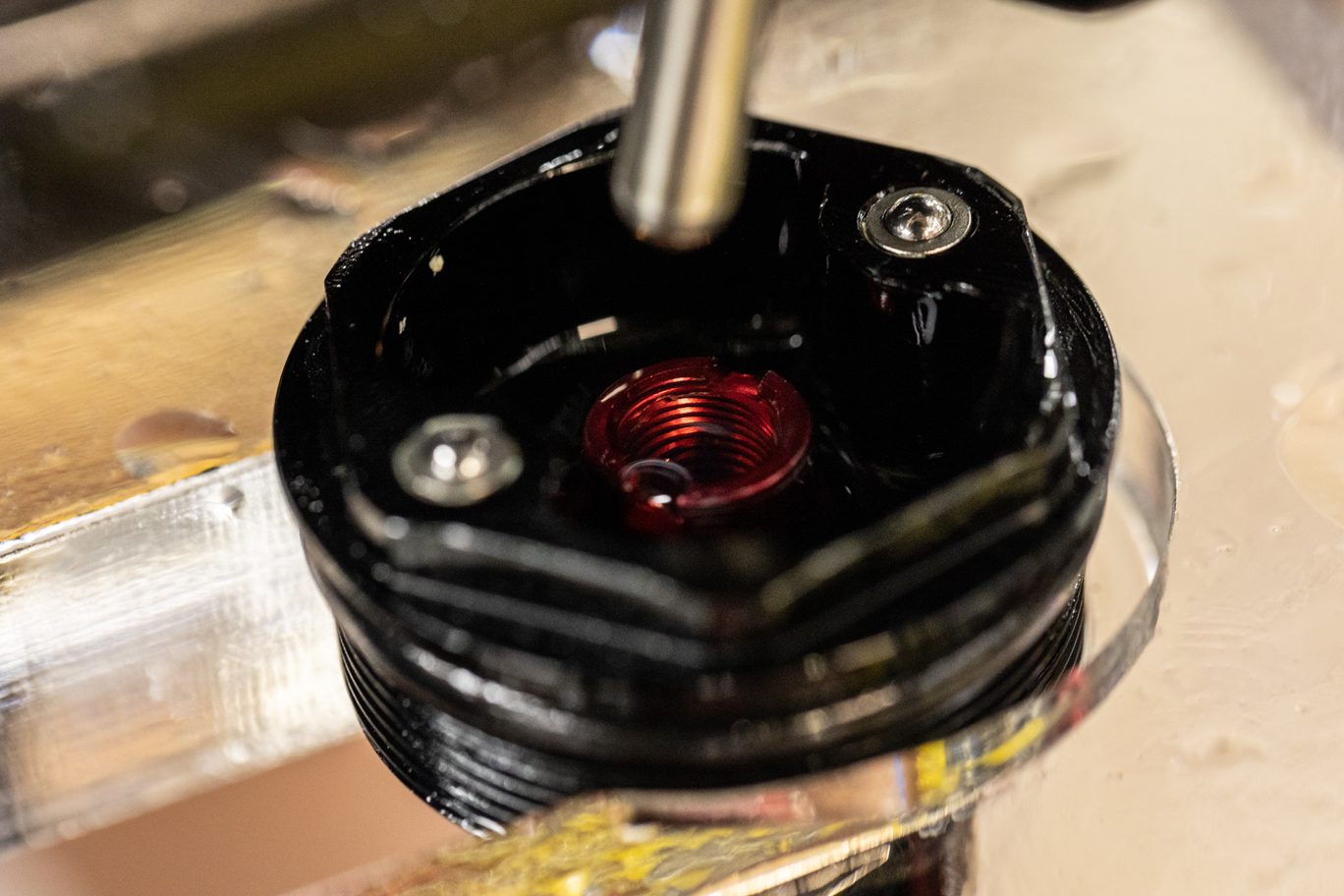
Fill Tool Removed
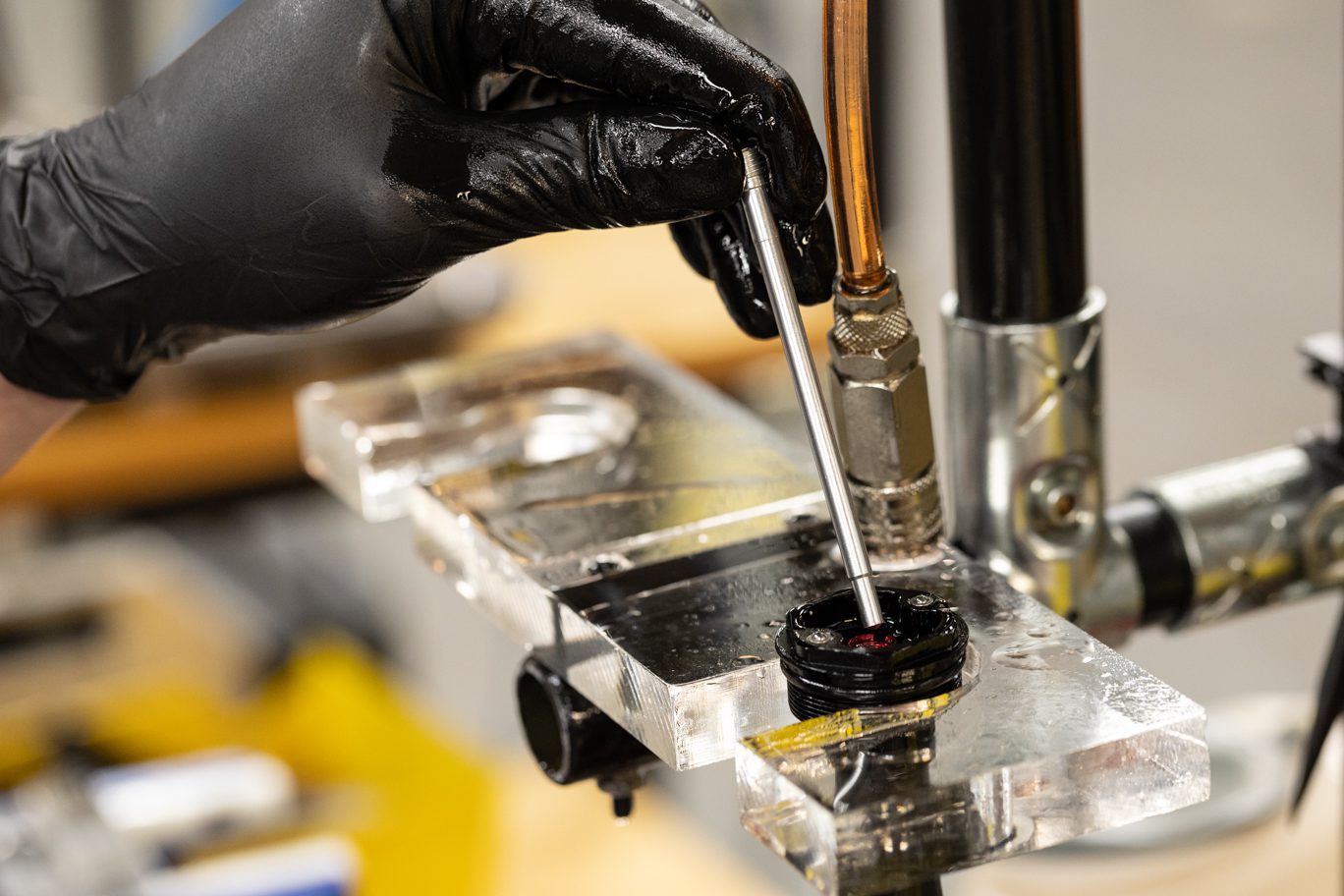
Low Speed Needle Install
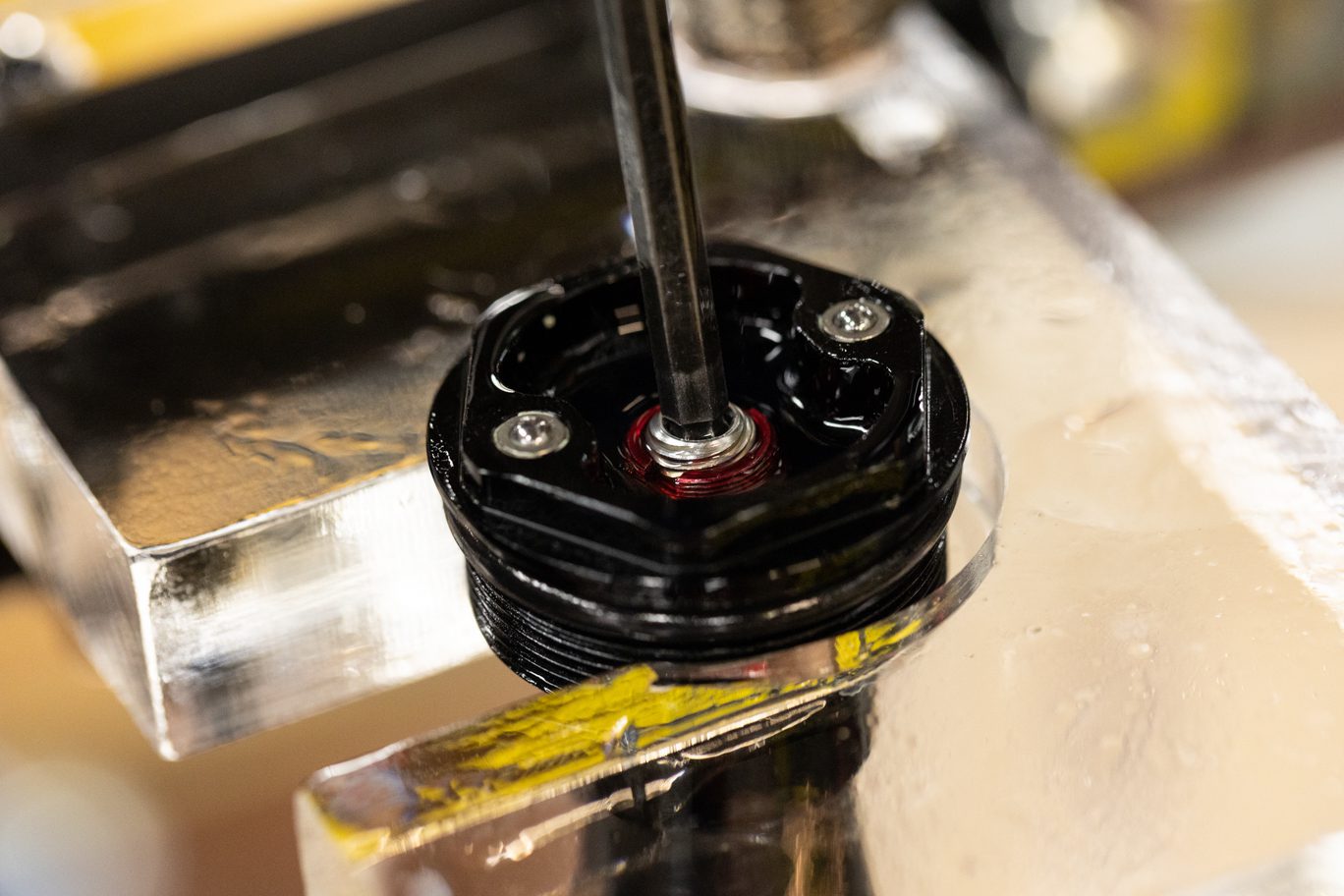
Low Speed Needle Closure Until Flush
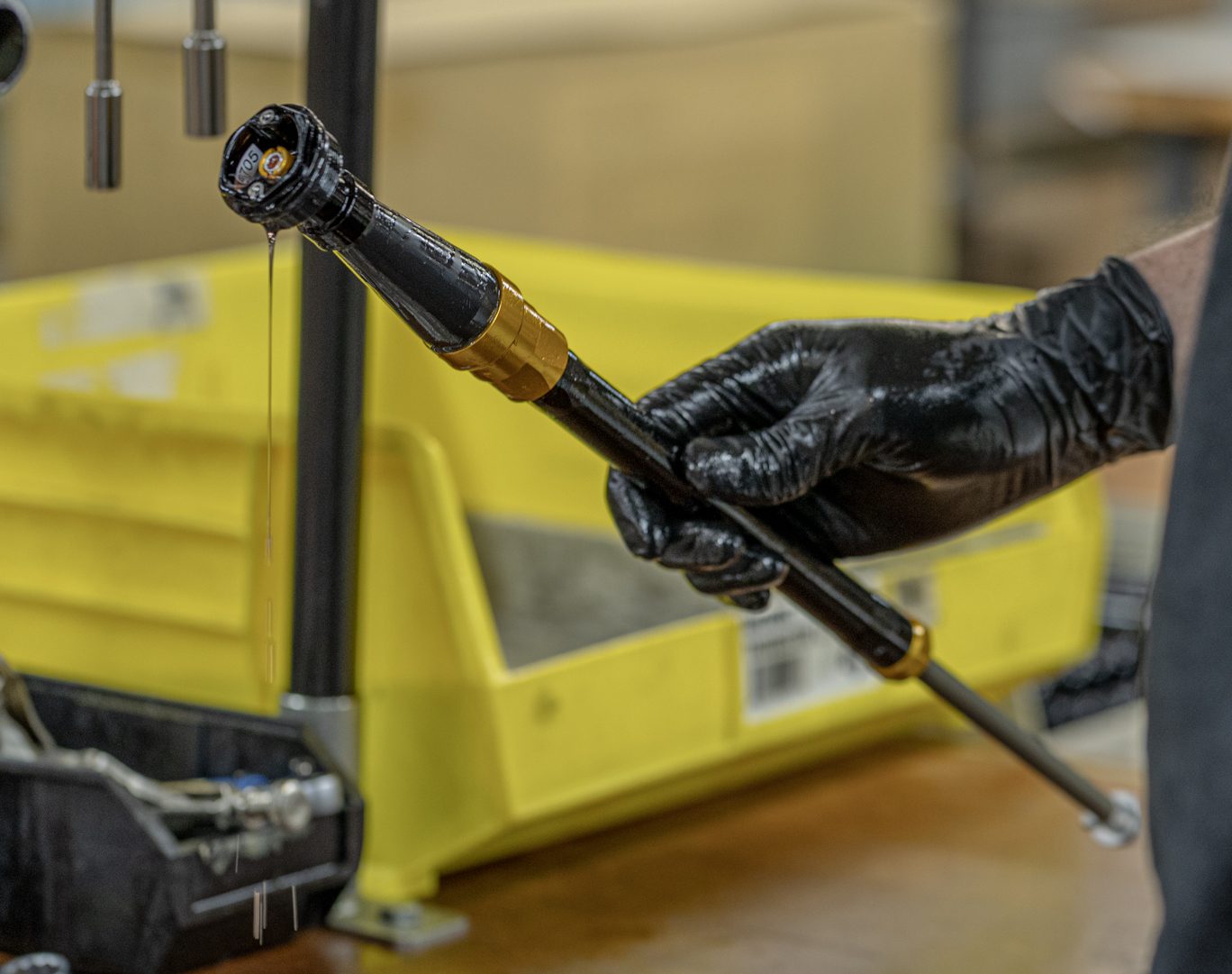
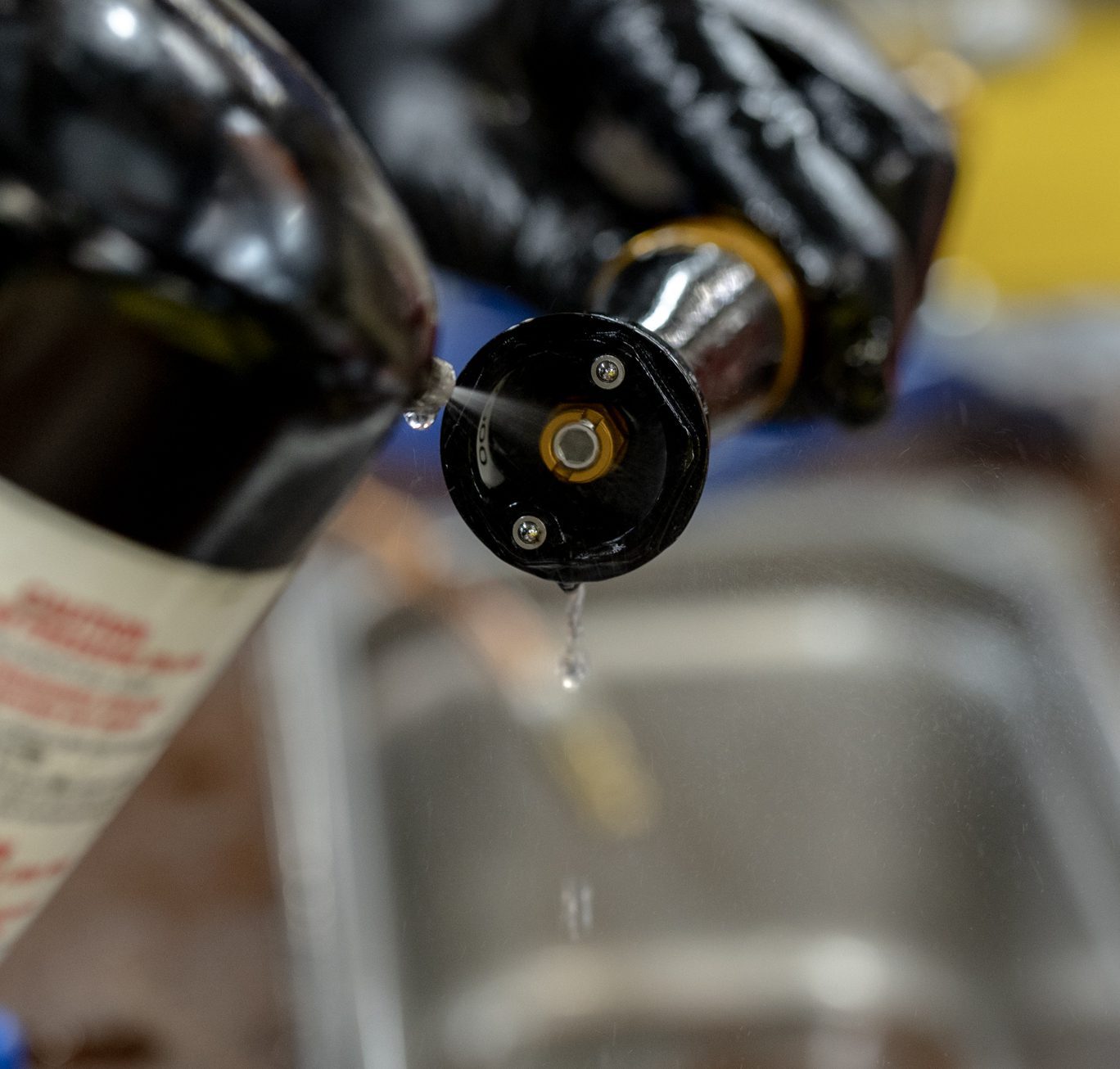
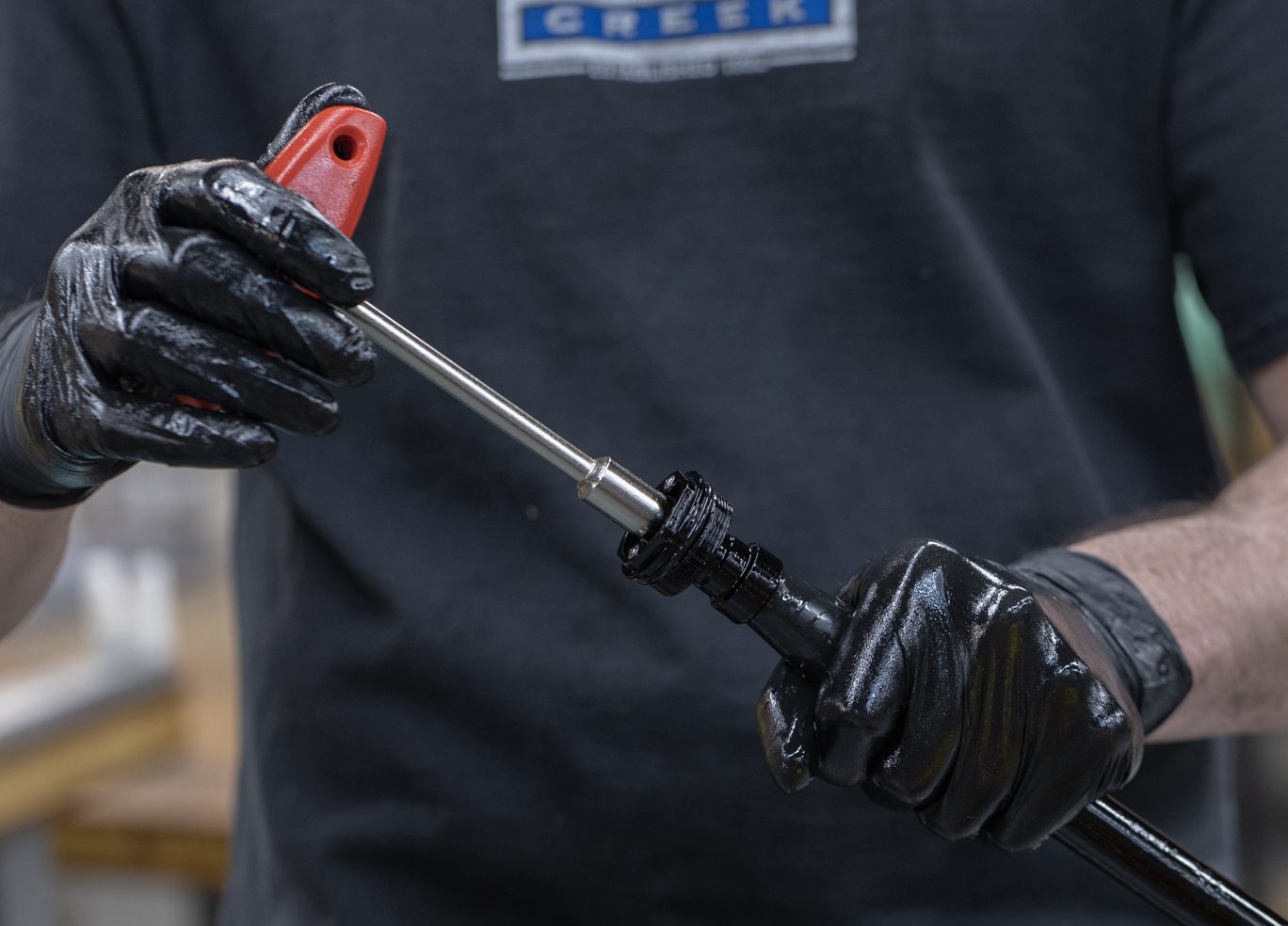
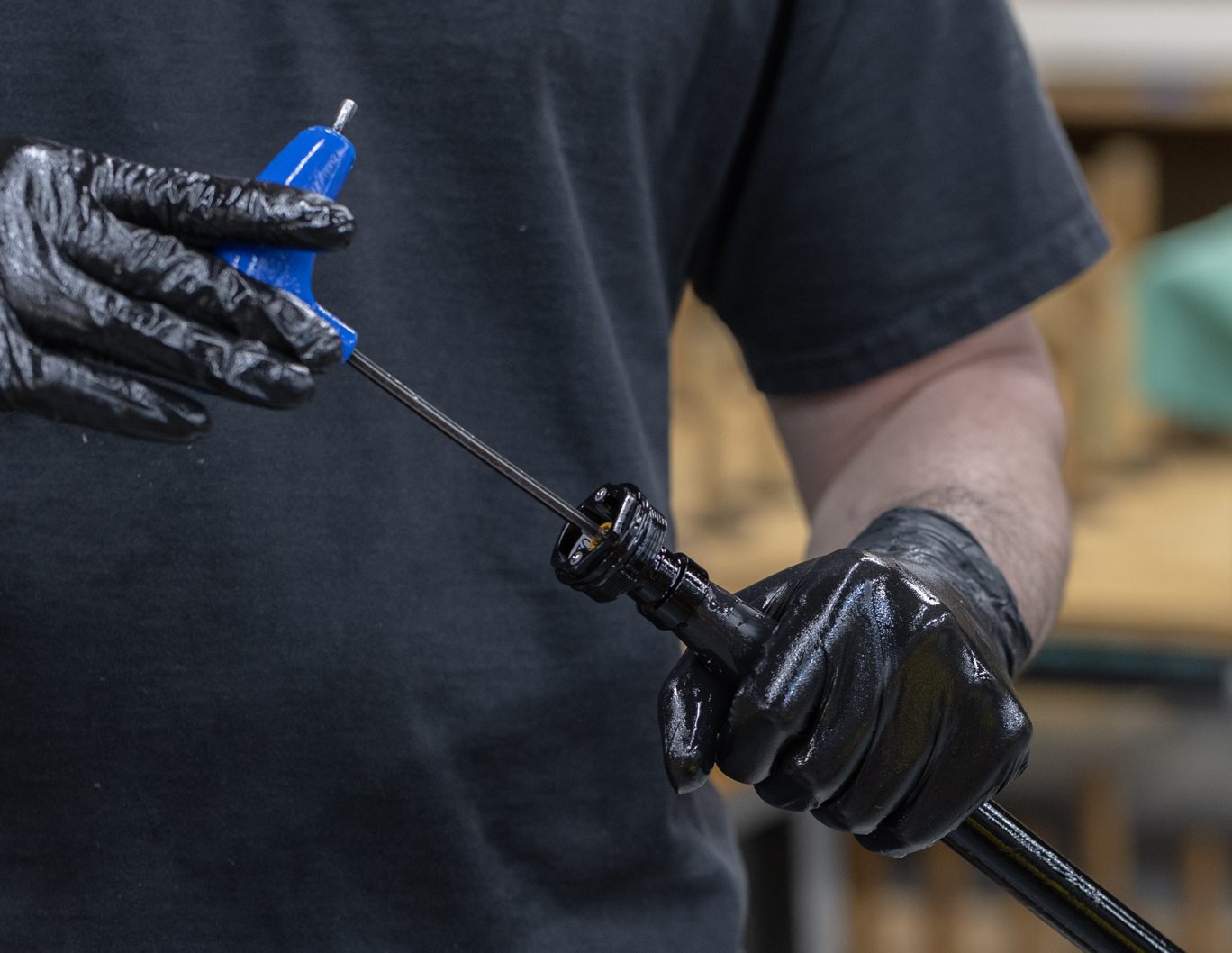
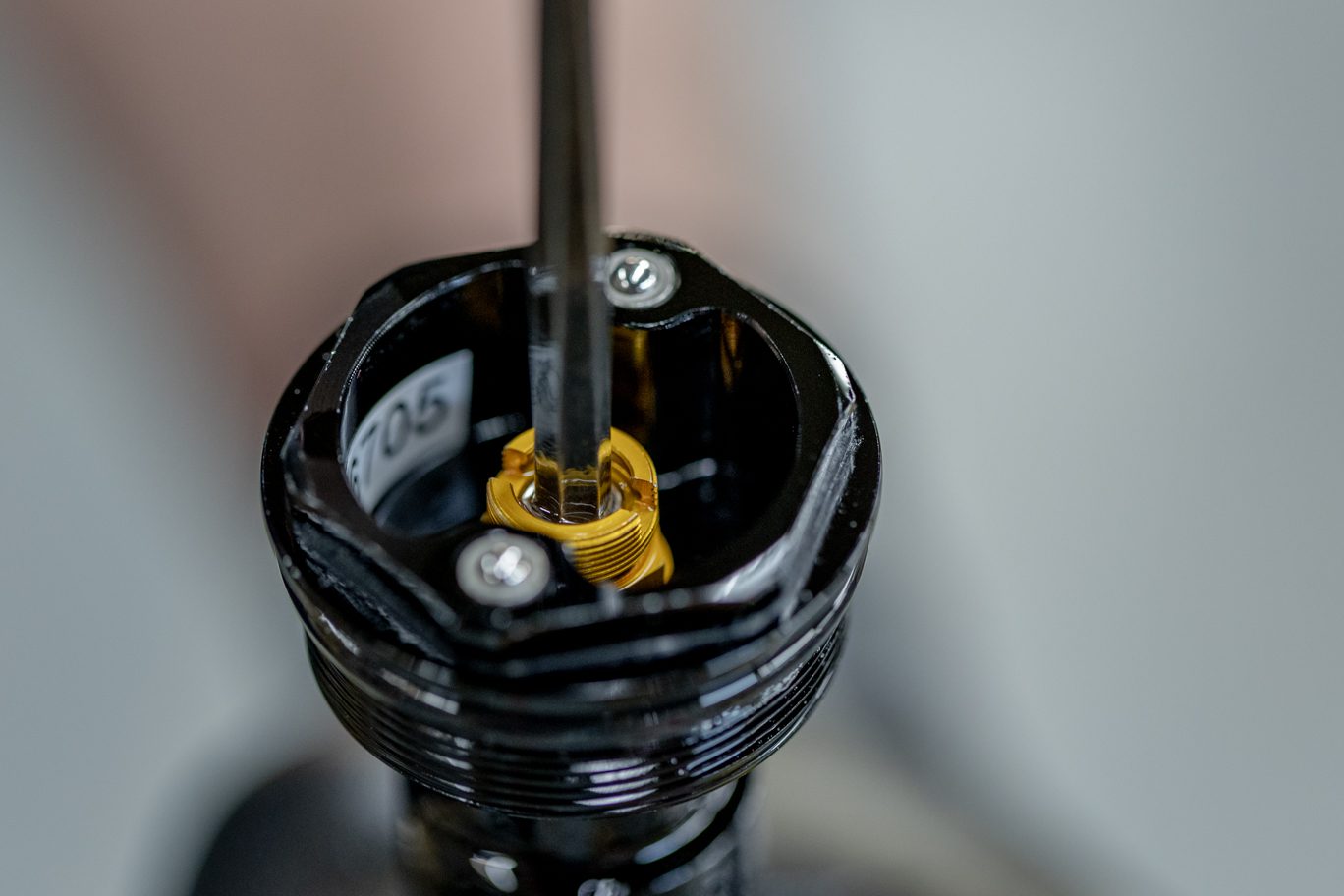
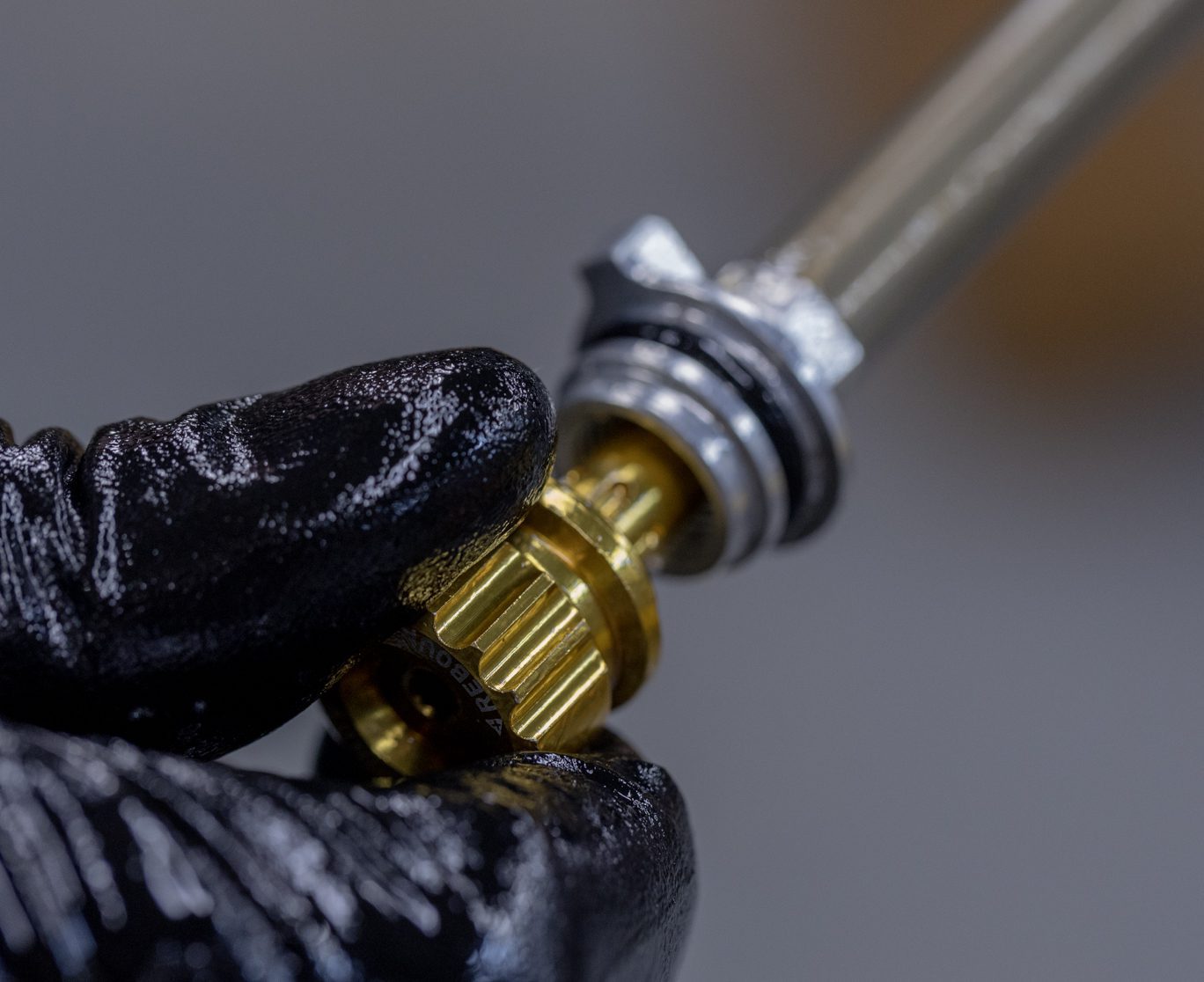
Step 4 – Damper Test
Clear top cap of any excess oil. Close (clockwise) high speed with 10mm socket. Close (clockwise)low speed with 4mm Allen. Close (clockwise) rebound. Cycle damper to check for proper function.
If mechanic dyno equipment is available, run damper on dyno at this point.
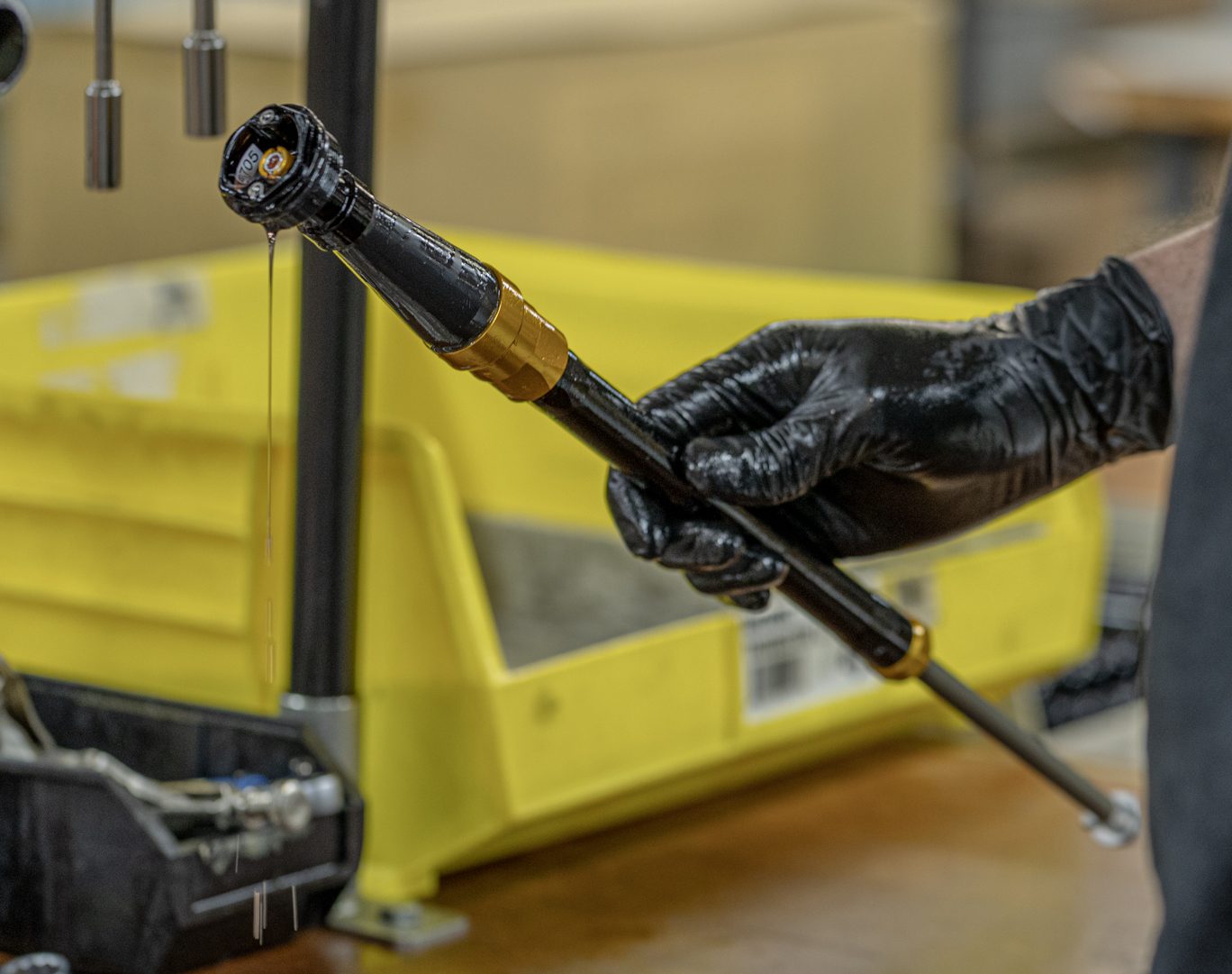
Dumping Excess Oil
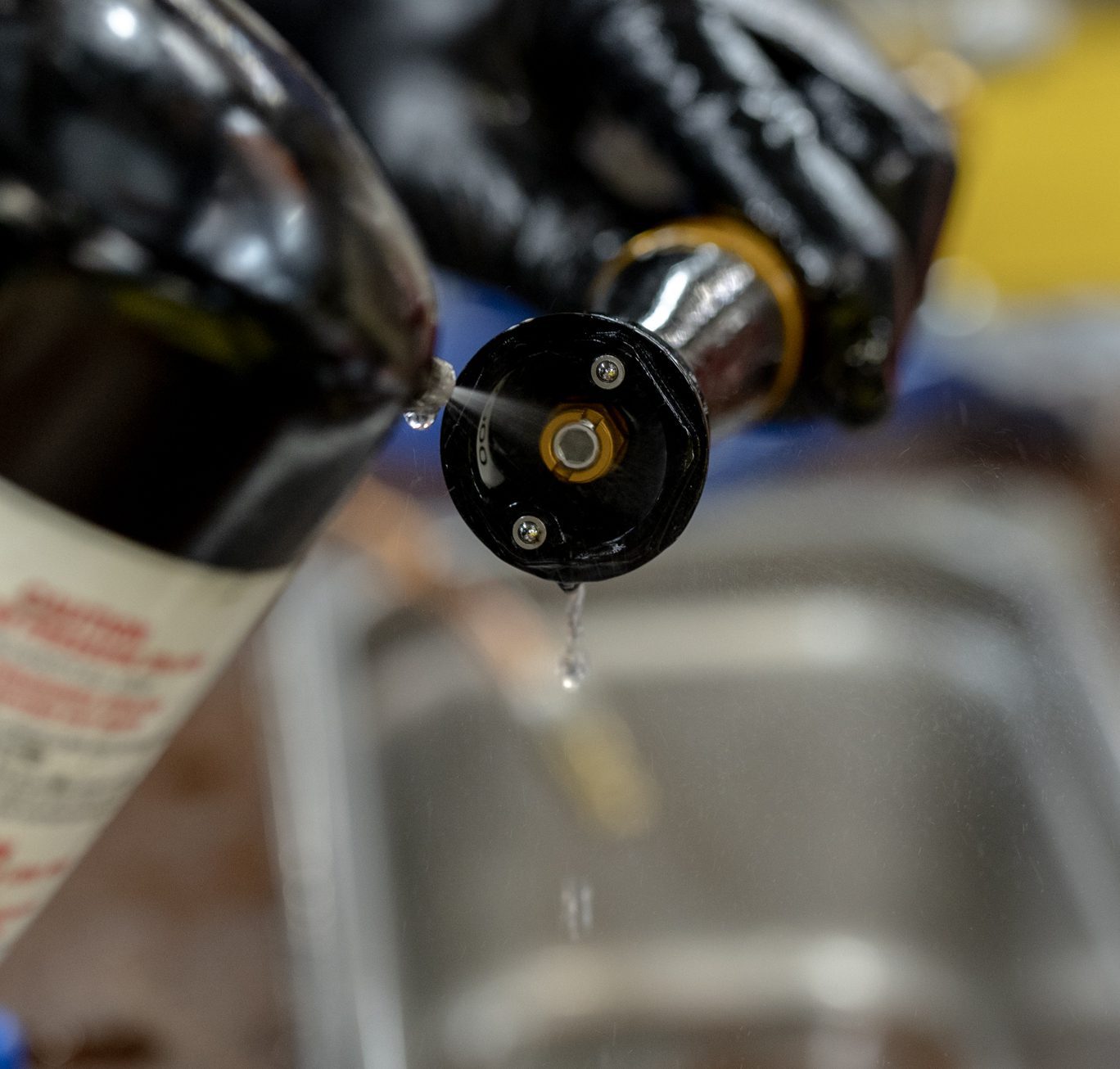
Cleaning Damper
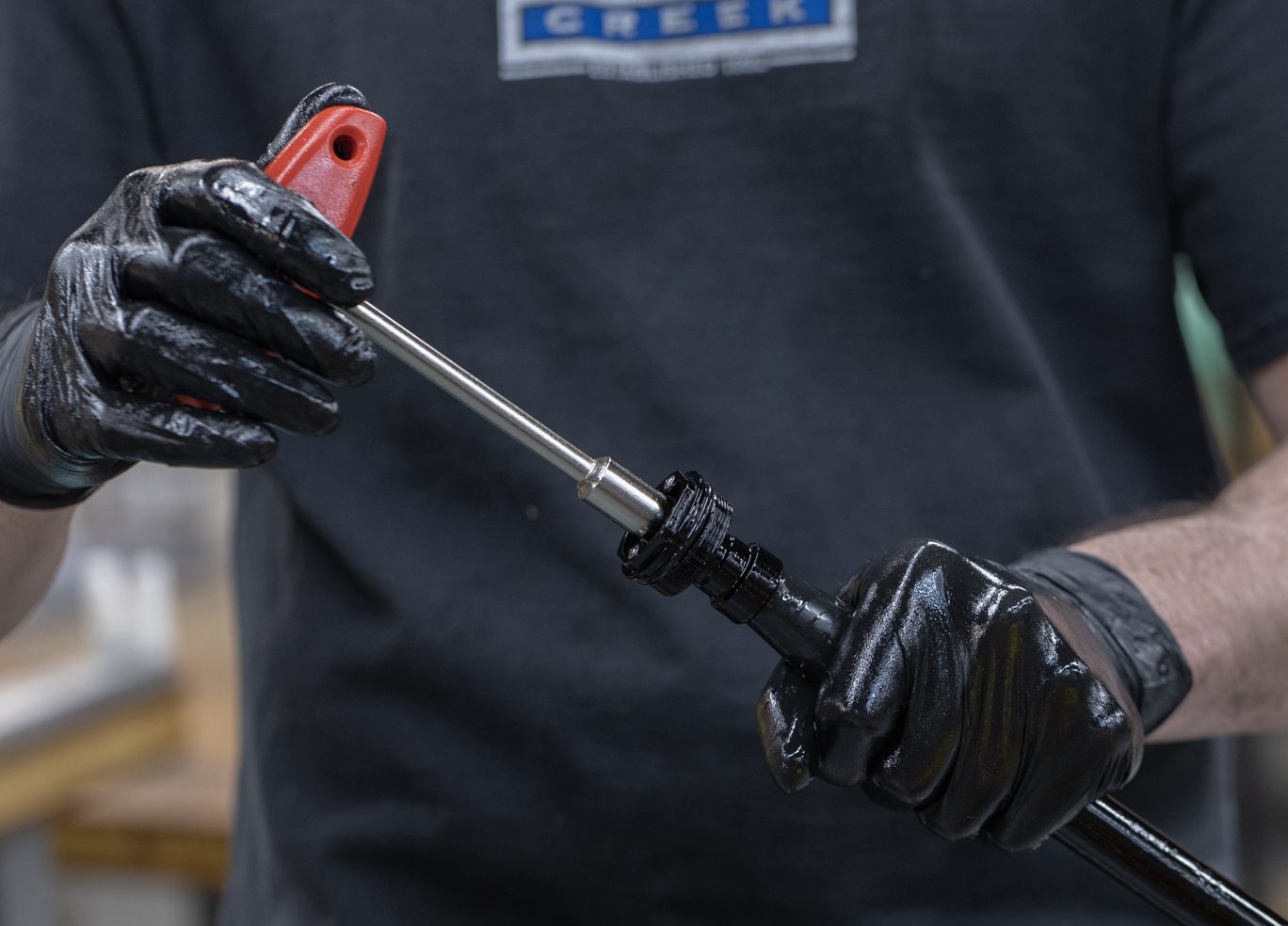
Closing High Speed Compression
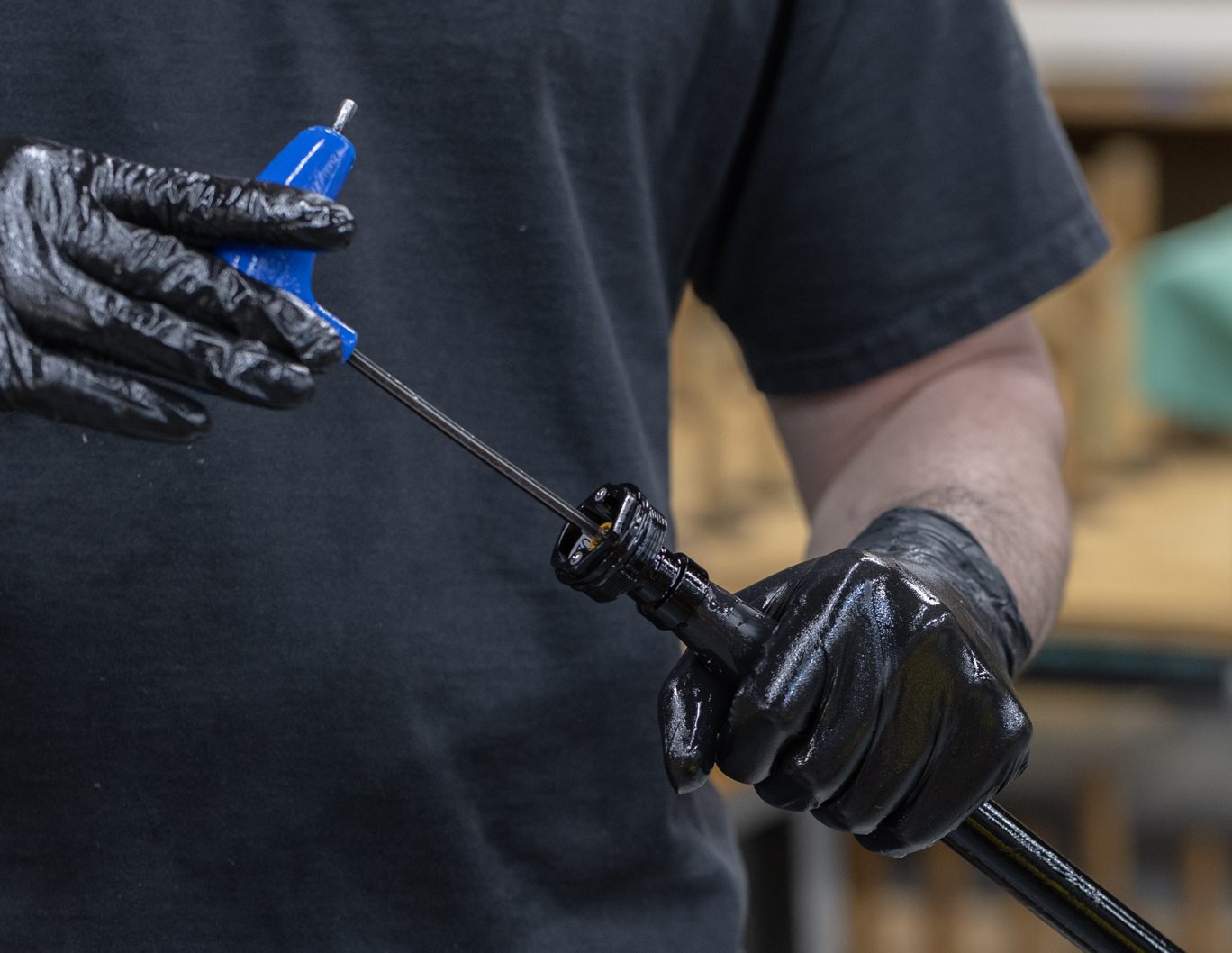
Closing Low Speed Compression 1
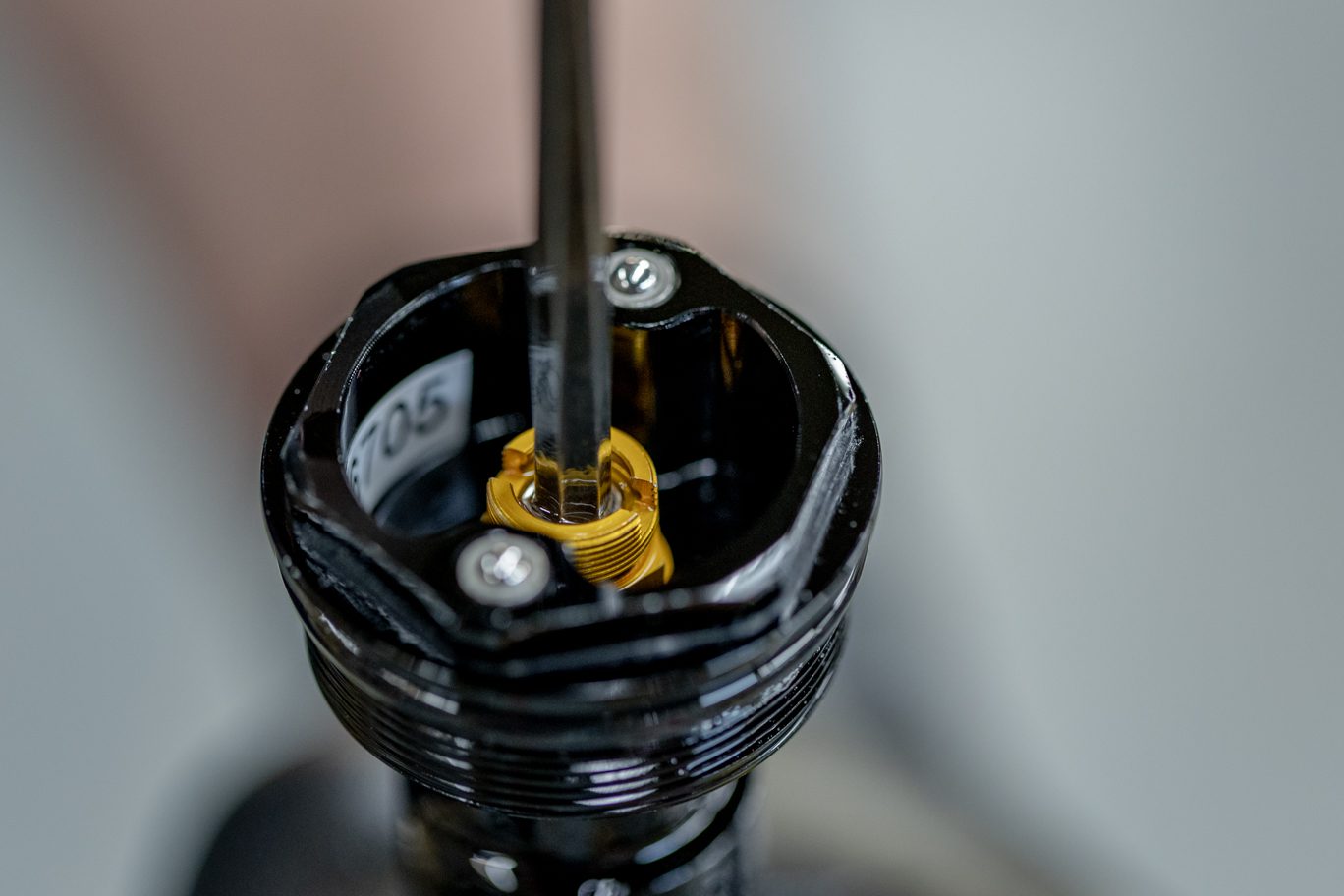
Closing Low Speed Compression 2
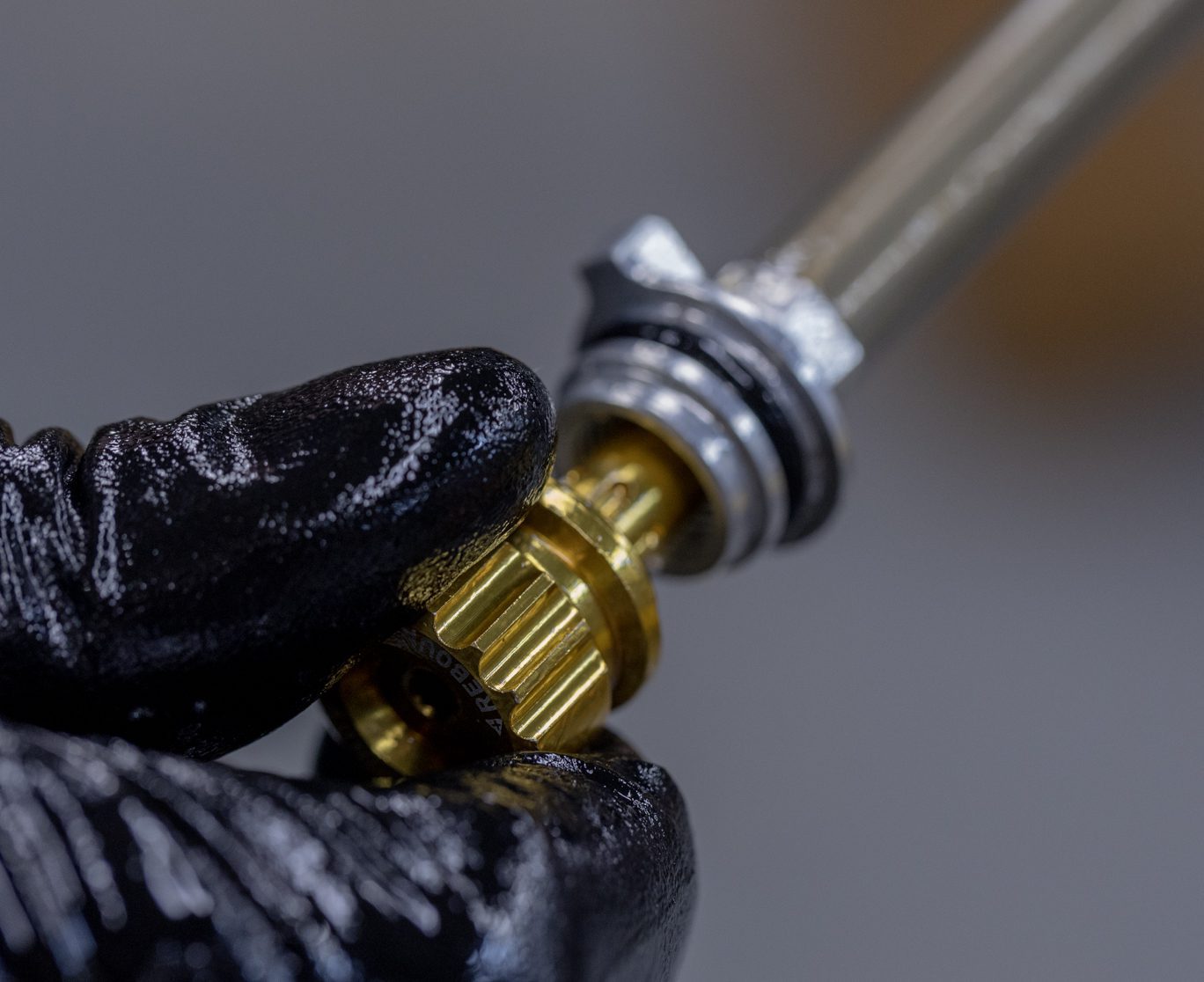
Closing Rebound
Damper Install
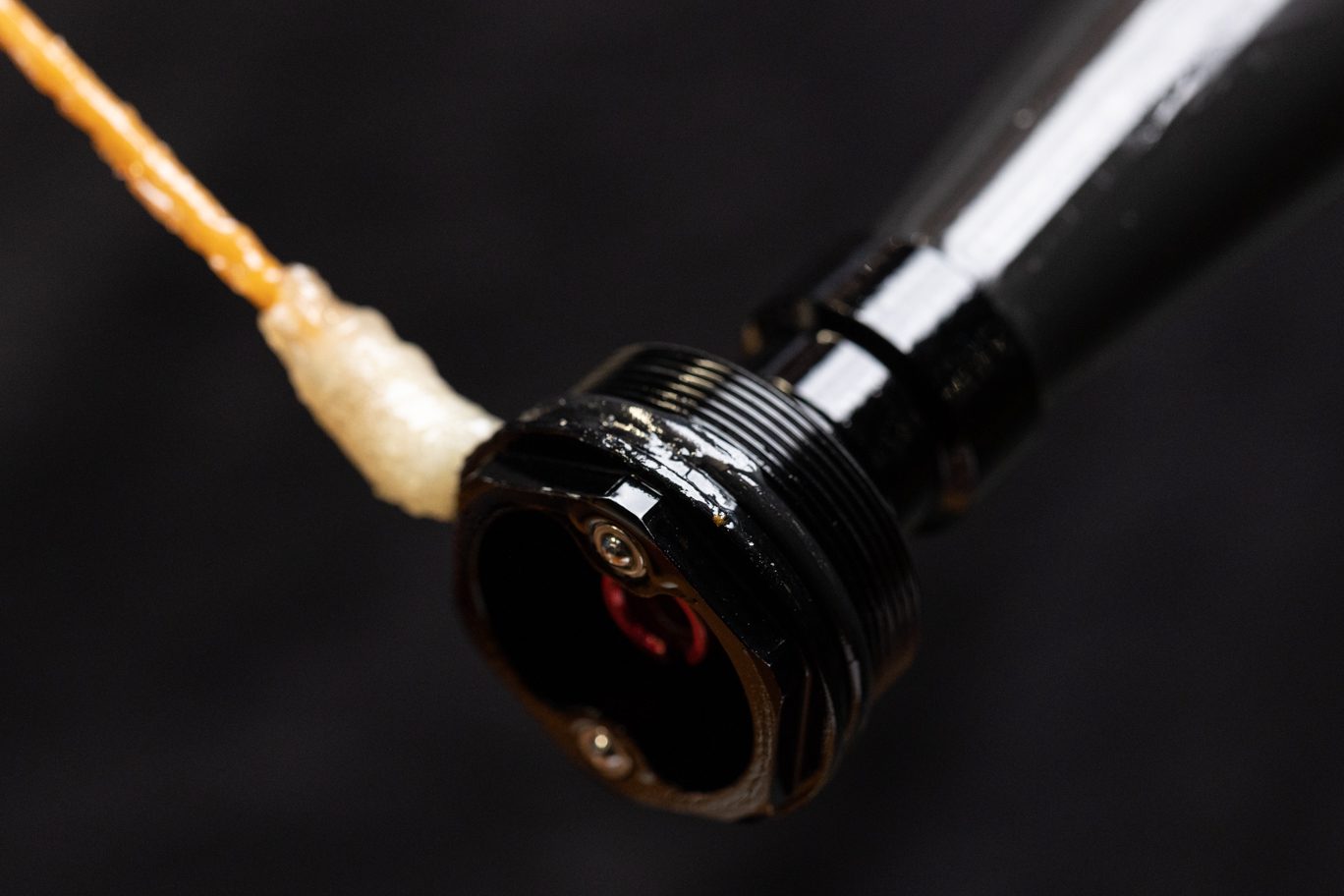
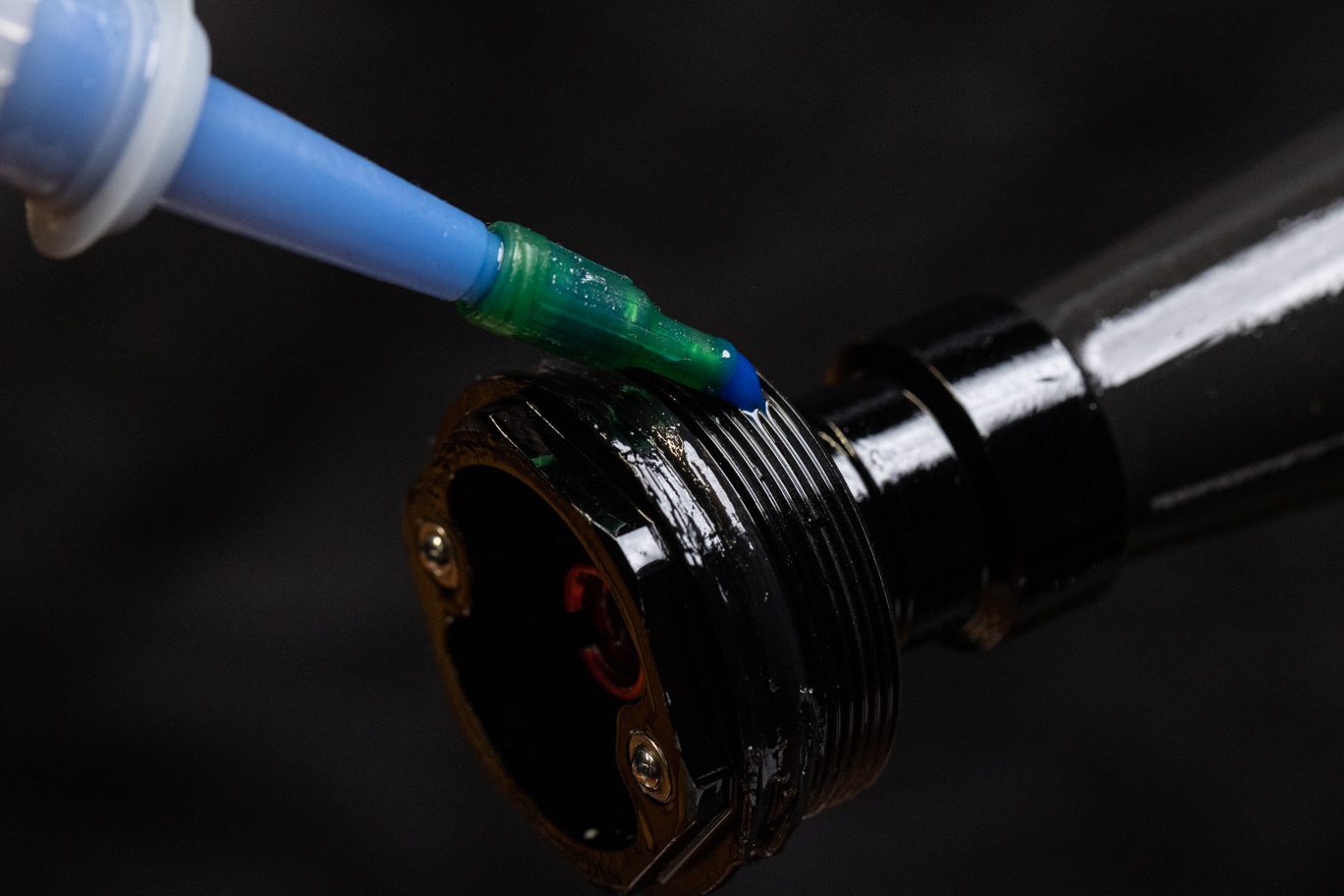

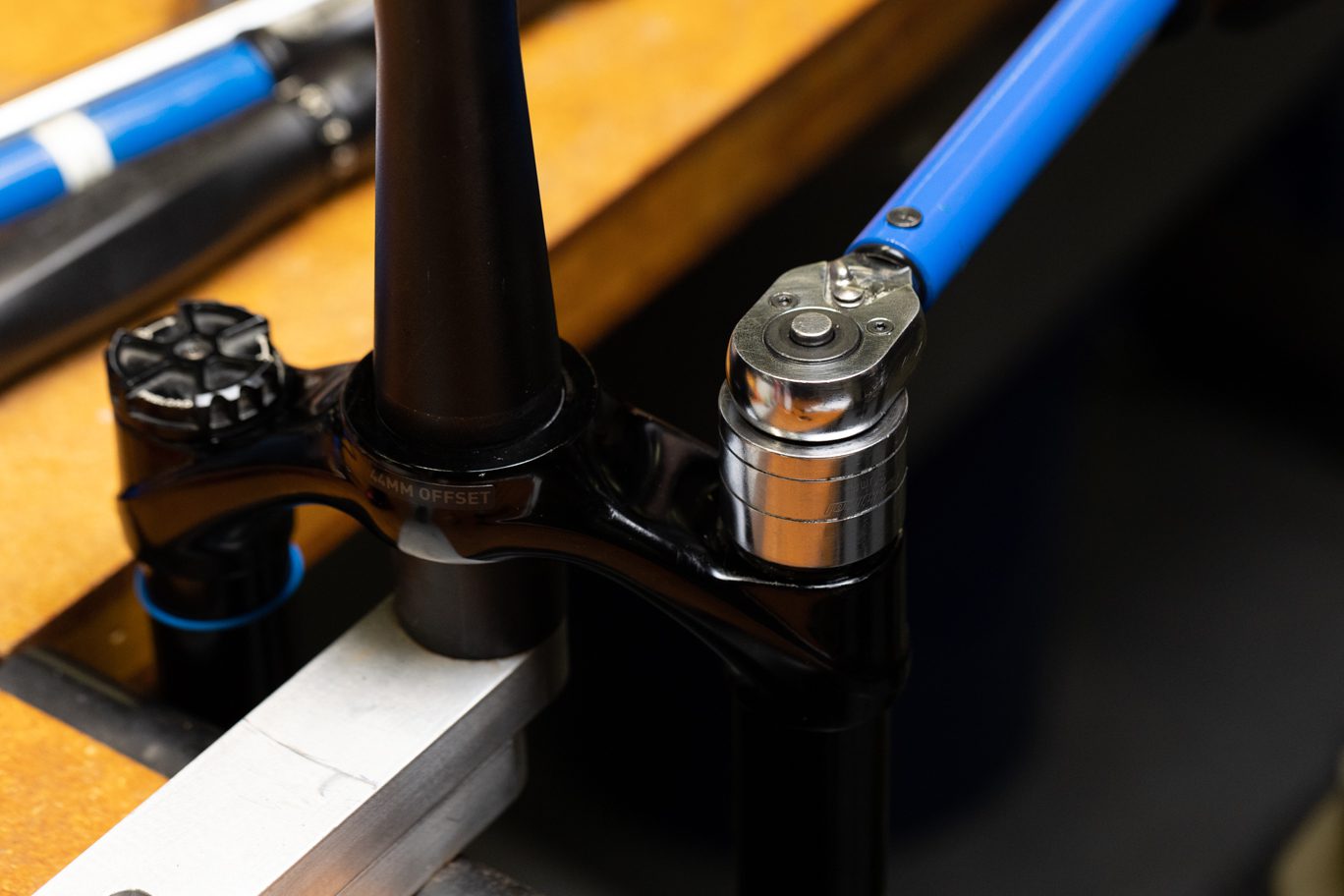
Step 1 – Damper Install
Lightly grease o-ring on damper top cap. Apply blue Loctite (243) to damper top cap threads. Insert damper. Torque to 36 Nm using 30mm socket.
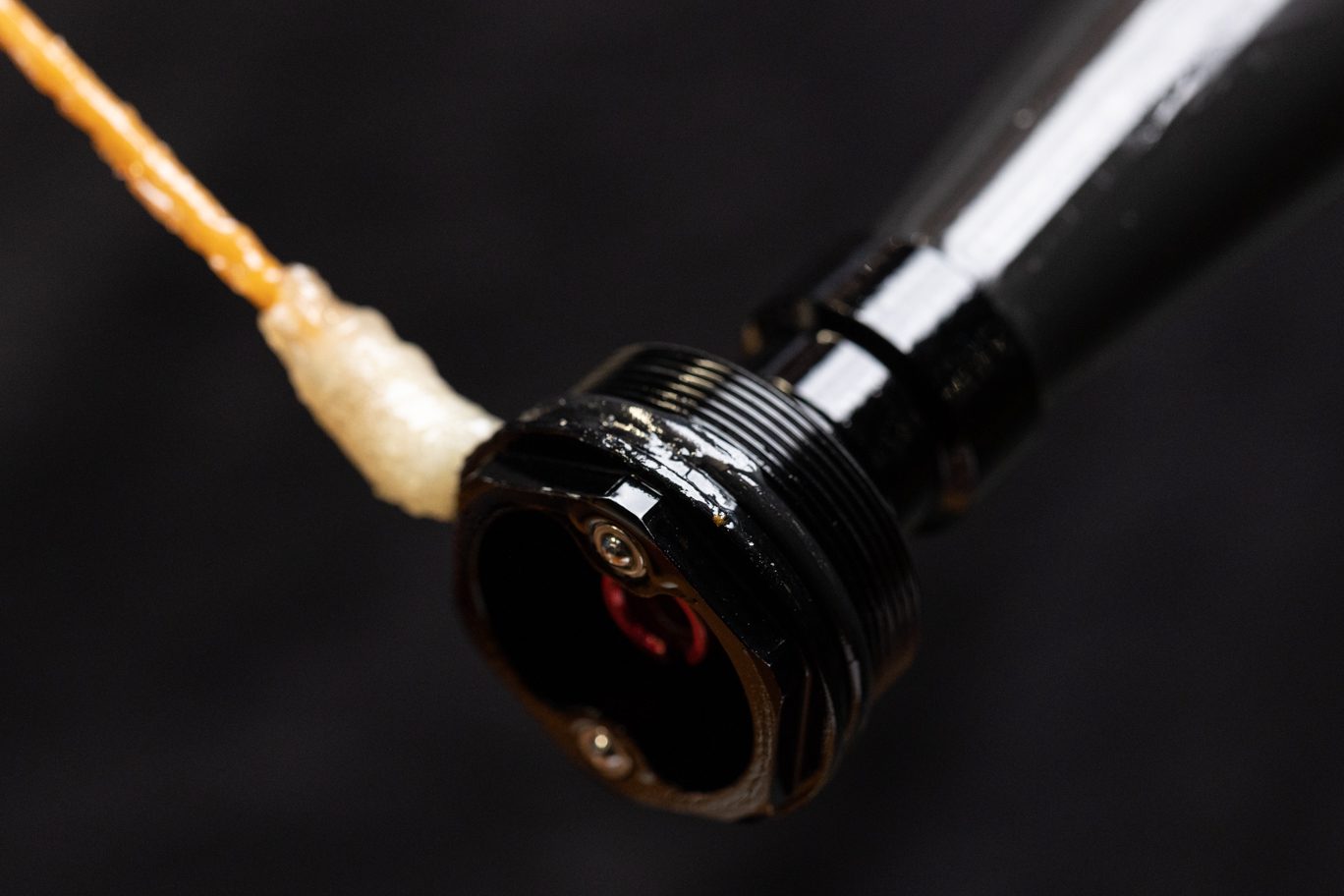
Applying Grease to Damper Top Cap O-Ring
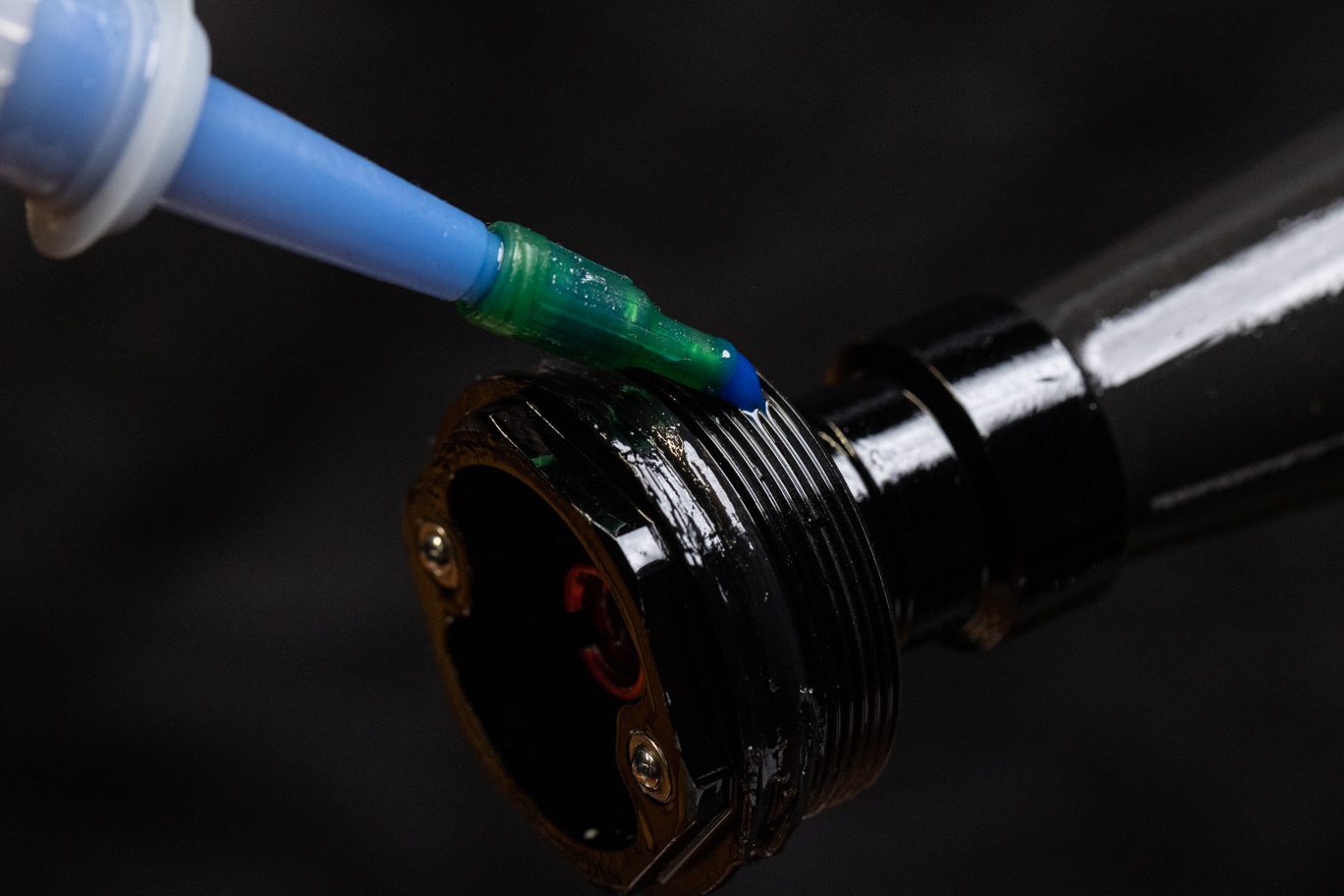
Applying Loctite to Damper Top Cap

Damper Installed
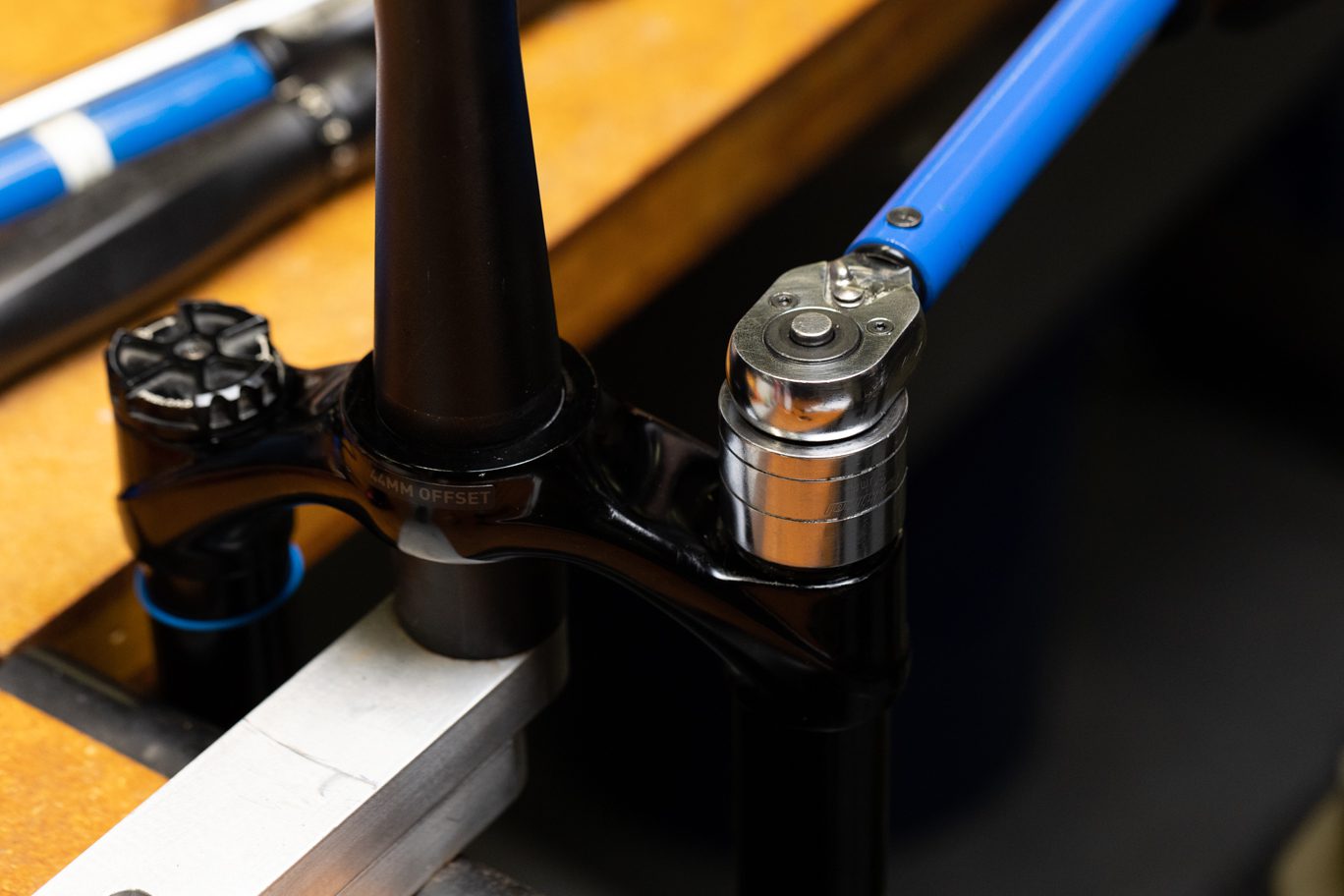
Damper Top Cap Torque
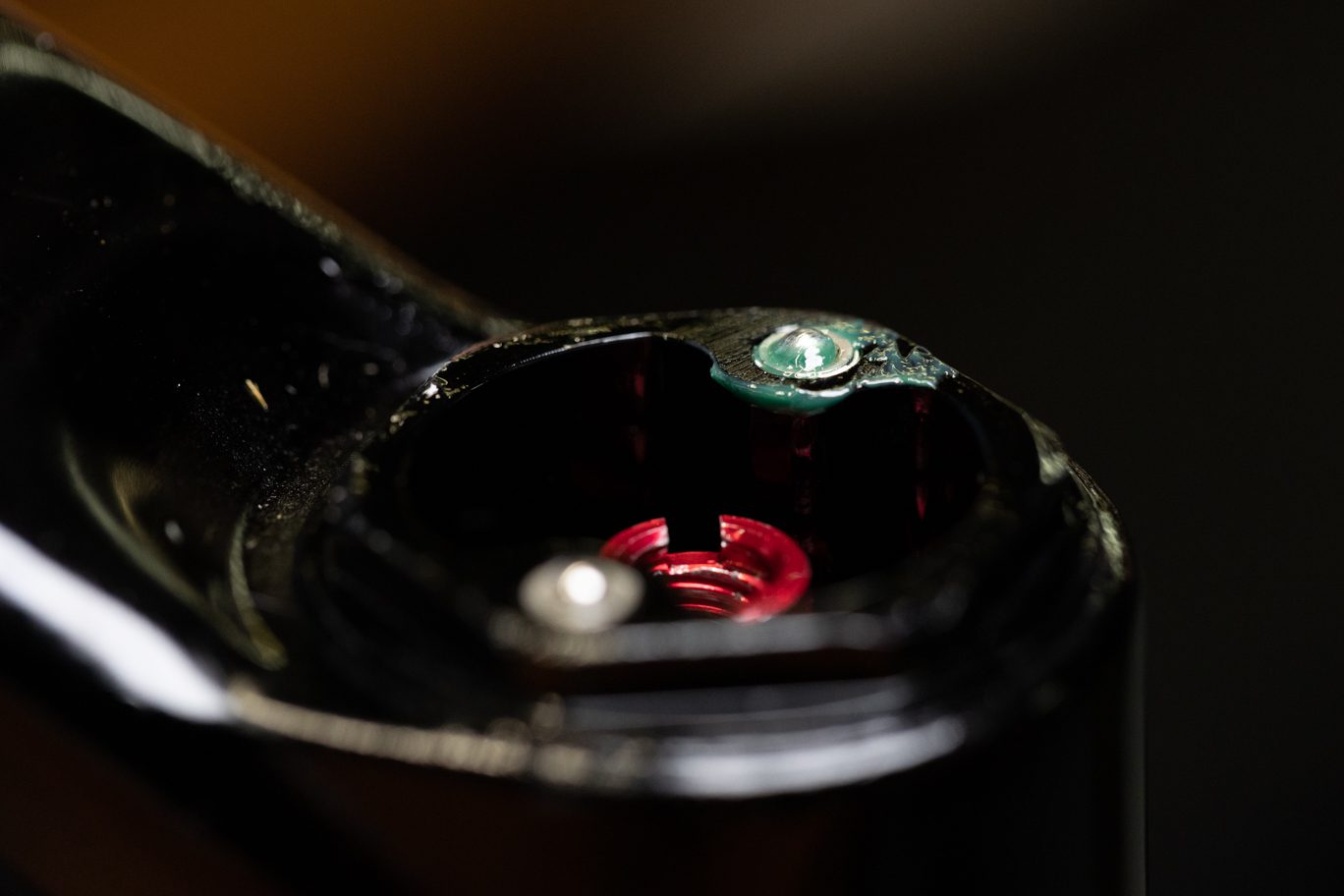
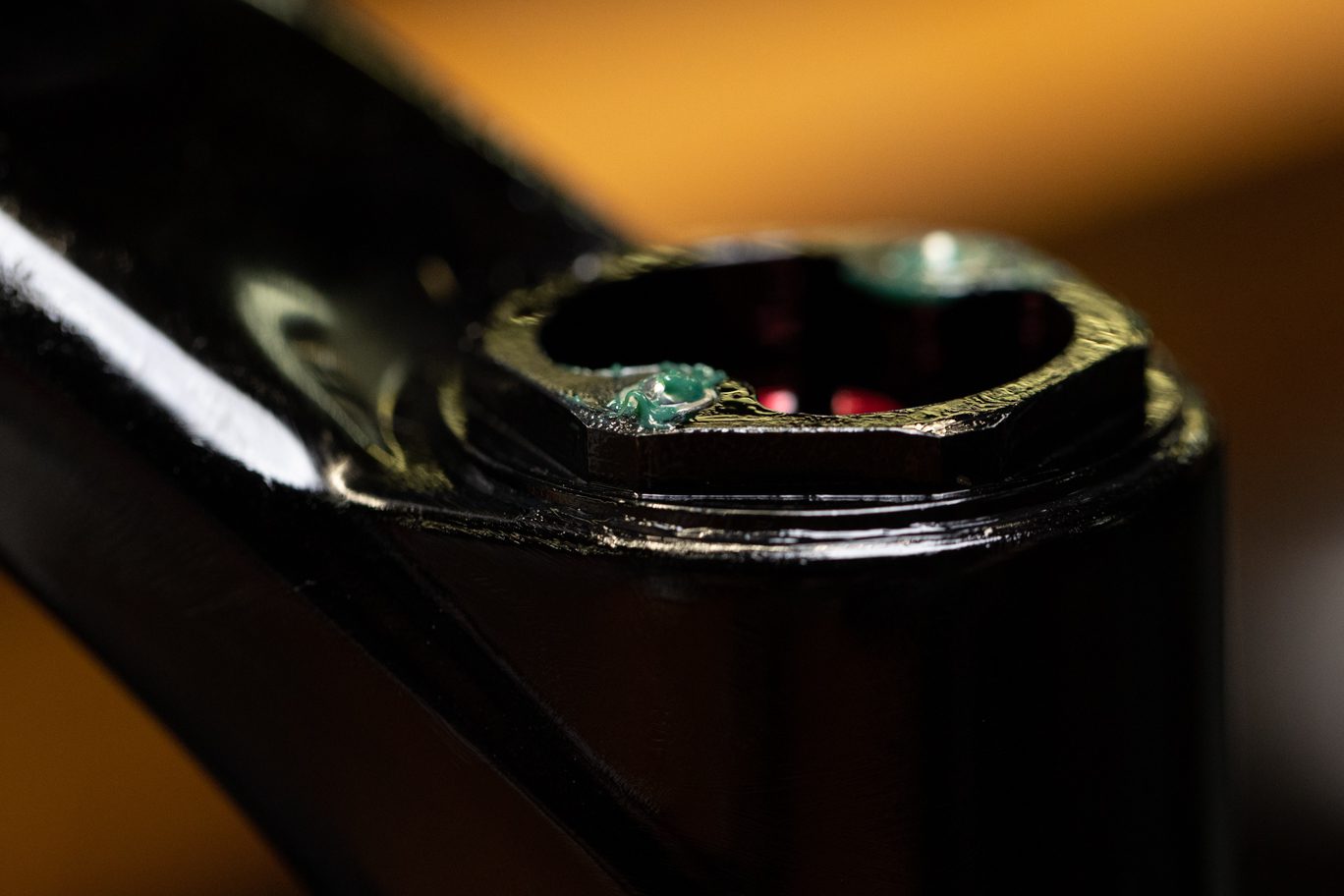
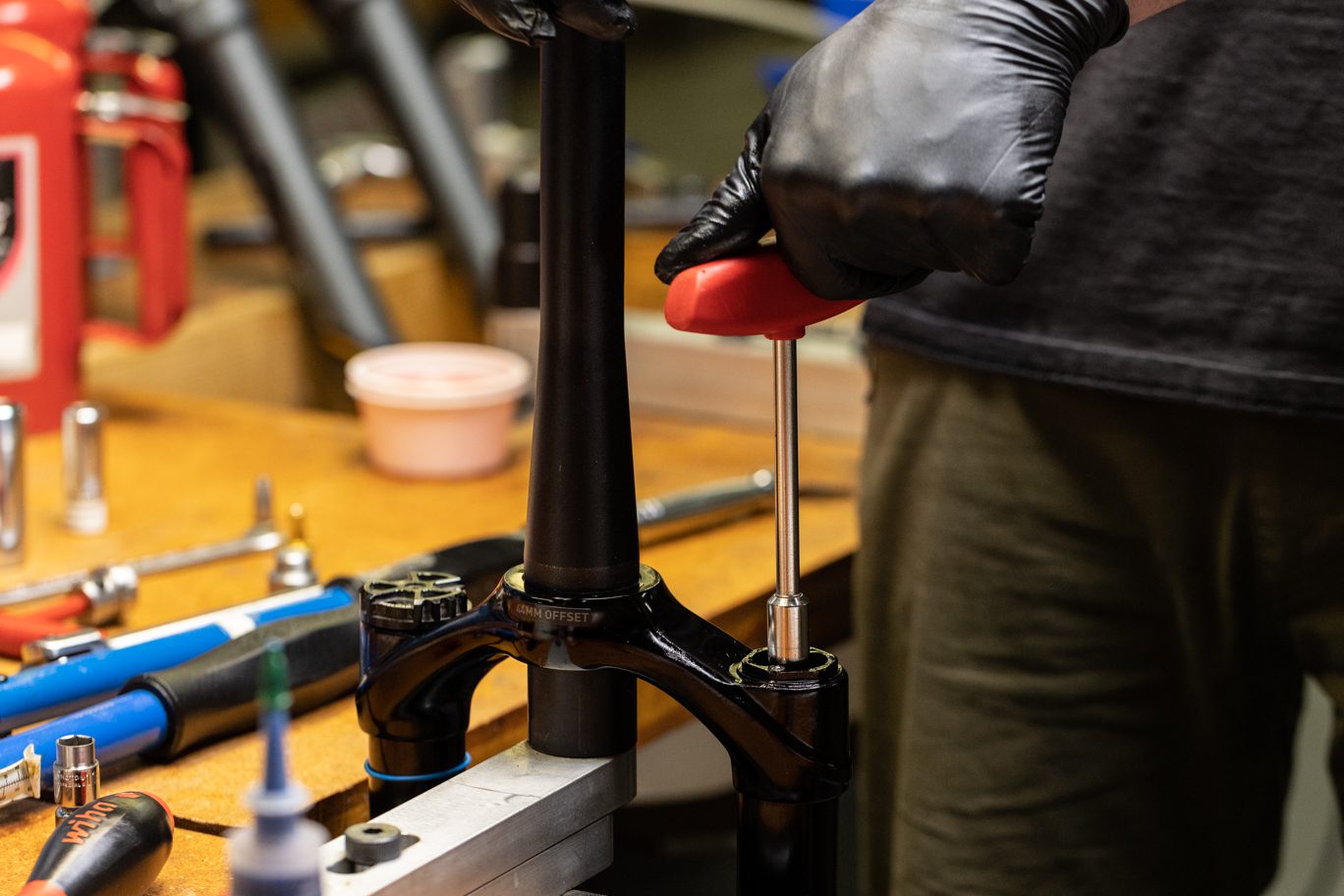
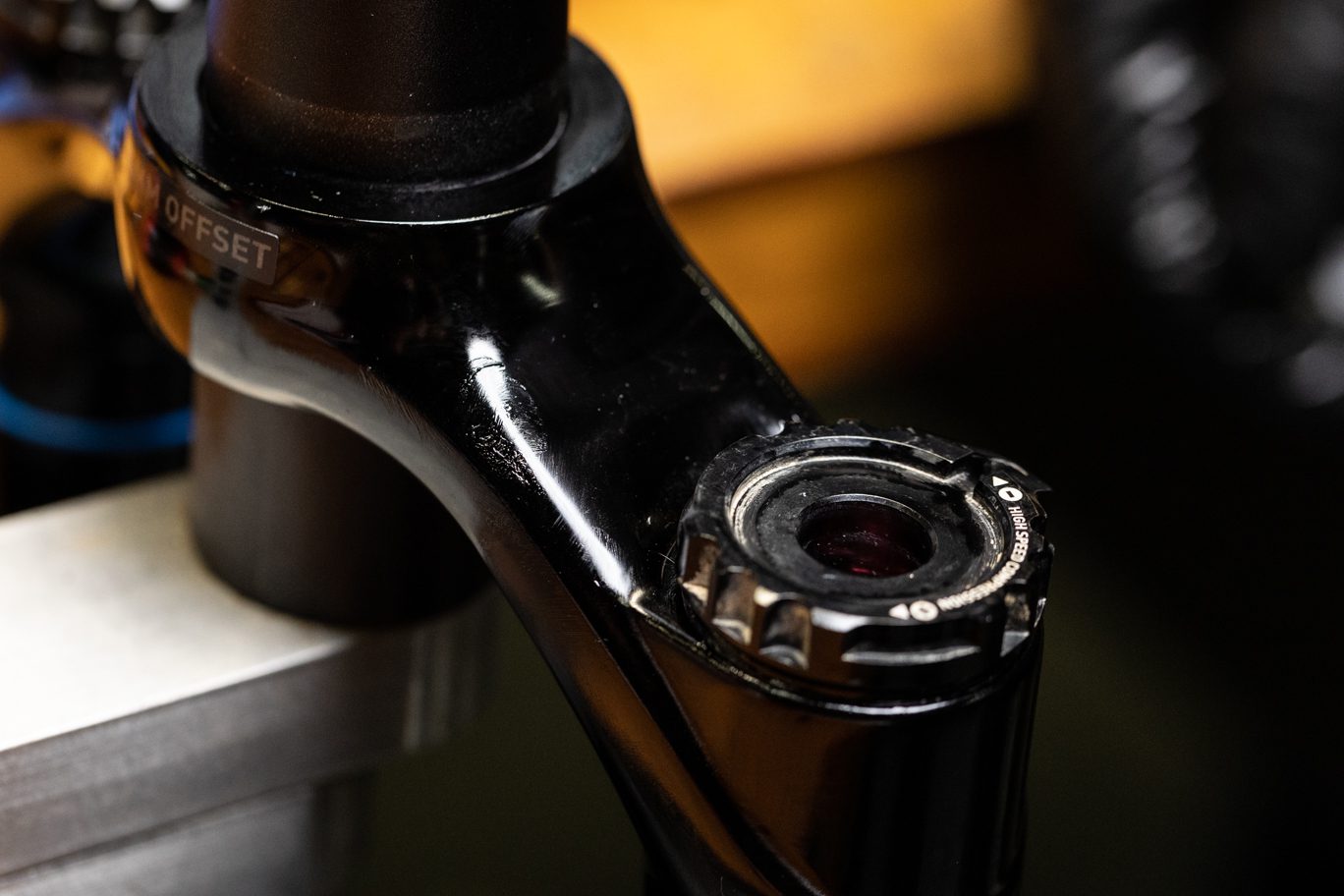
Step 2 – High Speed Compression Knob Install
Apply PolyLube to detents on the damper top cap. Fully open (counterclockwise) the High Speed compression (helix). Install High Speed knob. Note orientation with tab towards the front.
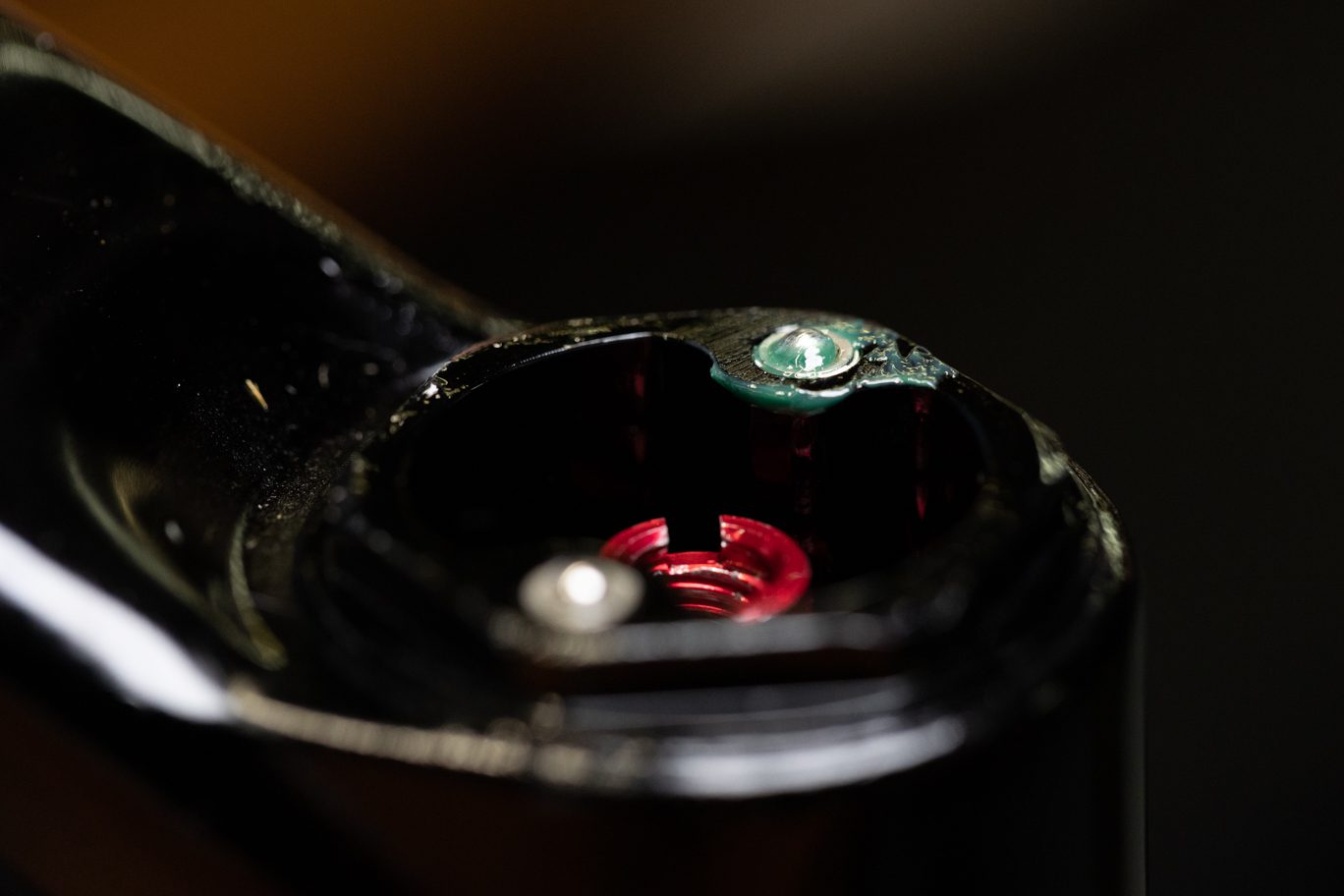
Greasing Top Cap Detents
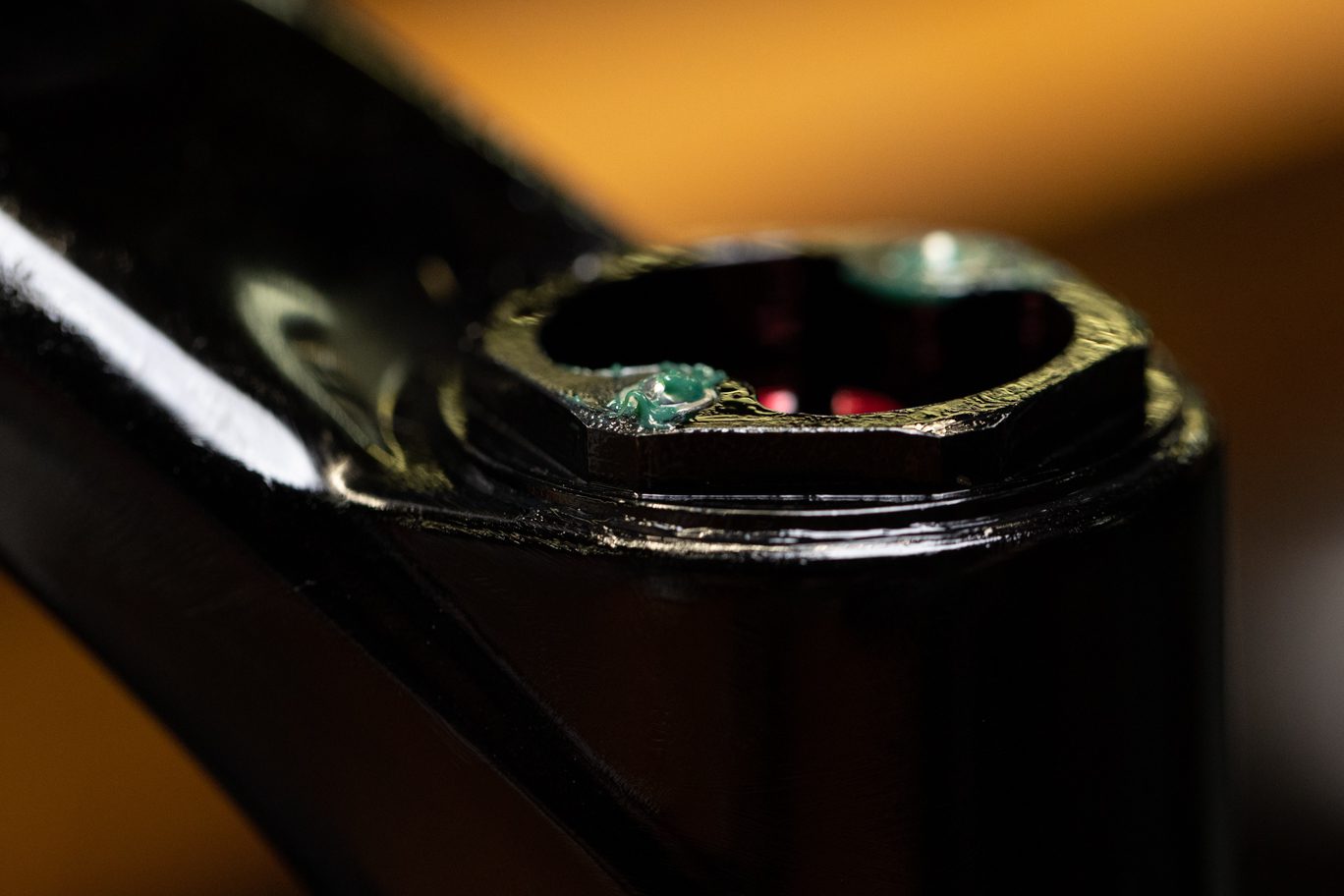
Top Cap Detents Greased
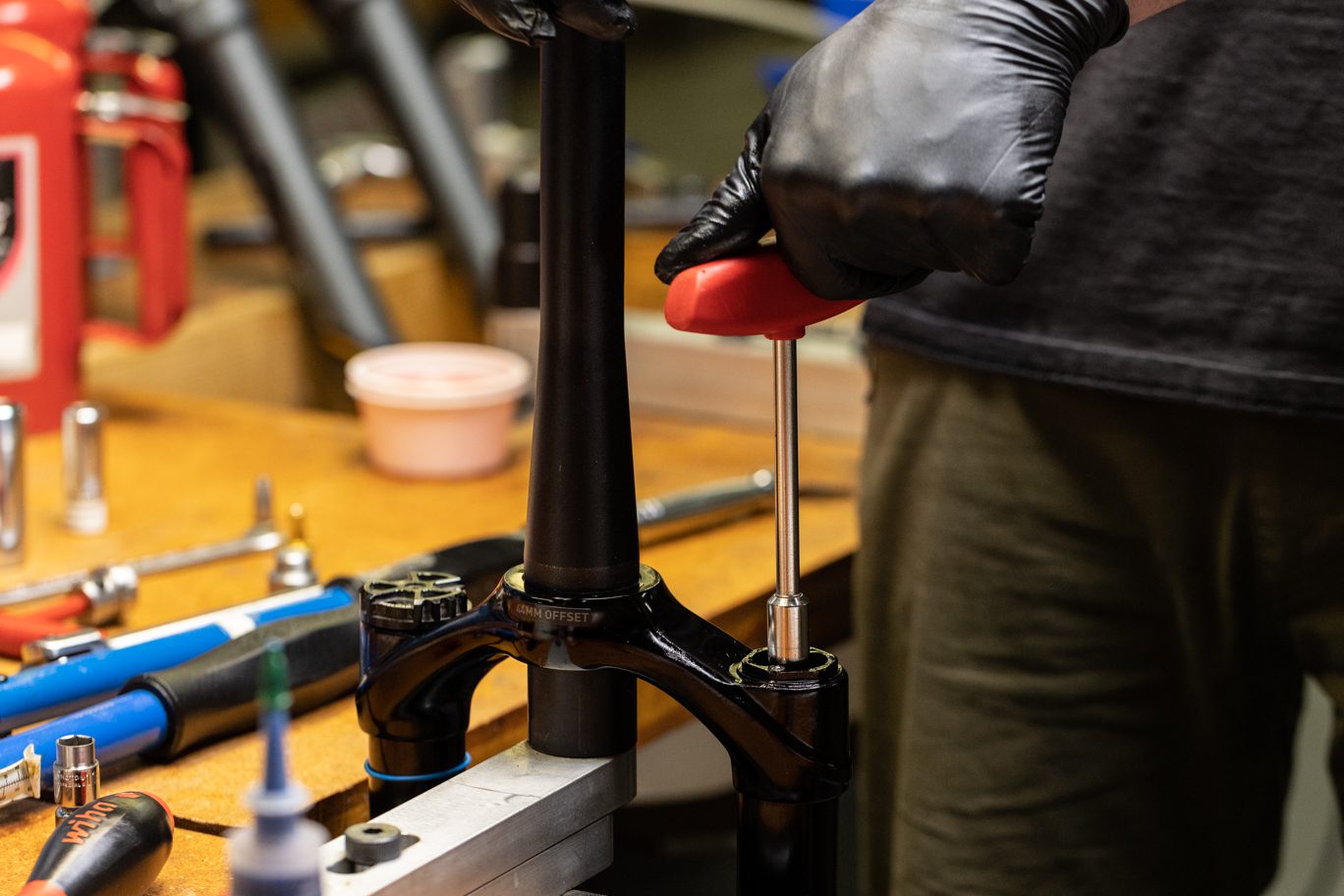
Fully Opening HSC Adjuster
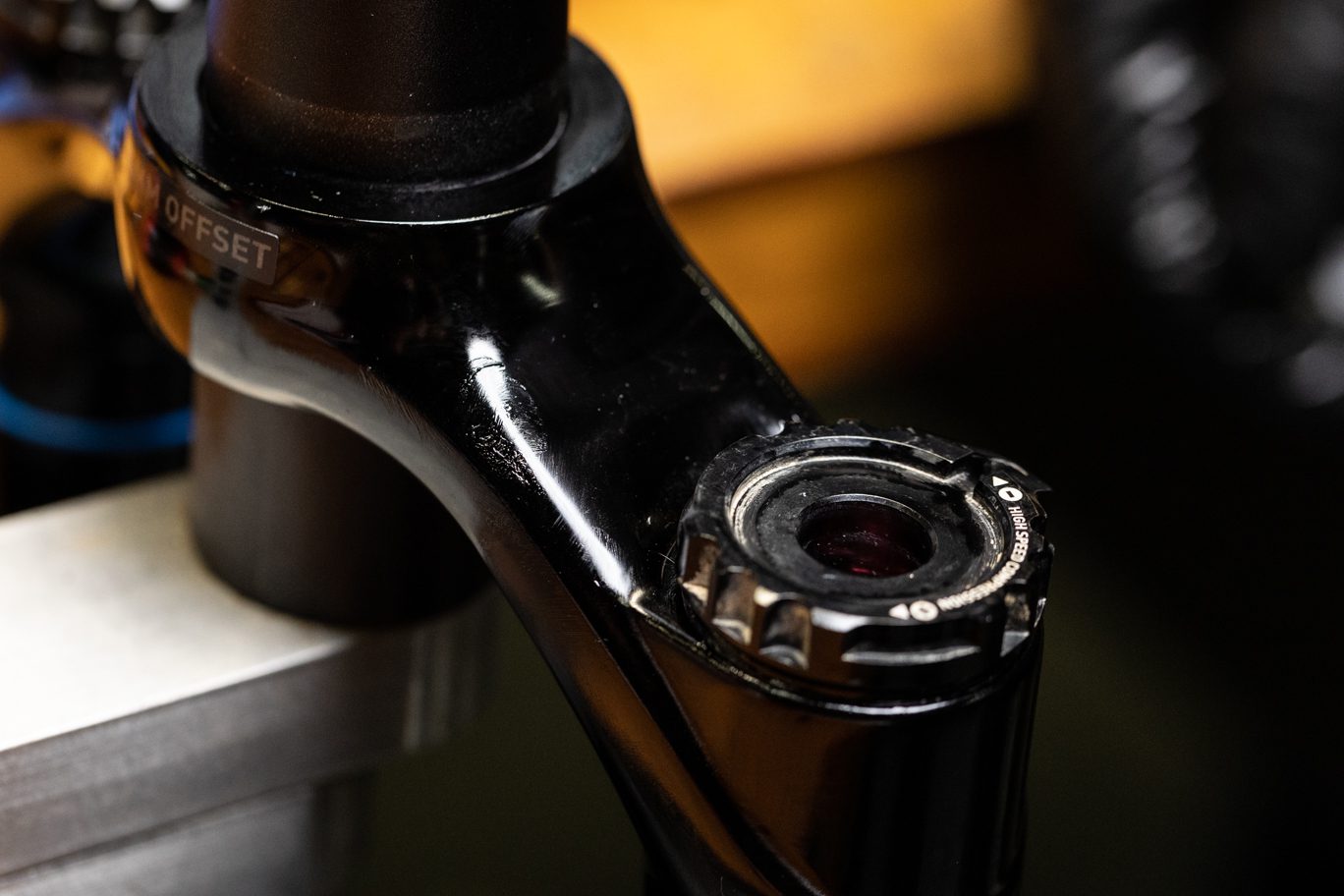
HSC Knob Installed

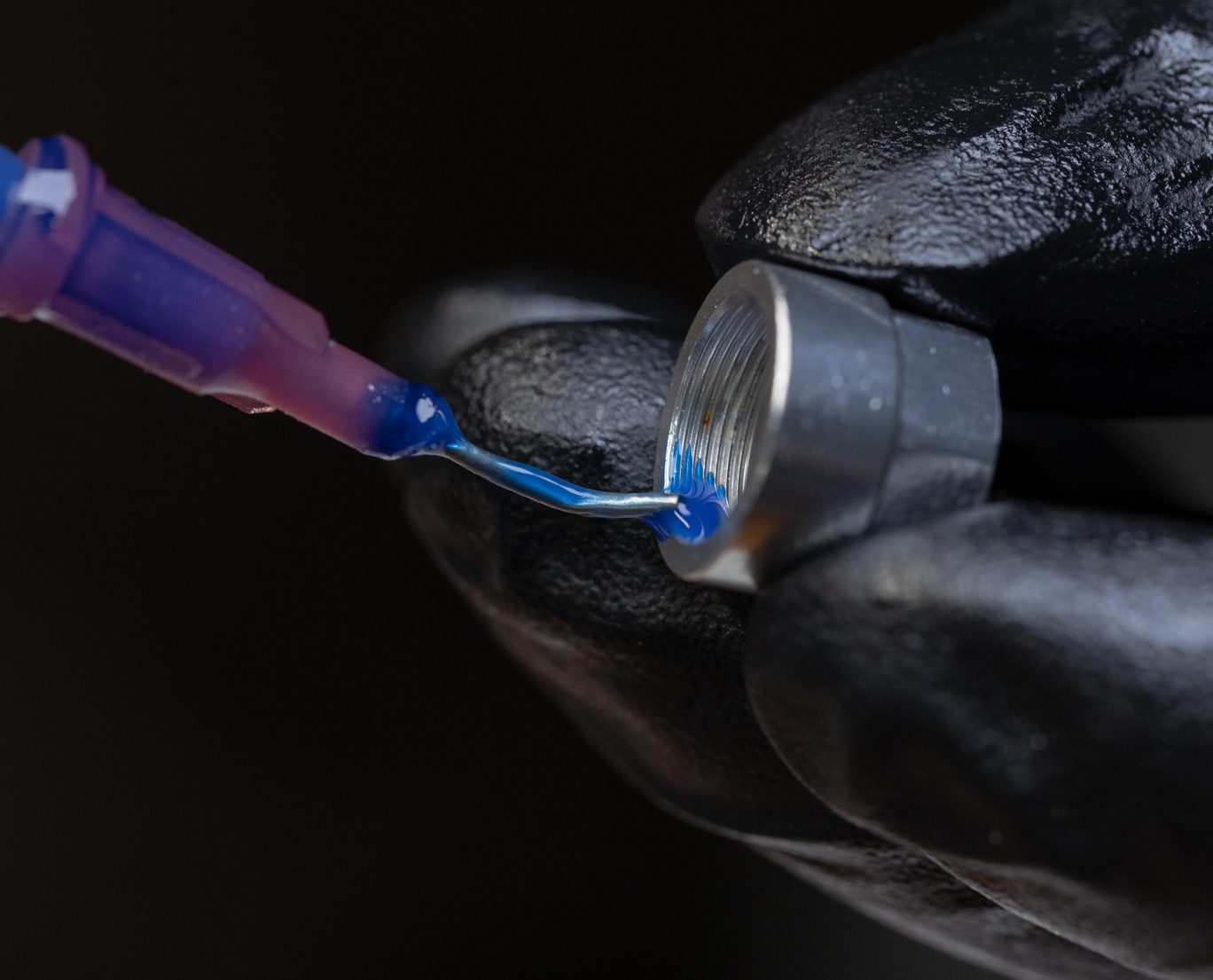
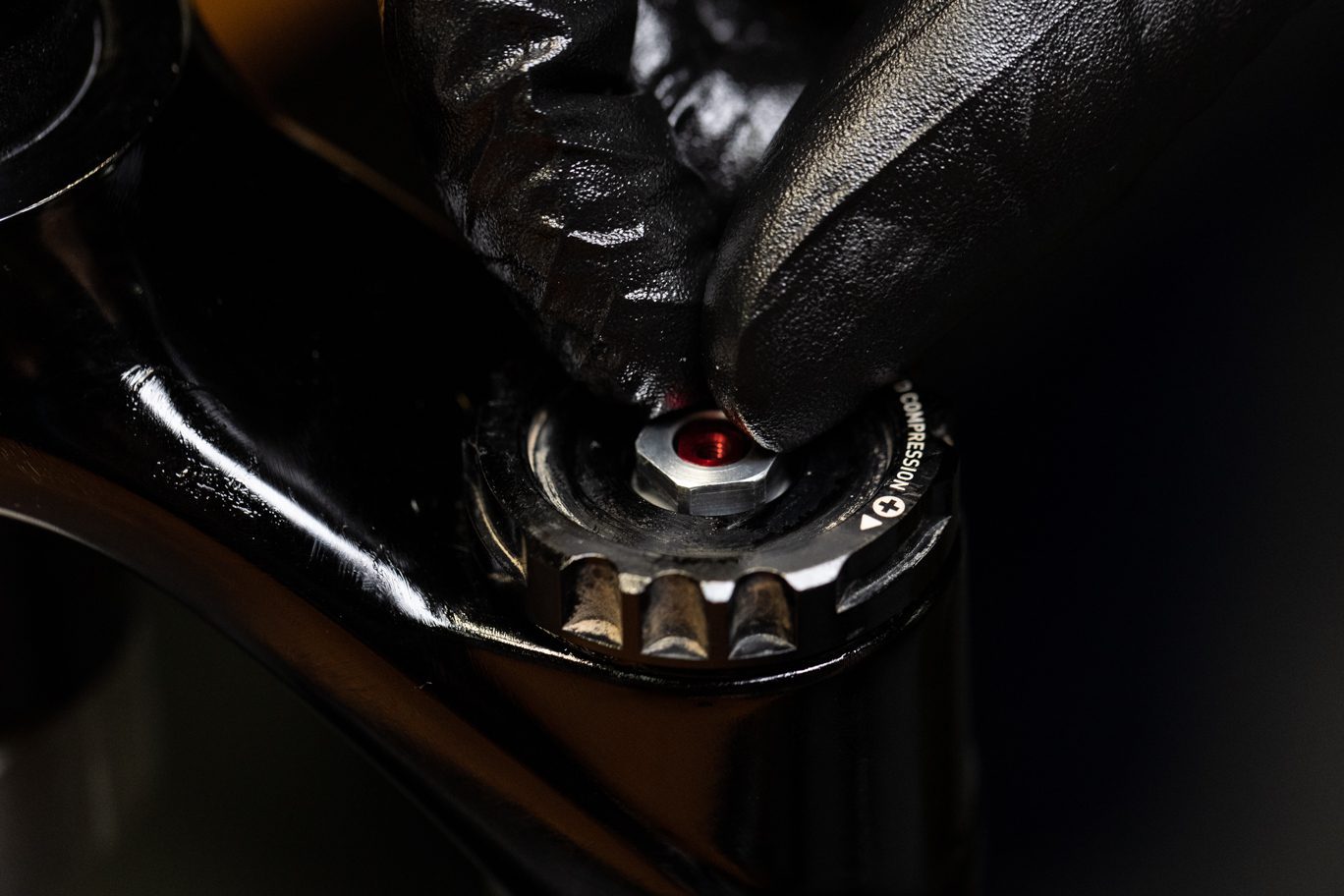
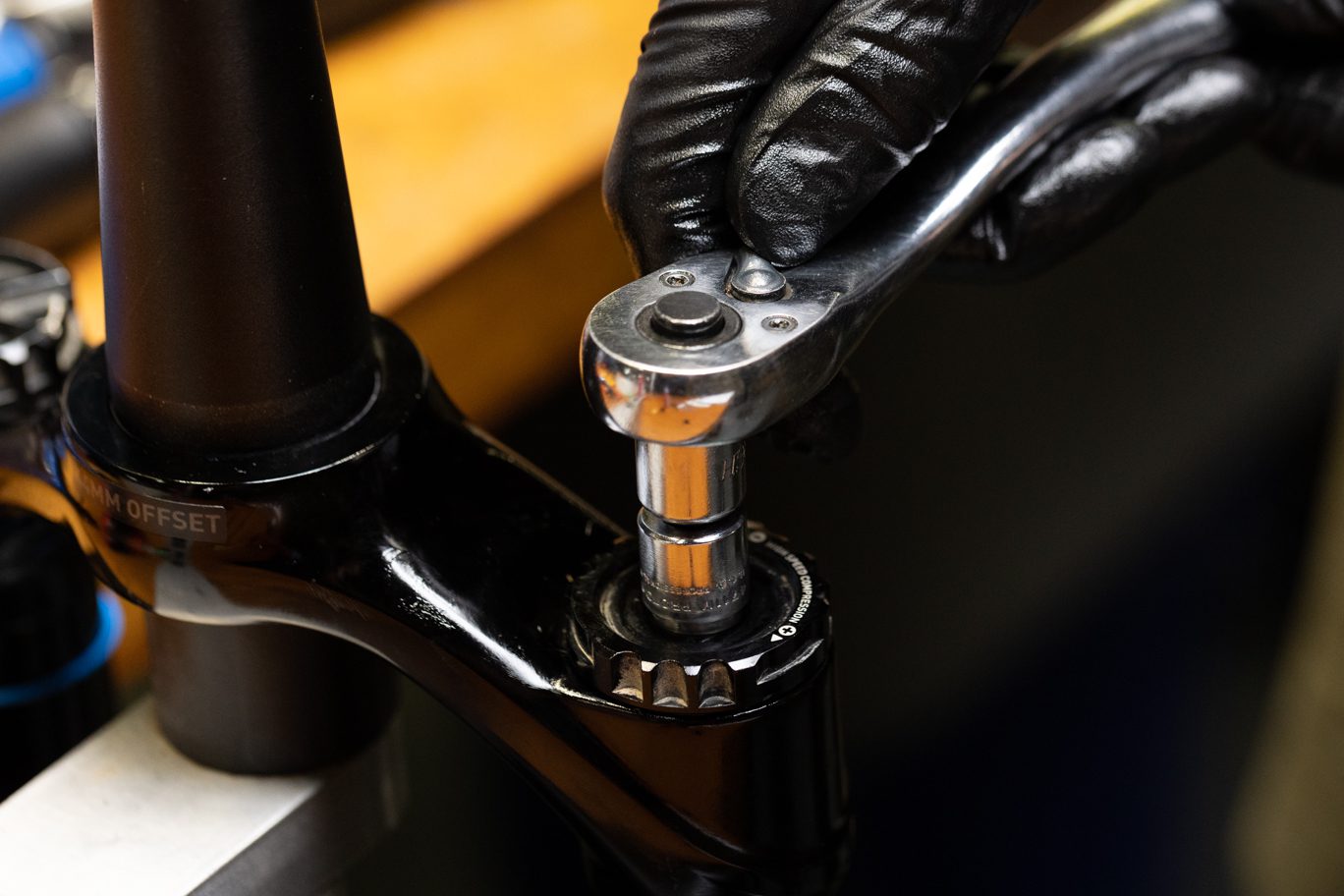
Step 3 – Compression Retaining Nut Install
Install red take up adapter. Apply blue Loctite (243) to inner threads on compression retaining nut. Install retaining nut. Tighten with 11mm compression nut socket until hand tight. Note knob will rotate to closed position.

LSC Take Up Adjuster Insall
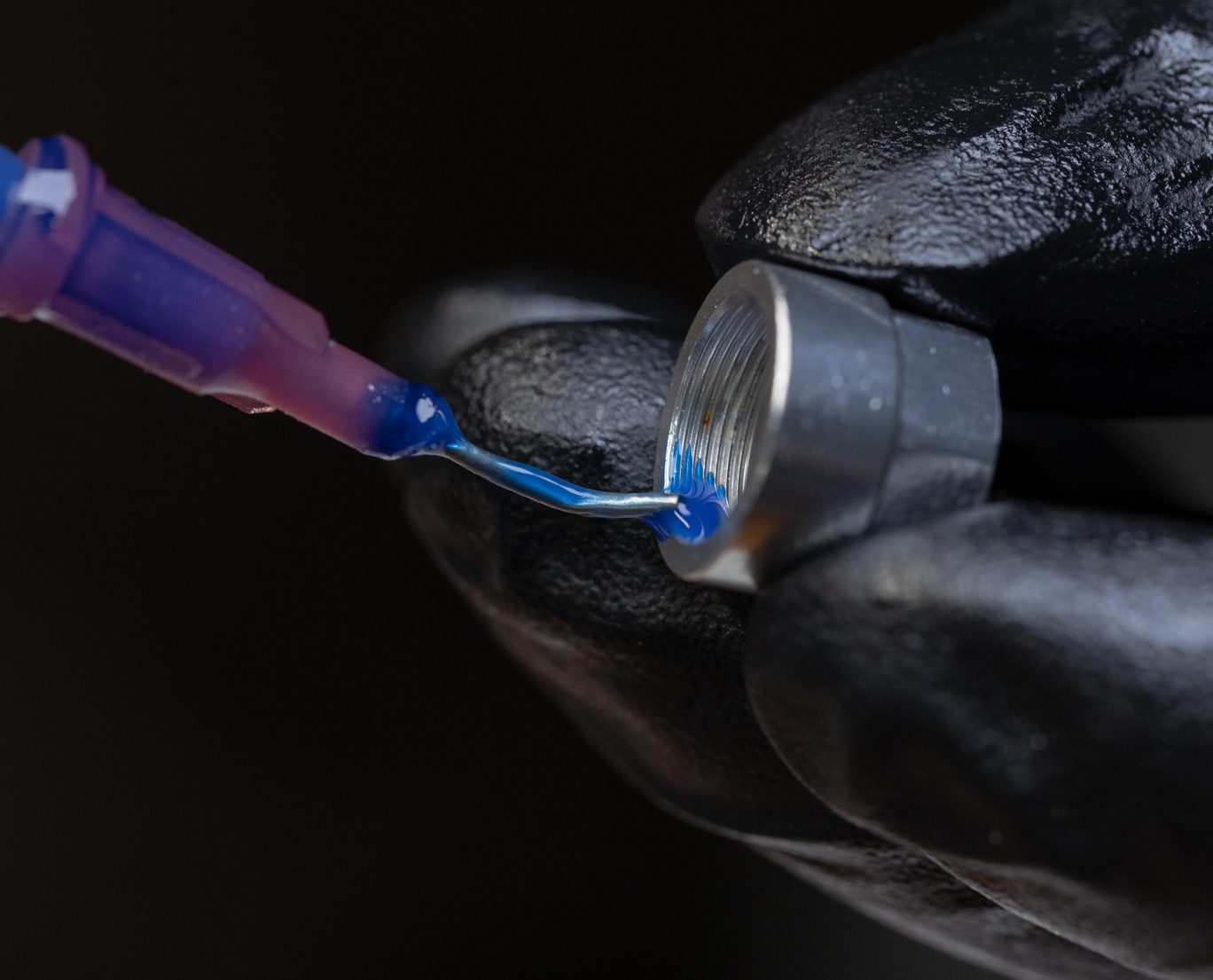
Applying Loctite to Retaining Nut
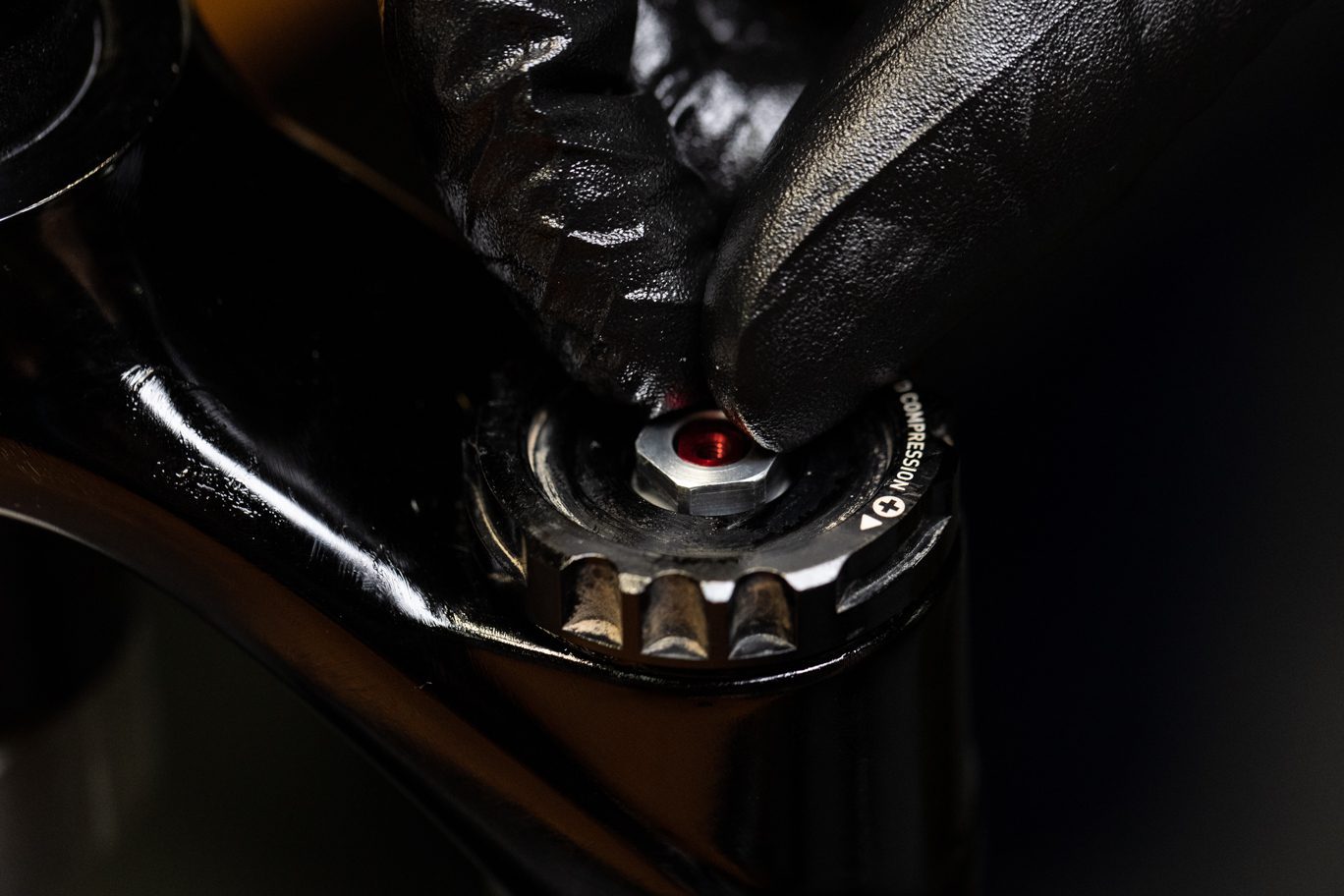
LSC Retaining Nut Install
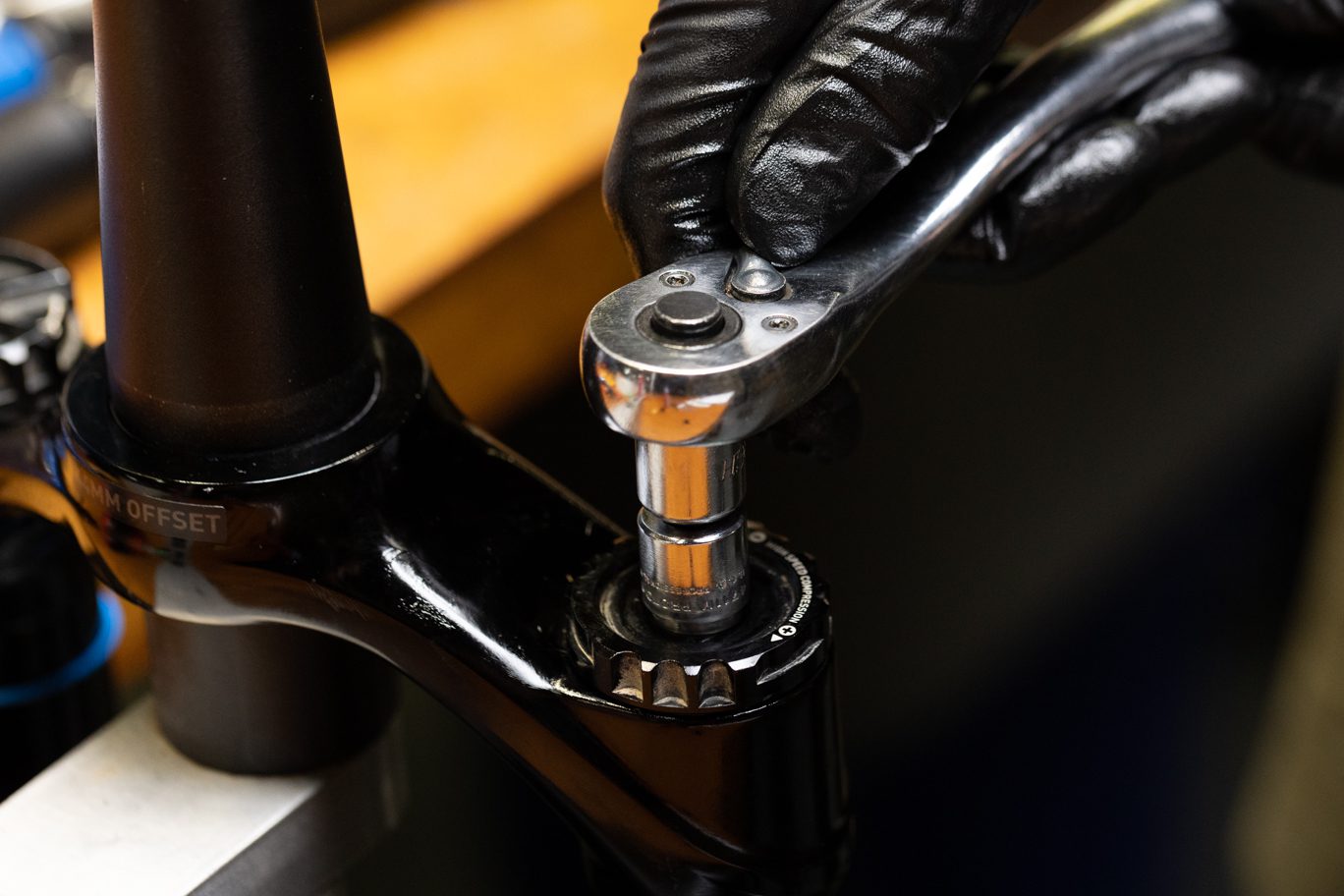
LSC Retaining Nut Tighten
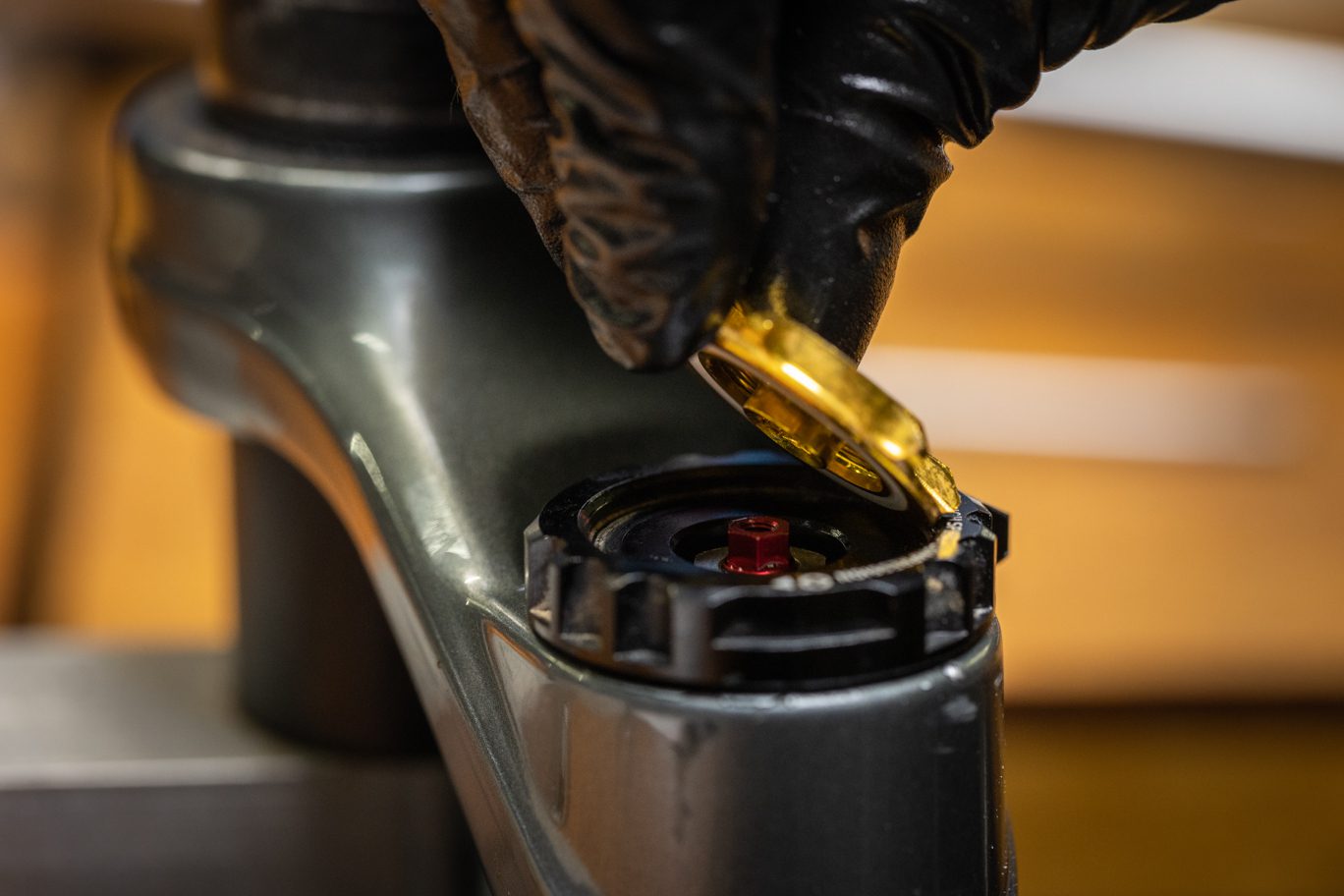

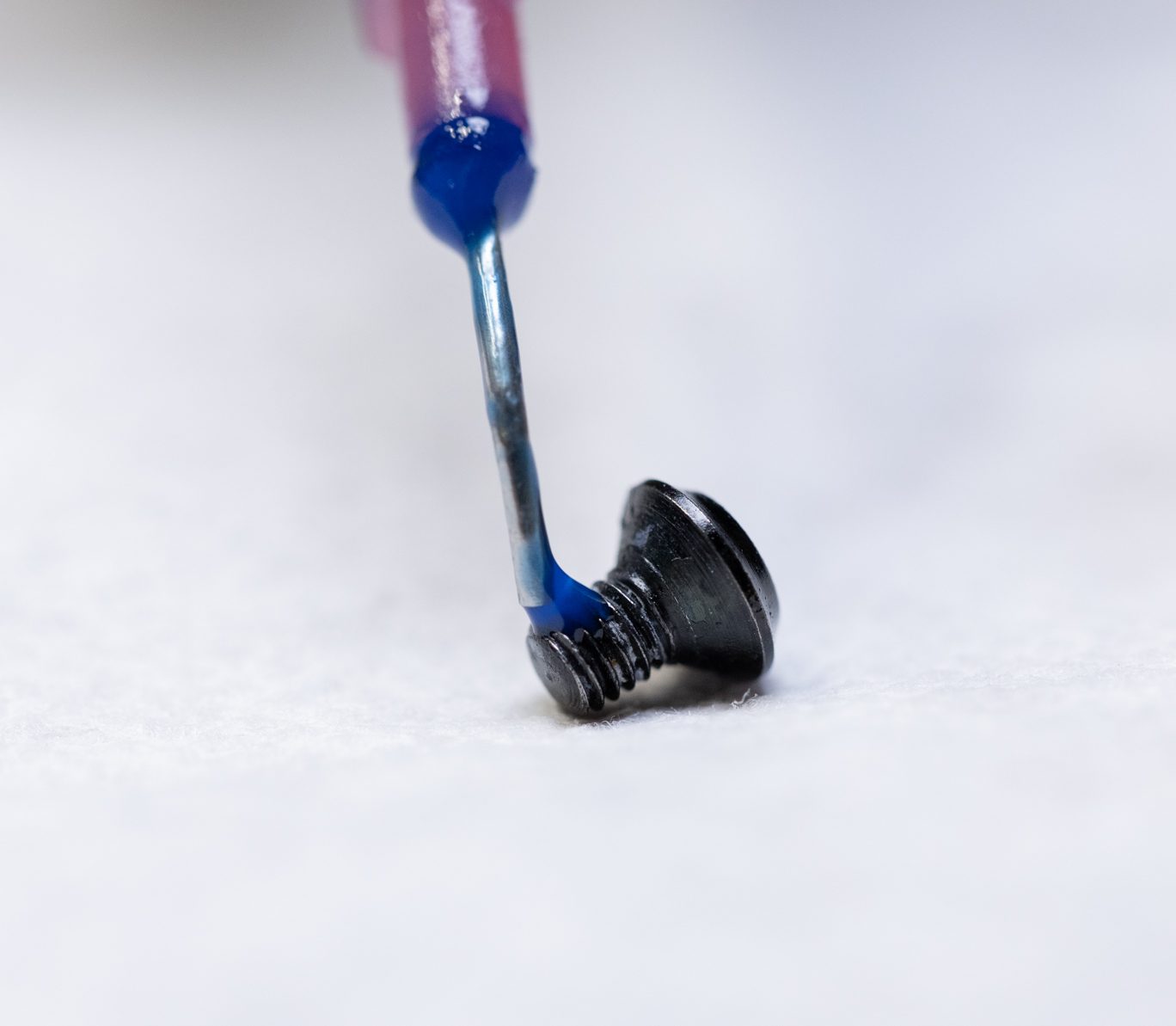
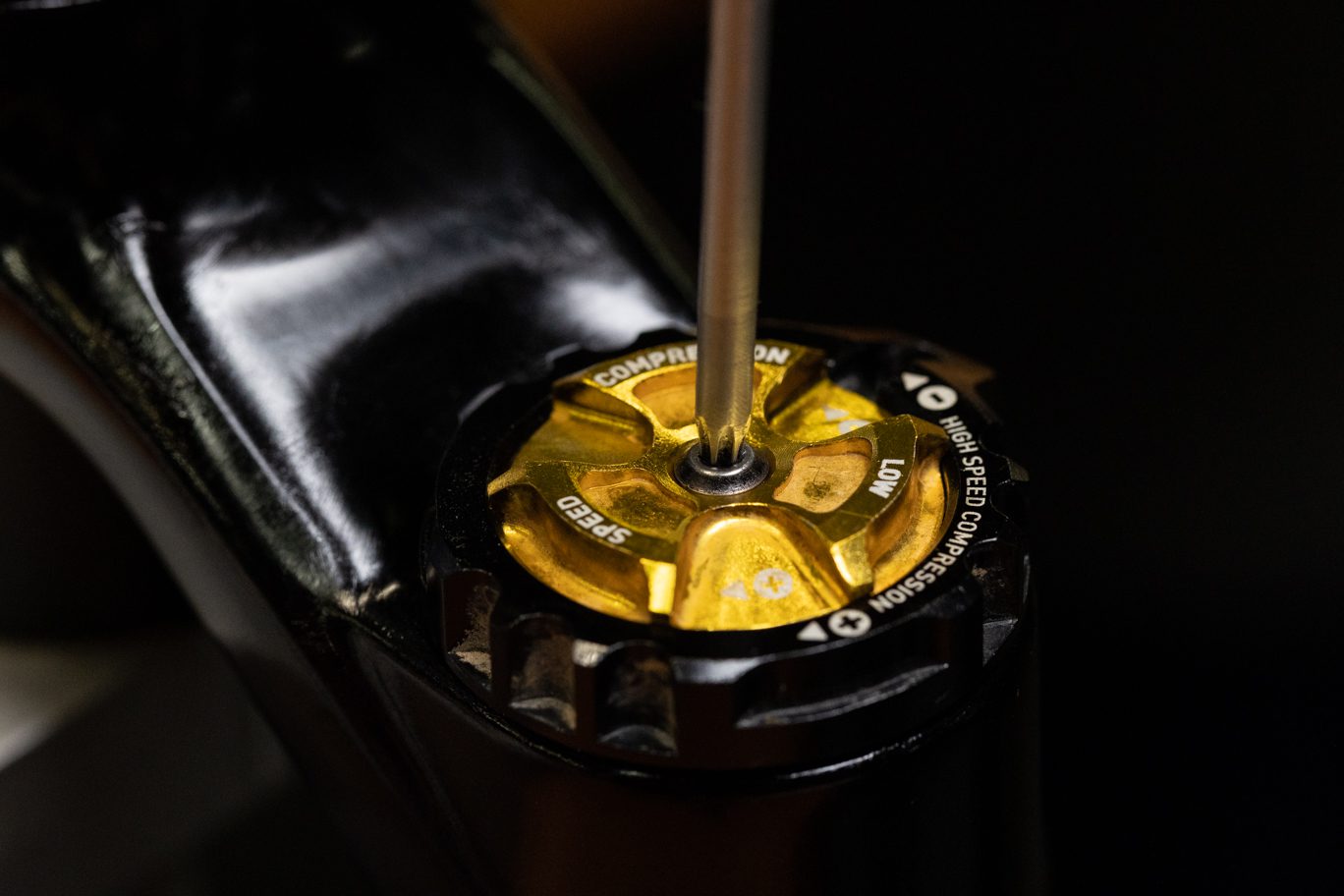
Step 4 – Low Speed Compression Knob Install
Install Low Speed knob. Apply blue Loctite (243) to threads on Low Speed compression screw. Install screw and torque to 1.6 Nm with T10.
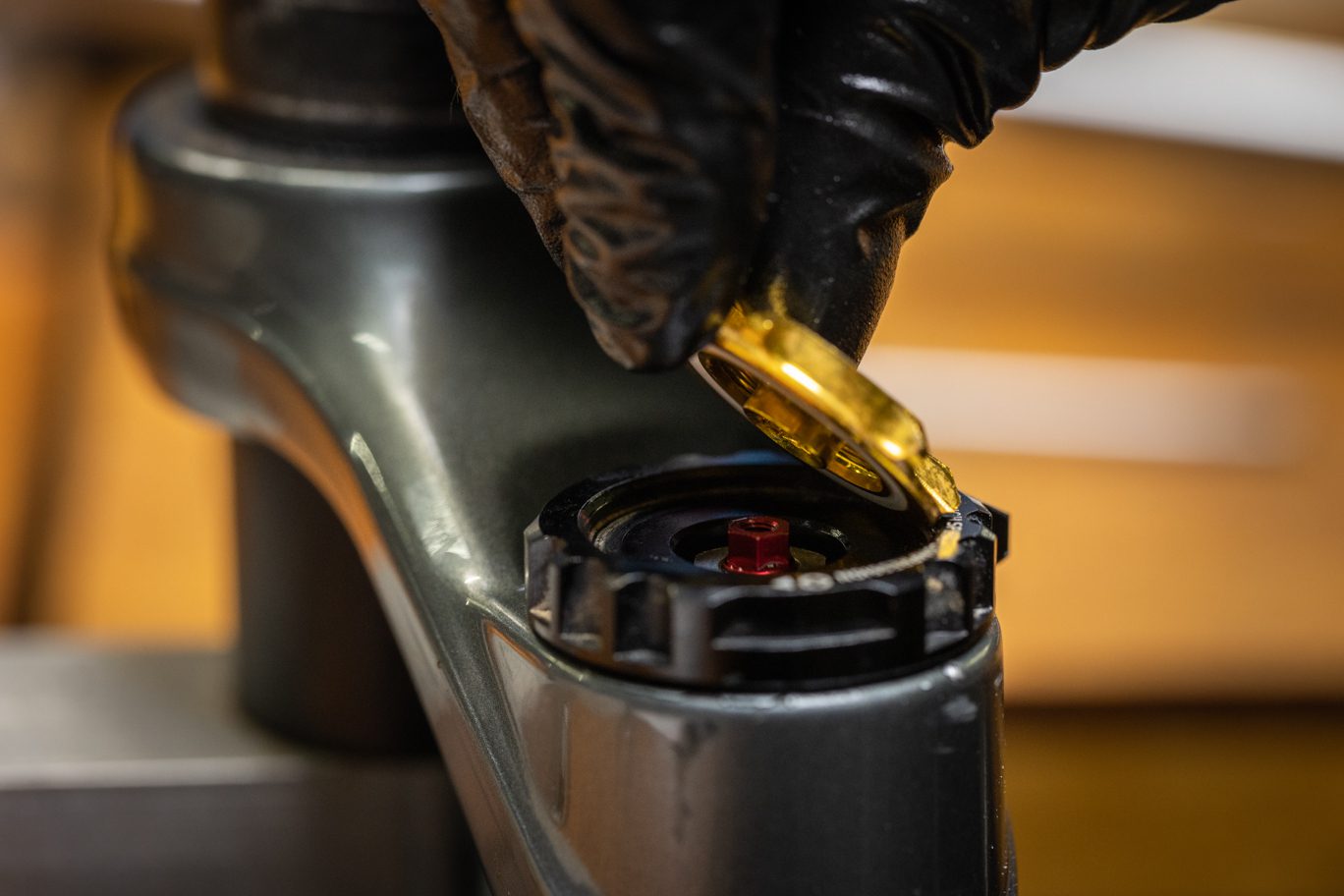
Low Speed Knob Install

LSC Knob Screw Location
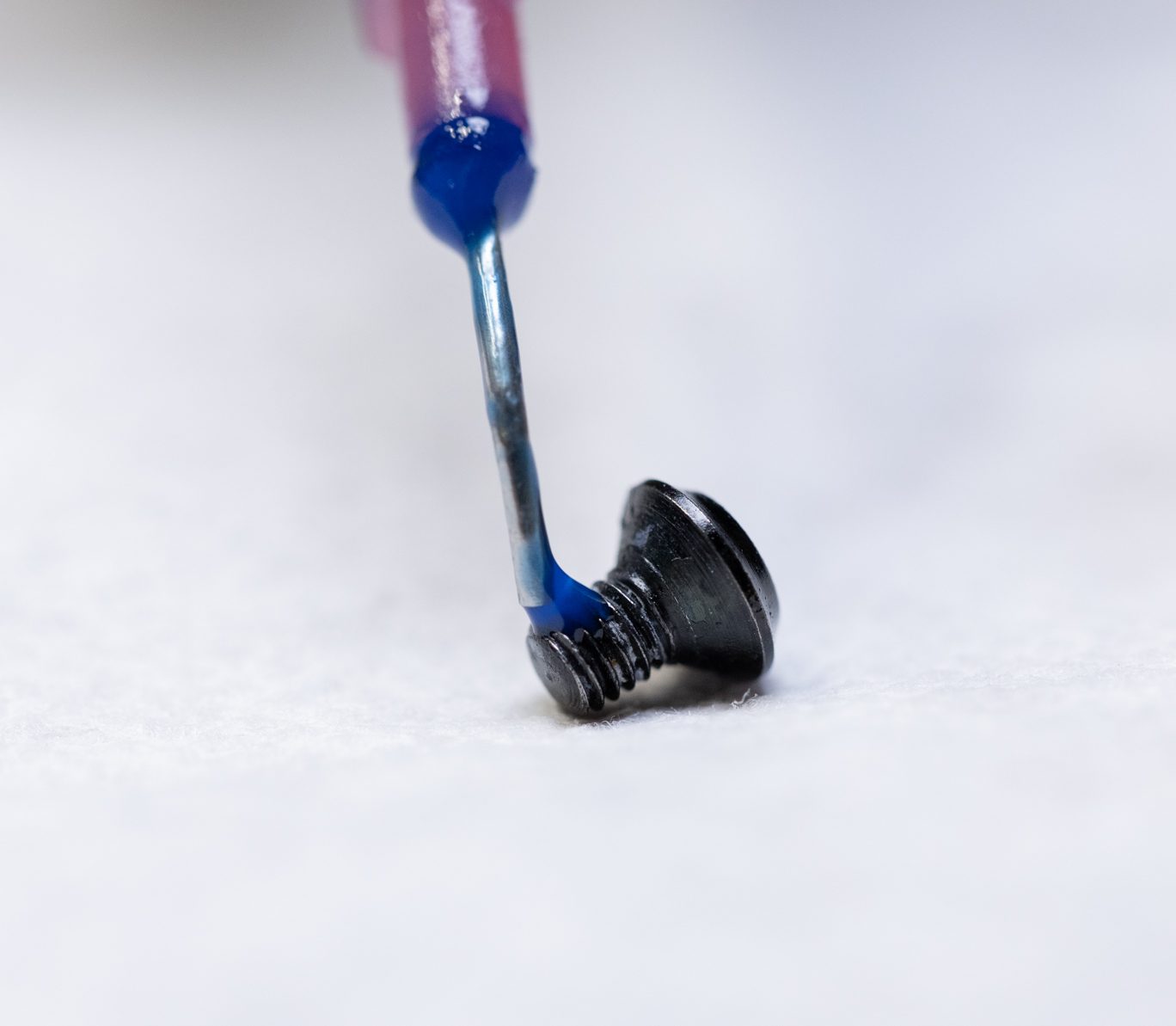
Applying Loctite to LSC Knob Screw
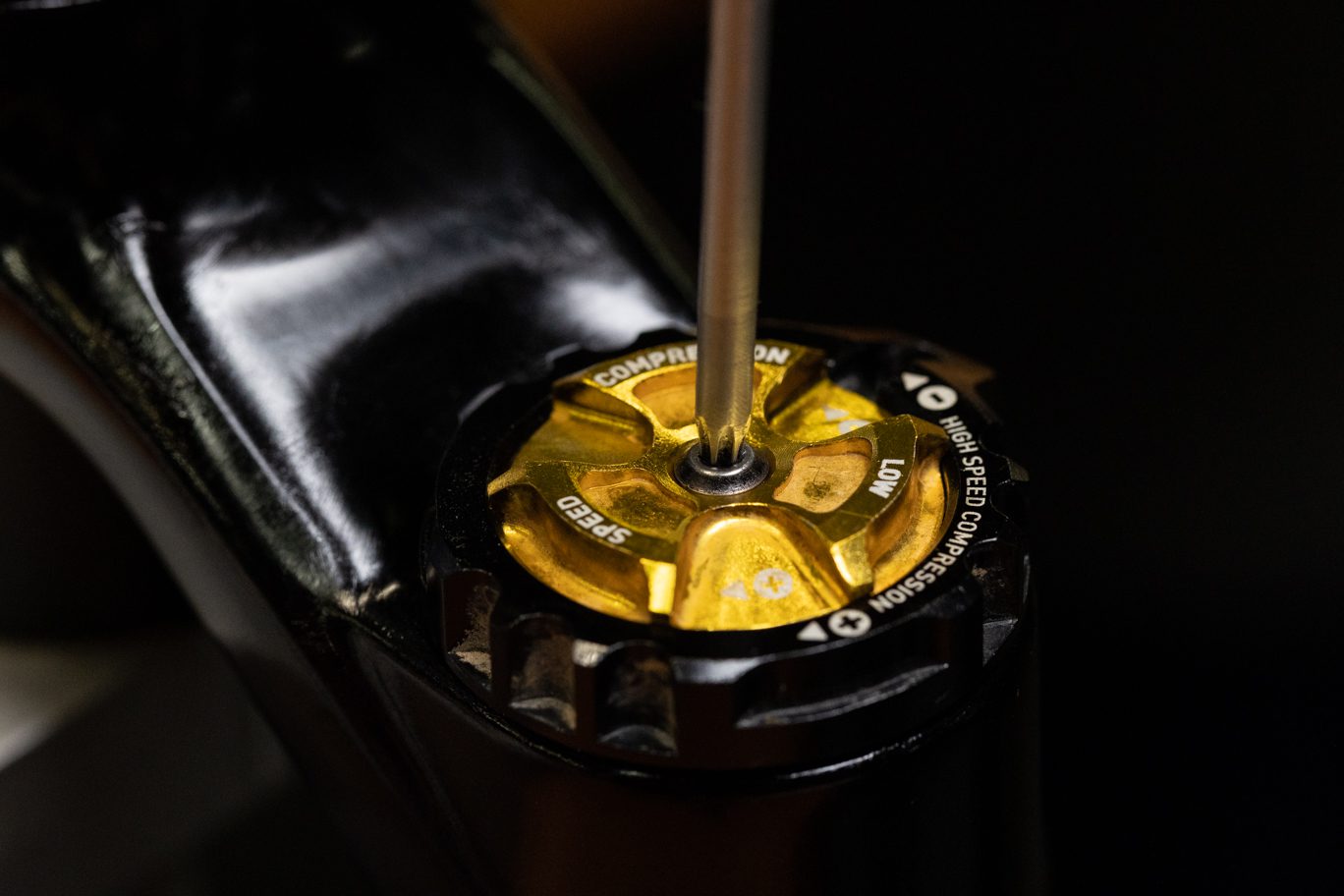
LSC Knob Screw Install
Lower Assembly Install
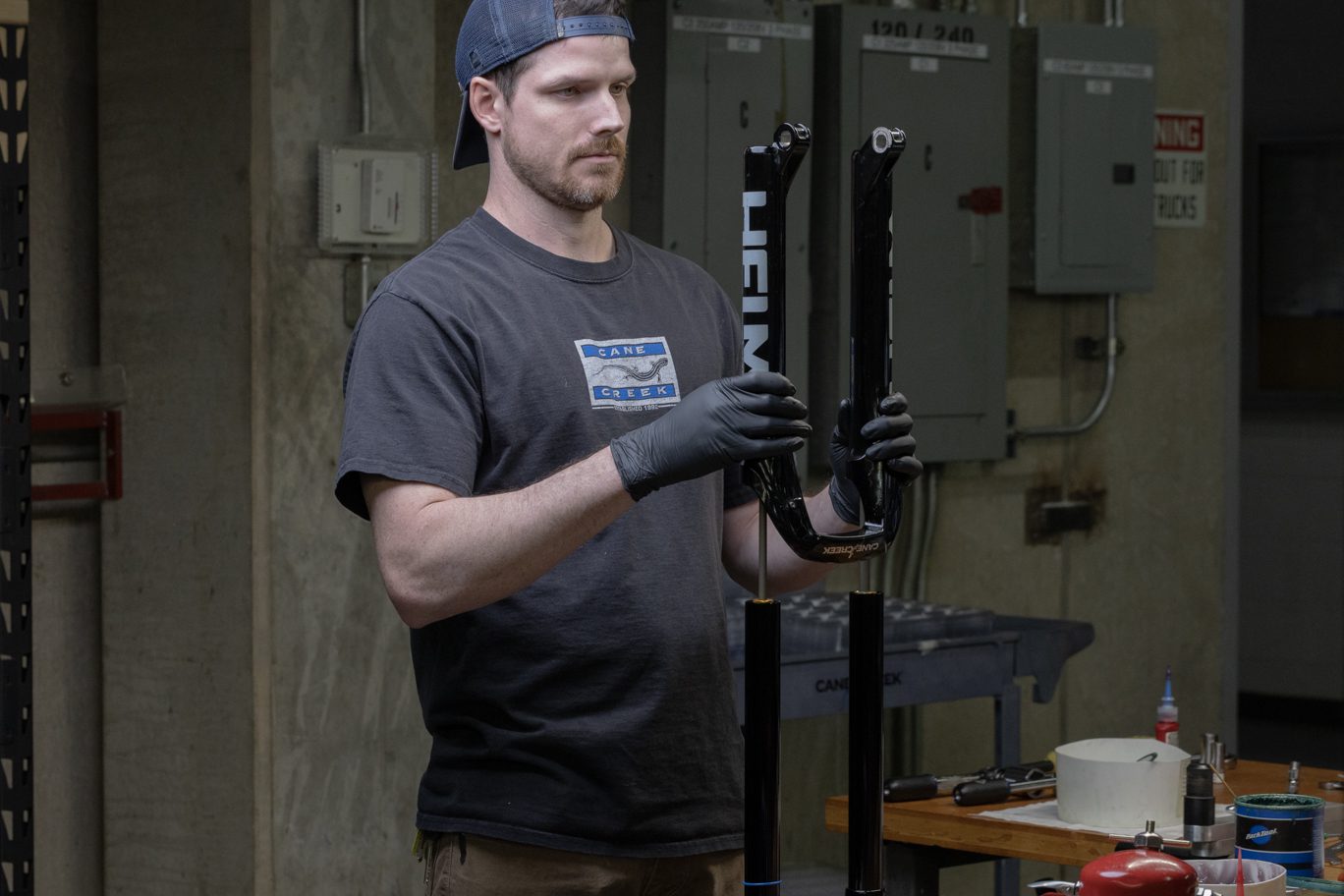
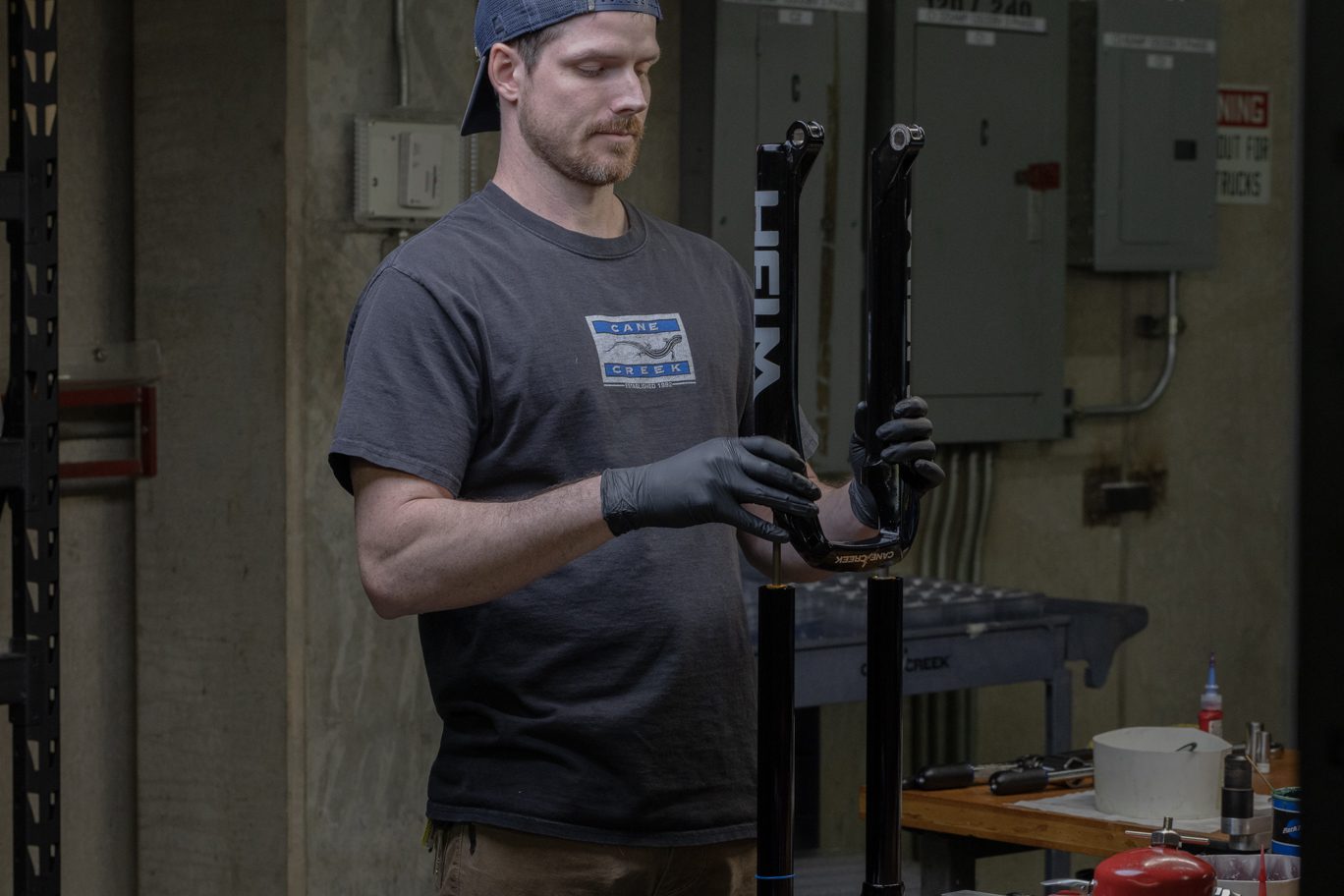
Upon completion of the damper install and any spring side service, install lower assembly per the 50 hour service instructions.
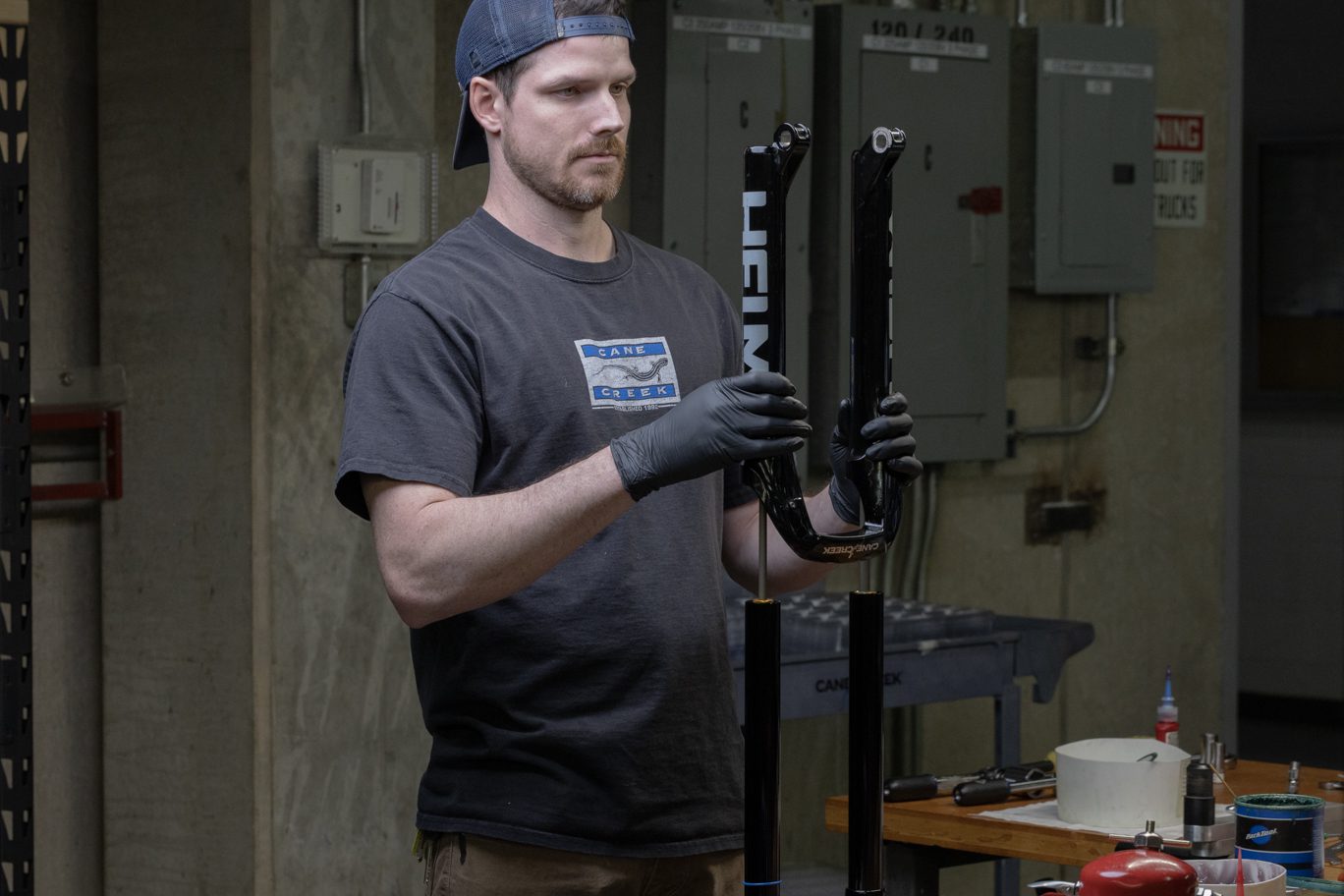
Lowers Install 1
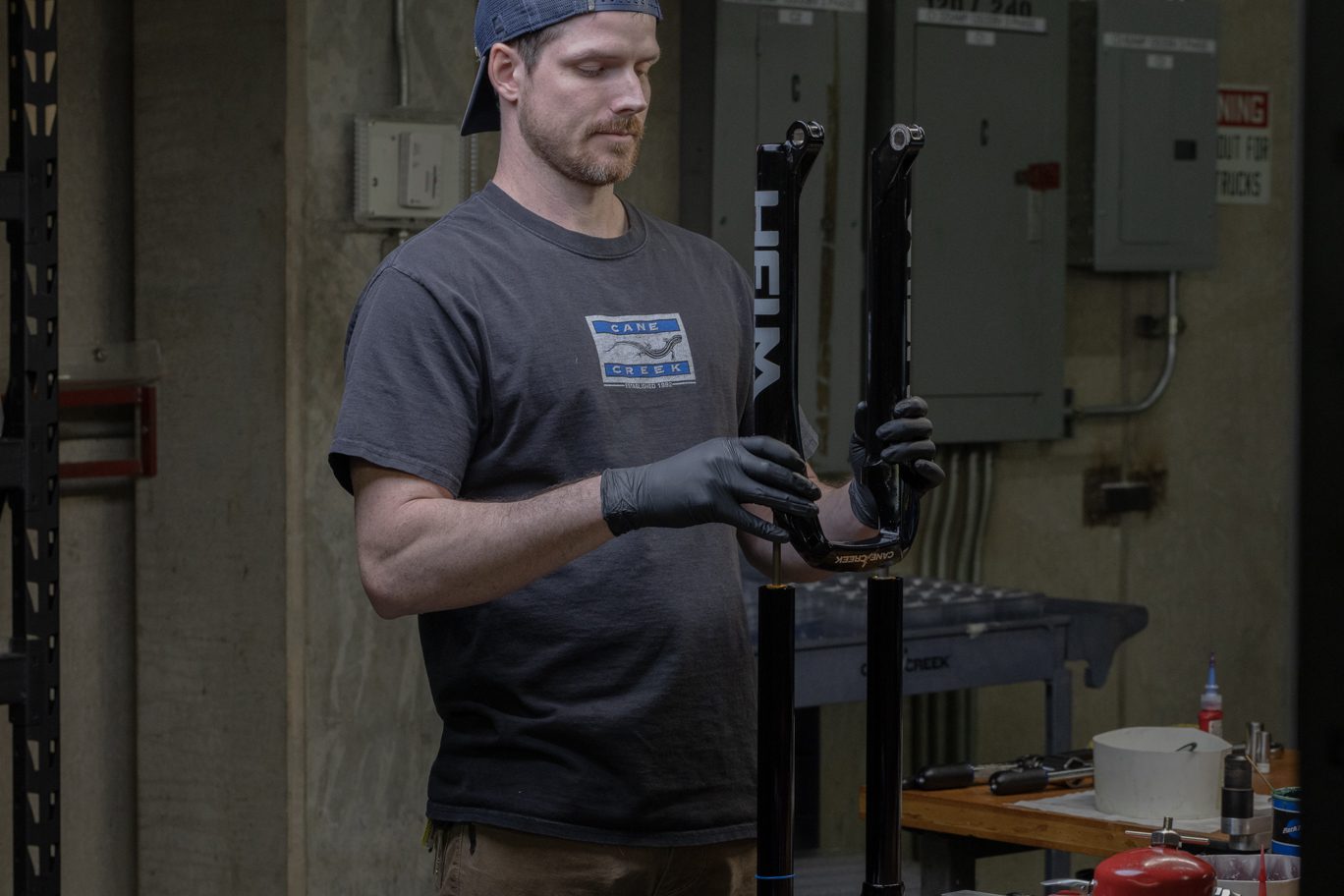